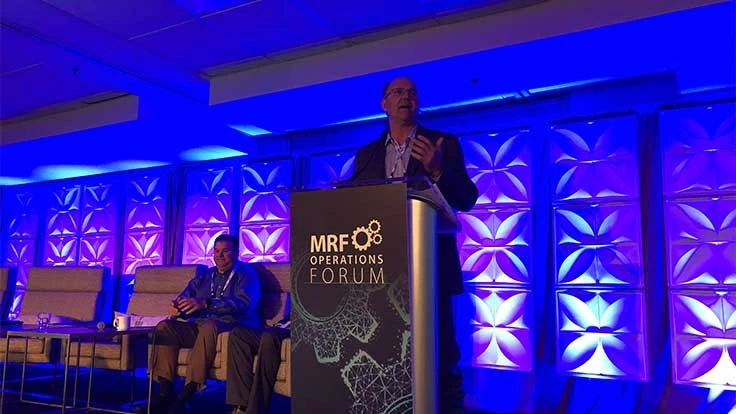
Megan Smalley
The inbound material stream at material recovery facilities (MRFs) is vastly different in 2019 from what MRFs experienced just a decade ago. For instance, MRFs about 10 years ago may have desired to bale an old newspaper (ONP) fiber grade more than mixed paper, yet the ONP grade has been dwindling to extinction in recent years. Also, with single-stream facilities, contamination is a regular concern and varies from community to community.
Adding optical sorters or automated equipment could be a solution to these problems, but some MRFs are strapped for cash and that’s not an answer. During the MRF Operations Forum Oct. 22 in Chicago, Mark Henke, senior manager of recycling at Phoenix-based Republic Services, and Jim Marcinko, vice president of recycling operations at Houston-based Waste Management, offered some of their suggestions for what MRFs could do to improve both throughput and uptime when there’s not existing capital to improve.
Improve throughput with no money
All MRFs need to produce good quality material and equipment can certainly help to improve the quality of that material—yet sometimes it’s not possible to make a big investment in a new optical sorter or screen. “Not everybody can have [a brand new system] and you still need to produce quality,” Henke said.
In MRFs, a 3-to-5-year-old system isn’t designed to handle current material streams or quality specifications, he said. Also, screens and other pieces of equipment diminish in quality over time and wear down with contamination.
Henke shared a few ways MRFs can improve their throughput levels without capital investments:
• Collaborate with mills and end markets: Henke said it’s important today for MRFs to know their end markets. “It’s not just knowing where you’re taking the material; know what their final product is,” he said. “What is the recipe [mills] need? What can they tolerate? What is a deterrent to them? Be their partner. And make sure they understand what you’re up against as an operator on inbound quality.” He suggested MRF operators to tour mills to get to learn their needs better and invite them to visit the MRF as well.
• Sorter placement is key: Have a solid plan on where to place each sorter. Henke suggested MRF operators have sorter responsibility charts to layout each station and where everyone should go. In addition to machine separation, it’s important to have good quality sorters on the line. He advised MRF operators determine where each sorter works best. He said that might mean moving sorters around occasionally so that they don’t get bored, too. “Take sorters to their optimal location so they can do their jobs,” he said.
Improve uptime with no money

A number of issues cause downtime at MRFs—mechanical failures, scheduled maintenance, operational issues and even things such as employees going out to a company lunch or needing to take time off. Downtime is going to happen, so it’s important that MRFs work as efficiently as possible outside of these occurrences.
“Uptime is everything,” Marcinko said. “If a conveyor belt isn’t moving, we’re not generating anything out of the back end.”
Marcinko shared a few ways MRFs can increase uptime without investing in new equipment:
• Determine realistic production capacity: To ensure efficiency, Marcinko said MRF operators need to know the material stream composition, and they also need to know what the mills and end markets want from these commodities. He said production requirements differ depending on the stream’s composition. While operating faster will create more bales to sell, it might be more worth it to slow the line to create a cleaner bale. He said knowing the exact levels of contamination can help operators know whether they need to slow down the line to create a cleaner end product.
• Gather data: Be consistent with taking notes on what is causing jams on the line and track how long downtime is needed for lunch and breaks. Marcinko said it’s helpful to track where jams occur to prevent them from reoccurring in the future. “If you don’t have data, it’s all speculation,” he said.
• Set employees up for success: To reduce the chance of turnover, provide maintenance and operators with tools for success, Marcinko said. He suggested giving operators iPads to check off preventive maintenance tasks to make that process easier. He also said it’s good to track teams to measure their performance and to give each team goals to meet under deadlines. Additionally, he stressed the importance of providing employees with a clean workplace they can be proud of. “Efforts like this lead to better success and longer term employees,” he said, which reduces downtime caused by turnover.
Latest from Waste Today
- Yanmar CE launches full line of compact equipment
- EC Waste acquires fellow Puerto Rican hauling firm
- Goldman Sachs Alternatives to acquire Liquid Environmental Solutions
- Block Island Recycling Management Inc. aims to promote environmental stewardship
- Miami region officials seek WTE plant location
- Clean Harbors faces potential penalty for Ohio fatality
- New Hampshire governor signs leachate management bill
- MSS relocates to new facility in Nashville, Tennessee