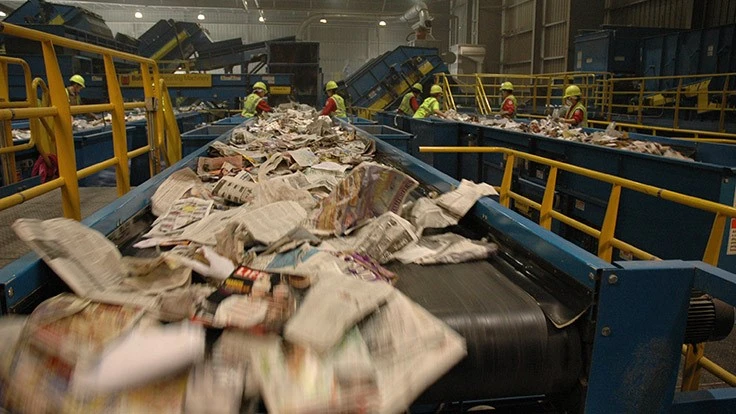
Quality is king when it comes to the output material recovery facilities (MRFs) are being called on to generate. Faced with shrinking global end markets, MRF operators are using advanced technology to help cut contamination rates and improve the overall quality of their bales. Two types of equipment that are on the front line of this battle are optical sorters and artificial intelligence (AI)-equipped machines, commonly known as robots.
While optical sorters have been used in MRFs for years, robotics are just now gaining traction with recyclers. Together, industry sources say these tools can greatly enhance a facility’s material recovery capacity, increase revenue and overcome human limitations in sorting.
Choosing the right equipment
A MRF operator should outline what the business’s goals are when considering new sorting equipment. Due diligence is required before purchase to assess how new equipment might help the MRF achieve these goals.
“The first step is to understand the capabilities of both an optical sorter and a robot,” Adam Lovewell, process engineer for Van Dyk Recycling Solutions, Stamford, Connecticut, says. “The second step is to evaluate where you need to replace equipment or manual sorting with automated sorting. And the third step is deciding how many picks per minute need to be made, what the picks are, and where they need to go.”
Nathiel Egosi, president and CEO of RRT Design & Construction, Melville, New York, says understanding the cost and subsequent benefits of an equipment purchase can be instrumental in helping decide the merits of investment.
“When considering capital upgrades, such as opticals or robotics, undertaking a costs/benefit analysis and return-on-investment calculation should be performed. One should take into account all relevant operating parameters including, but not limited to, feedstock quality and composition, throughput requirements (low, average and high throughout the day and year) and end product quality requirements,” Egosi says. “From these, an assessment of the efficiency increase(s) and cost implications can be determined, and from which, a decision can be made on where or how to start [incorporating new equipment].”
According to Egosi, an operator should ask the following questions before deciding on implementing new optical sorters or robotics:
- What am I trying to achieve, or what is the problem I need to solve?
- What are the risks of doing nothing?
- What are the potential rewards (e.g. operational, financial) of making a change?
- What are the conditions that need to be met to give the best chance of success by making a change?
Understanding differences and applications
The industry’s latest robotic sorting machines use some of the same technology that has been incorporated in optical sorters for years.
While both systems feature high-speed, high-resolution cameras, three-dimensional sensors and near-infrared optics used to identify and sort waste, optical sorters use jets of air to change the trajectory of material toward the desired location. Robotic sorters use an armature with either a suction or a grappling capability to pick one item at a time and transfer it to the desired location.
Optical sorters are still 10 times faster than robotics, capable of roughly 600 picks per minute compared to the 60 picks per minute capacity of most robots, but both are accurate. A primary difference between the two is that robotic systems use algorithms and programming software designed for improved sorting capacity over time. In effect, these machines learn how to be more efficient the more they are used.
Although robots can be programmed to be more sophisticated in the materials they pick, the speed differential between the two types of systems confines their use to certain roles in a MRF.
According to Lovewell, operators should weigh the strengths of these machines when considering their potential application in their facility.
“Optical sorters are best suited for fiber sorting and container sorting in medium- to high-volume plants,” Lovewell says. “Robots will be best suited for sorting containers in low-volume plants, maintaining quality control of ejected containers (from an optical sorter) on the container line and for the recovery of missed recyclables on the final residue recovery line.”
Because of their differences in capacity, operators need to come up with a plan that best allows these machines to target materials in the waste stream for optimal efficiency. Getting the most out of these machines takes intricate planning in system design so as not to overwhelm the equipment with a stream configuration it can’t efficiently handle.
“Optical sorters and robotic sorters may work in two different areas of a MRF,” Bruce Clark, project director for SCS Engineers, Long Beach, California, says. “For heavy volumes of a few related commodities (i.e., plastic containers) the optical sorters would be located closer to the front end of the MRF, potentially following an initial separation of light materials versus heavy materials and/or two-dimensional items such as fiber and paper from three-dimensional items (i.e., containers) by other equipment such as a screen or drum.
“In general, a robotic sorter would likely perform better anywhere in the MRF where there is some presorting to spread material evenly across the belt and remove oversize and bulky material, or two-dimensional material like paper and foil, that can obscure the targeted material(s),” he continues.
Clark says a MRF’s control systems are typically upgraded when optics or robotics are installed to provide the operator more local control of all sorting equipment on the line, more flexibility to address waste stream changes and simpler control interfaces.
Weighing the options
Once an operator makes the decision to purchase new equipment, the process of shopping for the right solution begins. There are a number of different MRF sorting technology providers. Although cost is a major factor that will influence an operator’s purchasing decision, it shouldn’t be the only consideration.
Clark advises reading up on system information via trade publications, inquiring about system performance with other operators and talking with experienced consultants and vendors to narrow down the best option for a facility’s needs. This information can then be used as a resource when vetting providers.
“Allow companies to come into your facility and make an initial assessment, review data you may have on material volume, material changes and percent recovery and residue. Then request a written report,” Clark says. “That report should include: feasibility of employing the machine(s), expected tangible improvements (i.e., rate of recovery, reduction of residue, removal of additional targeted material(s), etc.) any other modifications needed to your system to allow the new equipment to perform properly, a budget cost estimate or range, and estimated operating costs.”
Clark suggests sending a representative waste stream sample to potential vendors and having that run through the vendor’s test facilities to gauge the equipment’s effectiveness. He also advises operators to visit facilities currently running the equipment under consideration for purchase to see how it operates in person. If visiting a site isn’t possible, he suggests reviewing a site’s system layout and analyzing its efficiency results.
Lovewell says it is important to know the provider when investing in new equipment. Parts and service are a big component of efficiently running these machines. Companies should choose providers who will be able to offer support throughout the life of the equipment.
“A big mistake we see is companies choosing to invest in [equipment] that does not have parts and service representation in the United States,” Lovewell says. “Waiting six weeks for parts to run your machine is not a fun situation.”
Lovewell advises to assess a manufacturer’s track record and reputation before committing to a provider, as this can help give operators peace of mind when parts and service are needed.
Planning for the future
Equipment is always changing Although it is impossible to “future proof” a facility in a way that makes upgrades unnecessary down the line, there are still ways operators can implement sorting equipment to plan for the future.
According to Lovewell, operators need to stay one step ahead when deciding on system upgrades to make the addition of equipment in the future seamless.
“It is easier said than done, but operators should always plan for future equipment. If you do not have the capital to add optical sorters or robots during the initial design/installation phase, make sure you have adequate room to add down the road,” Lovewell says. “Both opticals and robots will be pieces to the overall puzzle, as will nonwrapping screens, ballistic separators and other equipment that better prepares the material and singulates it for optical sorters and robots.”
Because incoming material composition and output demand are ever-changing, Egosi advises choosing equipment in a way that allows companies to be flexible in meeting oncoming challenges.
“For new MRF builds, bigger is better. As technology advances and the input compositions continue to change, equipment retrofits and upgrades are always inevitable typically within a 10 to 15 year period of time—often even sooner,” he says. “Allowing room for reconfiguration is a best practice. For existing facilities where upgrading is desired, equipment upgrading can be a challenge, but one that is not insurmountable. Knowing your business is vital to making the best decision possible. If tonnage is expected to increase or remain static but the demand for higher quality bales is expected, greater separation and quality control efficiencies are an absolute must. Investments made in operational efficiency, whether technological or nontechnical, will enable MRFs to manage materials effectively and efficiently under a variety of operating conditions.”
There is no equipment on the market today that can completely negate the need for human involvement in sorting operations. However, as sorting equipment becomes more sophisticated, MRFs across the country will continue to realize greater purity and more opportunities for diversion, which is a positive for both operators and the public at large.
The author is the editor of Waste Today and can be contacted at aredling@gie.net.
Latest from Waste Today
- SECCRA signs up for landfill gas-to-energy system
- Hyster-Yale commits to US production
- VLS Environmental Solutions acquires Virginia waste management services provider
- Republic Services opens Colorado hauling facility
- G2 Energy, Waga Energy to produce RNG at 2 Recology landfills
- Massachusetts awards $4 million in waste and recycling grants
- WM announces 2025 dividend increase
- Vanguard Renewables names new CEO