
Photo by Neal Bolton
When I was 12, our family went to see the Harlem Globetrotters. This was during an era when Meadowlark Lemon and Curly Neal were leading that team. It was amazing, incredible and magical to watch them. They made the impossible look easy.
I came home from that event, liquidated my savings and bought a new basketball. Then I started working on my trick shots. I had the equipment. I had the motivation. But I wasn’t getting the results I wanted. Something was missing.
Before long, I discarded my dreams of being a globetrotter and settled for just being one of the guys on the 7th grade basketball team.
Sound familiar? I wonder how many landfill managers have liquidated their savings and bought a new landfill compactor, only to quickly give up on those dreams and become just another guy with a basketball?
Well, in this article, I’d like to share some ways that top landfill performers are using their compactors to achieve amazing, incredible and, yes, even magical results.
The idea that a steel-wheeled landfill compactor can pack more trash into the limited space of a landfill is a simple one—it makes sense. But it’s the step between the tool and the result where many folks stumble. It may not be rocket science but, brother, it is science.
Let me start with a little history lesson—a lesson on landfill compactors. Fred Caron (founder of Caron Compactor Company) unveiled the first landfill compactor, the Pactor, in the 1960s. He understood—long before anyone else—that waste compaction was a vital part of running a landfill. Since that time, the Caron Compactor Company has stood for innovation when it comes to landfill waste compaction. You’d think that would have been enough time for the landfill industry to figure this out.
Yet here we are, more than half a century later, still trying to apply some basic laws of physics to something as obscure as waste compaction. I’m not saying that as an industry we’re slow on the uptake but, surely, it’s about time we put some science into the compaction process.
Manage the moisture
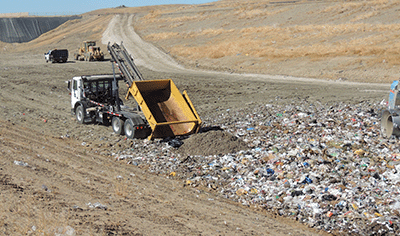
Much of the organic portion of trash consists of cellulose fibers. That includes wood, green waste, paper, cardboard and many other subtypes of materials. The thing about cellulose fibers is that they are rigid and can hold their shape against some very strong forces. They can resist bending, flexing and compressing … when dry. But when wet, those cellulose fibers lose much of their strength. They soften and are much more susceptible to the compressive force of a landfill compactor.
That’s why experienced operators are always looking for ways to get some moisture into dry loads made up of cellulose fibers. Residential trash, sludge and food waste are common sources of moisture in the waste stream.
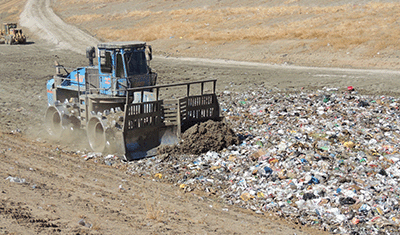
Some landfills go so far as to spray liquid on the active face to minimize dust and litter—and to increase compaction. As a rule of thumb, we’ve found that 25-30 gallons of liquid applied per ton of waste is adequate to improve compaction, without generating free liquid that could create other issues. Of course, there are many variables, and every landfill would have its own recipe.
The point is, though, that moisture can be beneficial in providing higher rates of compaction.
Spread waste in thin layers
The downward force of a landfill compactor spreads out with depth, looking like a subsurface pyramid. And at some point, the weight of the compactor would not be felt at all. This happens at a much shallower depth than most people imagine.
Even at depths of just 4-6 feet, the weight of the heaviest landfill compactor would not crush pallets or break bottles.
Have you ever seen a contractor dump a load of soil to build a ramp when crossing a concrete curb? That soil ramp acts like a bridge to help dissipate (spread out) the force exerted by a heavy truck or tractor, thereby protecting the concrete curb from damage. Well, that 4-6 feet of trash creates the same type of “bridge” that inhibits the compactive force of a landfill compactor. We don’t want bridges.
To achieve optimum compaction, the compactor’s teeth should fully extend through each layer of trash. That way, every bit of trash that goes into your landfill is impacted by the teeth.
For that reason, trash should be spread in thin layers to maximize the force applied to all waste. You’ve probably heard of the 2-foot rule. Even here, there is science.
When uncompacted trash is spread across the active face, it has a density of approximately 400 pounds per cubic yard (pcy). After the first pass with the compactor, the density has increased 250 percent, to around 1,000 pcy. Accordingly, that initial 24-inch layer is compressed to less than 10 inches, which is close to the tooth height on many compactors.
Keep in mind that as those compactor teeth wear, waste must be spread in thinner lifts to achieve that same full-length penetration. The solution here is to continue reducing the layer thickness or replace the compactor teeth more frequently. Studies indicate that more frequent tooth replacement saves airspace and makes financial sense.
Work flat
The downward force of a landfill compactor spreads out with depth, looking like a subsurface pyramid. And at some point, the weight of the compactor would not be felt at all. This happens at a much shallower depth than most people imagine.
Even at depths of just 4-6 feet, the weight of the heaviest landfill compactor would not crush pallets or break bottles.
Have you ever seen a contractor dump a load of soil to build a ramp when crossing a concrete curb? That soil ramp acts like a bridge to help dissipate (spread out) the force exerted by a heavy truck or tractor, thereby protecting the concrete curb from damage. Well, that 4-6 feet of trash creates the same type of “bridge” that inhibits the compactive force of a landfill compactor. We don’t want bridges.
To achieve optimum compaction, the compactor’s teeth should fully extend through each layer of trash. That way, every bit of trash that goes into your landfill is impacted by the teeth.
For that reason, trash should be spread in thin layers to maximize the force applied to all waste. You’ve probably heard of the 2-foot rule. Even here, there is science.
When uncompacted trash is spread across the active face, it has a density of approximately 400 pounds per cubic yard (pcy). After the first pass with the compactor, the density has increased 250 percent, to around 1,000 pcy. Accordingly, that initial 24-inch layer is compressed to less than 10 inches, which is close to the tooth height on many compactors.
Keep in mind that as those compactor teeth wear, waste must be spread in thinner lifts to achieve that same full-length penetration. The solution here is to continue reducing the layer thickness or replace the compactor teeth more frequently. Studies indicate that more frequent tooth replacement saves airspace and makes financial sense.
Make long runs
Landfill compactors are at their peak productivity when traveling at full speed—even if it’s only 3 miles per hour. But at the end of every run, that machine must slow down, stop, reverse direction and then accelerate back up to production mode. This is lost time and it is nonproductive time.
From the perspective of maximizing the compactor’s productivity, long runs are better because the machine spends a greater percentage of time at full speed,= and less time slowing, stopping, reversing and accelerating. You get the idea.
If you are covering with soil, the concept of making long runs is in direct conflict with the idea of maintaining a tiny active face to minimize cover soil usage. I remember when this was standard practice. But conditions have changed, and for landfills that are using ADC, the cost of covering a bit more active face at the end of the day is a small price to pay for the increased density you’ll get from longer runs with the compactor.
Compact thoroughly
Landfill compactors are at their peak productivity when traveling at full speed—even if it’s only 3 miles per hour. But at the end of every run, that machine must slow down, stop, reverse direction and then accelerate back up to production mode. This is lost time and it is nonproductive time.
From the perspective of maximizing the compactor’s productivity, long runs are better because the machine spends a greater percentage of time at full speed,= and less time slowing, stopping, reversing and accelerating. You get the idea.
If you are covering with soil, the concept of making long runs is in direct conflict with the idea of maintaining a tiny active face to minimize cover soil usage. I remember when this was standard practice. But conditions have changed, and for landfills that are using ADC, the cost of covering a bit more active face at the end of the day is a small price to pay for the increased density you’ll get from longer runs with the compactor.
Use aggressive teeth
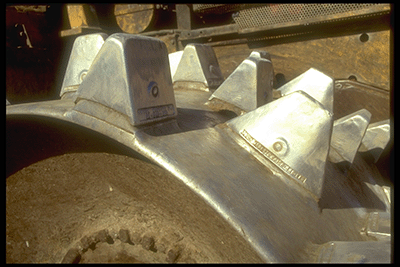
When it comes to teeth on your landfill compactors, size matters. Compactors with big teeth and lots of teeth will consistently get the best results. You may save money by going with smaller teeth, or by spacing them out on the wheel to have fewer teeth. But those savings only consider your upfront costs. In the long run, the cost of airspace trumps everything else.
Larger teeth have greater demolition ability. They can also reach further into every layer of waste to ensure thorough compaction.
Tooth spacing is also an important topic. Think about this. Have you ever seen a landfill compactor that was not achieving full depth penetration with the teeth? In other words, have you ever seen daylight between the drum and the trash? I have not. That indicates that a denser tooth pattern would be effective at putting more teeth into the trash.
The one drawback is that a dense tooth pattern can exacerbate wheel packing, where mud or sticky waste gets stuck between the teeth and the compactor ends up working as a smooth-drum roller, rather than a toothed compactor.
This can be mitigated by installing cleaner bars on the machine. Some compactors are designed with cleaner bars on all wheels. The operator can also help prevent wheel packing by staying on the trash and not traveling across areas of wet soil.
There are many factors to consider when selecting the right tooth design, size and placement pattern for your compactor. Just be aware that your decisions matter.
Prep for cover
Waste compaction ranks high on the list of important considerations for landfill managers. After all, it’s all about airspace. But when it comes to airspace, there is a hidden cost that we often don’t think about. It’s the cost associated with excavating, hauling and placing cover soil. The hidden part of that cost is related to the airspace that is consumed by cover soil.
I’ve been performing operational audits at landfills for more than 40 years. Without doubt, the single biggest avoidable cost in the landfill industry is the excessive use of cover soil. I saw it 40 years ago, and I still see it today.
So, when we talk about compaction and airspace, the conversation isn’t over until we’ve addressed the issue of cover soil.
We’ll dive into that topic in the next article, Part 3, but the compactor operator can help reduce cover soil consumption by prepping the waste before cover soil is applied.
Whether it’s soil or some form of Alternative Daily Cover (ADC), cover is most efficiently placed when the waste surface is properly finished.
This starts with placing homogeneous, nonbulky trash on the surface. Sometimes this requires the dozer to warehouse a few loads until the end of the day, to make sure the compactor has good material to work with.
Then it comes down to the compactor operator doing a good job of trimming and filling, to create a smooth, uniform and plane surface.
The process of compacting trash at a landfill truly is a science. Yes, there is a component that is art, but only where it lines up with the basic laws of physics.
We’ll continue our series on landfill airspace in the next three articles as we address:
Part 3 - Optimizing Cover Soil Usage
Using Cover Soil Wisely – Compliance without Overdoing it
Part 4 - Alternative Daily Cover
ADC Secrets from the Best Managers in the Business
Part 5 - Tracking Your Landfill’s AUF
Bringing It All Together to Save Airspace and Money
Neal Bolton is president of Blue Ridge Services Montana Inc. He has been improving solid waste operations for more than 47 years. You can contact Neal at neal@blueridgeservices.com.
More from our latest newsletter
- Report: Common-sense standards could cut California landfill methane emissions
- Sunshine Canyon Landfill issued order to reduce odors
- Keystone Sanitary Landfill granted temporary operating permit extension
- Project Canary, Sniffer Robotics partner to develop methane emissions monitoring tools