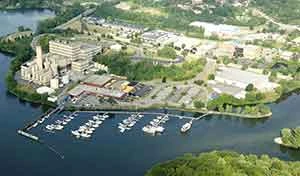
Wheelabrator Westchester and White Plains Linen have announced a first-of-its-kind renewable energy partnership in Peekskill, N.Y., which will enable the county’s largest commercial laundry operation to reduce its carbon footprint by 90 percent.
Under a long-term supply agreement, steam from Wheelabrator Westchester’s waste-to-energy plant is being piped directly to White Plains Linen’s adjacent 100,000-square-foot commercial laundry facility via a newly constructed steam line. White Plains Linen is converting its natural gas-fueled laundry equipment and room heating systems to steam.
When the conversion is complete, White Plains Linen is expected to significantly reduce the amount of natural gas it uses to make steam and hot water, from 1 million therms per year to less than 90,000 therms per year. The reduction in natural gas usage will eliminate 4,775 metric tons of greenhouse gas emissions annually, according to Wheelabrator.
“Westchester County is pleased to support this innovative partnership between two of our larger industrial employers,” says Westchester County Executive Robert Astorino. “It is a great example of how corporate responsibility, especially when it comes to protecting our environment, is also good for business. Considering that more than 50 percent of the waste converted at Wheelabrator Westchester comes directly from ordinary residents in the county’s Refuse Disposal District, it means that we’ll all be contributing to a cleaner, healthier environment in Westchester.”
“This partnership with Wheelabrator Westchester makes White Plains Linen an industry leader in the use of eco-friendly, alternative energy,” says Bruce Botchman, president of White Plains Linen. “By practically eliminating the use of fossil fuels in our laundry operations, we are helping to clean the air, protect the environment and preserve natural resources for future generations. We are proud to make this green investment in our business and in our host community of Peekskill.”
“The stability of this reliable energy source from Wheelabrator Westchester to power our plant will help us to plan our growth strategy for the future,” says Leonard Labonia, vice president of operations for White Plains Linen. “This type of energy source does not react to political unrest overseas or spike due to unforeseen shortages.”
Designed, constructed and operated by Hampton, N.H.-based Wheelabrator Technologies, the Wheelabrator Westchester plant processes up to 2,250 tons per day of municipal solid waste. Inside the plant, waste is transferred to utility-type boilers that recover thermal energy in the form of high pressure steam, which is converted to electrical power by a turbine. The plant generates 60,000 kilowatts of electricity.
“After nearly 30 years of successfully converting post-recycled waste into clean electricity for Westchester homes and businesses, this innovative project puts additional steam from Wheelabrator Westchester to use by a large industrial operation and major employer in the city of Peekskill,” says Mark Weidman, president of Wheelabrator Technologies. “We are proud to partner with White Plains Linen in reducing greenhouse gas emissions and expanding the use of renewable power sources. The reliable delivery of clean energy such as steam to support local industry and economic growth is a business solution we hope to provide to additional customers in the future.”
Since opening in 1984, Wheelabrator Westchester has:
• Processed more than 19 million tons of waste;
• Generated more than 12 million megawatts of electricity; and
• Recycled nearly 520,000 tons of ferrous metals.
Latest from Waste Today
- Reworld acquires R.E.D. Technologies
- Tracey Road Equipment becomes authorized Tana North America dealer
- BTR appoints CEO
- American Biogas Council launches Biogas Carbon Accounting Tool
- GFL completes sale of its Environmental Services business
- EverGen announces updates
- Fleetio launches automation software
- European strategy document favors WTE over landfills on emissions front