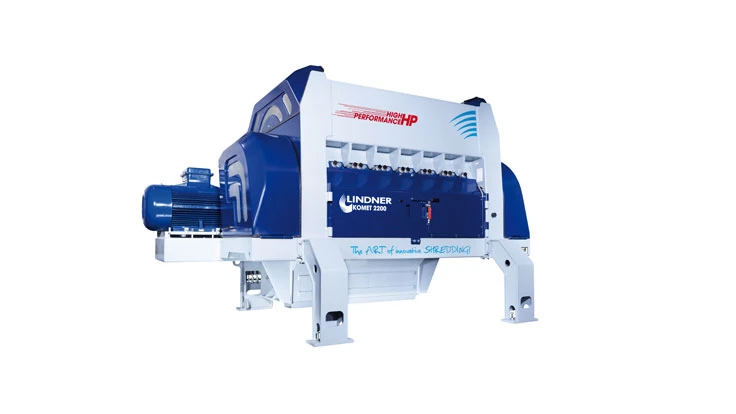
The Lindner Komet 2800, from Austria-based Lindner and available in the U.S. through Raleigh, North Carolina-based Lindner America LLC, is described by the company as a powerful, high-capacity single-shaft shredder that is primarily used for the efficient shredding (granulation) of a range of different preshredded waste such as commercial and industrial waste, paper, cardboard, files, containers, mixed plastics, rubber, leather, textiles, floor covering, cables and electronics scrap without impurities and by dosed feeding. The resultant output material is a defined granulate for subsequent processing (cutting mill, compactor) or as final refuse-derived fuel (RDF) product. The Lindner Komet 2800 can be optimally adapted for different applications by individual configuration and equipment components. The company touts the following features:
- low cost per ton expense, due to high output and four times the usable knives as other shredders;
- output rates of up to 30 tons per hour of 2-inch minus RDF;
- with hundreds of Komet shredders installed worldwide, customers can have confidence in numbers, the company says;
- a maintenance-friendly design with high emphasis on ergonomics; and
- 15-year track record and successive design improvements
According to the company, the machine lives up to highest quality standards and typifies durability, maximum availability, cost effectiveness and operational safety. The massive, vibration and noise-damped machine housing – designed for heavy industrial use – is supported by buffer and leveling elements to provide for low-vibration operations. The double-walled construction in the area of the rotor bearing provides protection against bearing damages caused by pollution. Lindner says the service-friendly construction offers conceptual and practical advantages, low-maintenance operations and facilitates a quick change of cutting knives and a simple replacement of washers between the rotor and housing. The counter knives as well as the scrapers are easily segmental adjustable outside the cutting chamber, the company adds. Fourfold useable knives segments made of high wear-resistant tool steel guarantee the best rotor cutting performance.
The power system of the Lindner Komet 2800 with its belt drive system (single stage) is extremely robust and very low maintenance, the company adds. When compared with gear drives, the direct drive gives a system with improved operational characteristics such as efficiency, maintenance, wear, noise level and throughput capacity, while the omission of a mechanical transmission leads to a high degree of rigidity.
The inwards opening, hydraulically driven Lindner maintenance and foreign part flap provides fast and unobstructed access to the rotor and ensures ergonomic turning/change of knives. Large maintenance doors allow for best possible access to the hydraulically traversable screen cassette and the scrapers. The individual modules of the screen made of high wear-resistant steel are not bolted together but elastically clamped and therefore can be replaced simply and quickly.
In case of foreign part collisions, the power drive components (motors, drive shafts, v-belts) are protected by safety clutches that are mounted directly on the rotor shaft. The high rotor mass, which is advantageous for the shredding process, is uncoupled in split seconds.
The hydraulically operated internal pusher, the “rammer”, only connects to the outside via the drive shaft. This means no ducting of component parts through the casing and no sealing – with the virtually enclosed shredding chamber, dirt outside of the machine is history. The entire system – proportionally controlled and buffered – is low wear and maintenance free, except for the hydraulic drive.
By using modern frequency converter technology (recommended option), efficiency, torque and starting currents are optimized so that operations are more energy efficient and cost-effective. The investment in the frequency converter for the Lindner Komet 2800 will pay for itself within a very short period of time, according to the company.
The Lindner Komet 2800 comes standard with the intelligent basic controller with an 8-inch touch panel. This provides adjustment to different, even difficult materials. Saved electrical drawings and spare parts lists as well as a variety of parameters, maintenance intervals, machine status and malfunctions (up to 1000 messages) are sorted by date and time and shown on the display. Software or changes are imported by USB stick or via Internet connection, which can also be used for remote maintenance.
All electrotechnical components built into the machine except for motors are wired and connected to an operator's panel. All electrotechnical components built into the hydraulic unit except for the pump motor and any tank heating are wired and connected to a terminal box.
The control and signal lines routed to the operator's panel and terminal box are connected to the electrical cabinet by multipolar cables indicated in a cable list. Motor cables are part of this cable list as well. The connection cabling is executed in accordance with the specifications of the cable list either by the customer or optionally by L-RT. More information is available at www.l-rt.us.
Latest from Waste Today
- Commentary: The rise of scam listings on waste and recycling platforms calls for vigilance
- New Hampshire lawmakers introduce leachate management bill
- Heritage Environmental Services appoints chief commercial officer
- Ripple Glass launches commercial glass collection program in Atlanta
- Veolia, MassBio partner with GreenLabs Recycling for medical waste plastics recycling
- NWRA, SWANA issue joint response to Bureau of Labor Statistics fatality data
- Former WM executive joins Amp board
- Heritage Environmental Services invests in hazardous waste shredder