
Photo by Shelley Mann
In Phoenix, city officials are working in coordination with Arizona State University to develop a model for a first-of-its-kind circular plastic recycling microfactory with hopes to eventually seed the operating model across the country and even internationally. The initiative is affiliated with Precious Plastic, a global effort started in the Netherlands, that aims to supply communities with guidance, physical blueprints and business models to start their own grassroots plastic recycling program.
Once it is fully operational, the microfactory will convert polypropylene (PP) and polyethylene (PE) collected and sorted by community partners at Goodwill Industries International into plastic pellets to make new products, explains Tyler Eglen of Arizona State’s Walton Sustainability Solutions Service, which is running the factory.
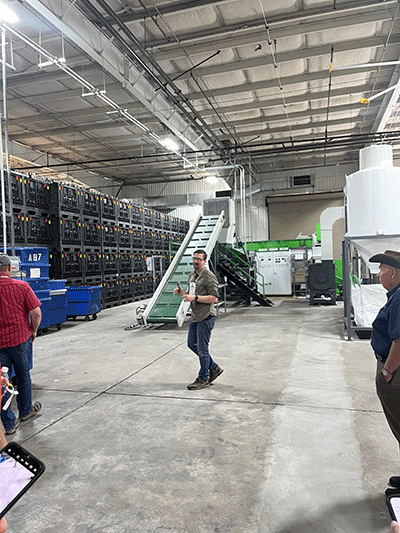
In Phoenix-area Goodwill donation centers, employees are using handheld plastic scanners to search for items made from PP or PP. When they identify eligible items such as home goods, toys, kitchen items and even the plastic totes and tubs used to hold donations, they pull them from the donation stream and set them aside for recycling.
Those collected plastic items are currently being stored at the Arizona State microfactory, where an entire wall is filled with boxes full of salvaged items from more than 100 Goodwill stores.
RELATED: SOAR 2024: Collaboration is key to circular solutions
Located inside the microfactory is a small-scale material recovery facility (MRF), where the sorted and cleaned plastics are transformed into recycled plastic pellets. First, plastics travel up a conveyor belt and into a shredding chamber, where a sieve is used for size control.
Throughout the recycling process, Eglen explains, the plastics are washed again and again to produce the cleanest material possible. The shredded plastic next goes into a water bath, where it is separated. Heavier plastics will sink to the bottom while paper and lighter plastics float at the top.
Clean shredded plastics are then put through a dehydrator, where a vortex of air pulls the material through, kicking out water and fines. Clean plastic flake is dropped into bulk bags to await pelletizing.
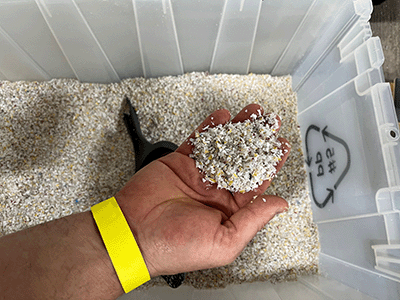
In the Phoenix plastics recycling microfactory, clean dry flakes can be pelletized on site.
“Every step adds value,” Eglen says.
To pelletize the flakes, the microfactory uses an extrusion process to turn flakes into molten plastic logs. That extruded plastic goes through a pelletizer, where a blade chops the plastic into clean pellets that can be sold.
Pellets can be used to manufacture items such as plastic lumber, sporting goods and flat-pack furniture, and different plastics create end products with different textures and grain. So far, during the pilot phase, Eglen and his team have used them to make skateboard decks and basic plastic lumber. These items are not meant to sell, but rather to inspire other communities of the variety of items that can be made from recycled plastic pellets.
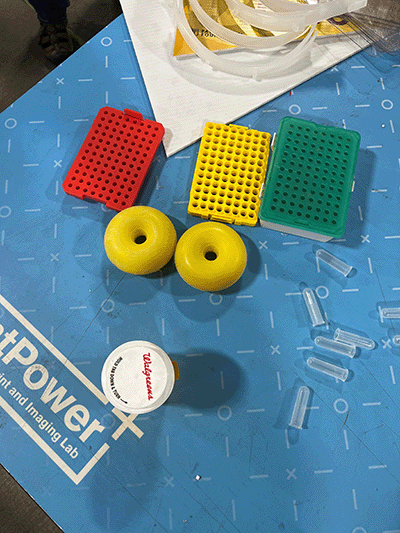
recycled plastic
Because Arizona State has a goal to replicate these microfactories in other communities, the goal was to keep the recycling system as simple and functional as possible, Eglen says, with open-source machines and economical options. The cost to install a similar small-scale MRF would be about a half-million dollars, he said, and the organizers’ ultimate dream for these plastic recycling microfactories is for them to become worker-owned cooperatives.
Because the plastic lumber and other products coming out of the microfactory will be made with 100 percent PE or PP, those end products can be recycled again and again—the ultimate closed loop recycling system.
Latest from Waste Today
- ReMA board to consider changes to residential dual-, single-stream MRF specifications
- Miller Environmental Group Inc. appoints CEO
- DPI acquires Concept Plastics Co.
- Laurel Mountain Capital announces investment in 5280 Waste Solutions
- Cielo investor requests annual meeting
- WIH Resource Group celebrates 20th anniversary
- NWRA: NIOSH cuts a step in the wrong direction
- Valicor Environmental services acquires Affordable Waste Management