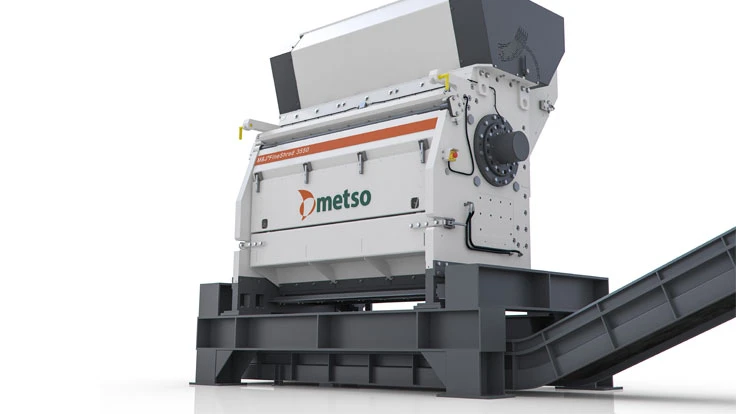
Helsinki, Finald-based Metso’s M&J FineShred 1550 and 3550 are the company’s new single shaft fine-shredders with vertical feed by a pusher for use in refuse derived fuel (RDF) production.
The shredders can deliver a throughput up to 17 tons per hour, depending on the output size, and has a homogeneous output from 10 to 100 millimeters.
“We saw a need in the market for single shaft fine-shredders with in-line feeding,” Uffe Hansen, senior vice president of Metso Waste Recycling, says. “These new shredders have an unbeatable price performance and delivers a super stable and homogeneous output which increases the value of RDF.”
The multi-edged shaft is fitted with a patented knife system and is fed by a pusher designed to avoid forcing material onto the shaft, and a small amount of heat is generated. The hydraulic drive of the shaft is designed to reduce power peak on the grid.
“Our goal was to create a shredder with vertical feed at a competitive price without compromising on Metso's usual high quality,” Johannes Kjærsgaard, manager of technology development at Metso Waste Recycling, says. “Its great force is that it can shred almost any material into very small scale and ensure a completely uniform result without crumbs.”
Features of the shredders include:
- The shaft can be fitted with a number of different cutting tools. Knife blocks are positioned firmly in the shaft using a self-centering, distortion- and tilt-safe assembly. The geometry of the 12-edged shaft is designed to minimize the risk of materials getting entangled and prevents the machine from heating up.
- Knives are available in different designs to suit the demands from different applications. The positioning of counter knives in relation to rotating knives delivers a clean cut designed to minimize dust emissions. Cutting clearance is adjusted using the notches provided.
- The hydraulic system consists of a variable pump with power control, an integrated feed pump and a hydraulic motor mounted on each shaft.
- The precise cutting of material is designed to minimize the strain on the screens. The absence of pressure on the screen means the open area can be optimized to ensure a high output rate. Granules can be discharged using screw or belt conveyors.
- Knives and knife holders are designed for easy fastening and changing. The service hatch on the outside of the two one-shafted machines is designed for easy access to service the shaft or change the knives.
Latest from Waste Today
- Goldman Sachs Alternatives to acquire Liquid Environmental Solutions
- Block Island Recycling Management Inc. aims to promote environmental stewardship
- Miami region officials seek WTE plant location
- Clean Harbors faces potential penalty for Ohio fatality
- New Hampshire governor signs leachate management bill
- MSS relocates to new facility in Nashville, Tennessee
- Houston weighs adding a solid waste fee
- Smith & Loveless highlights wastewater treatment system