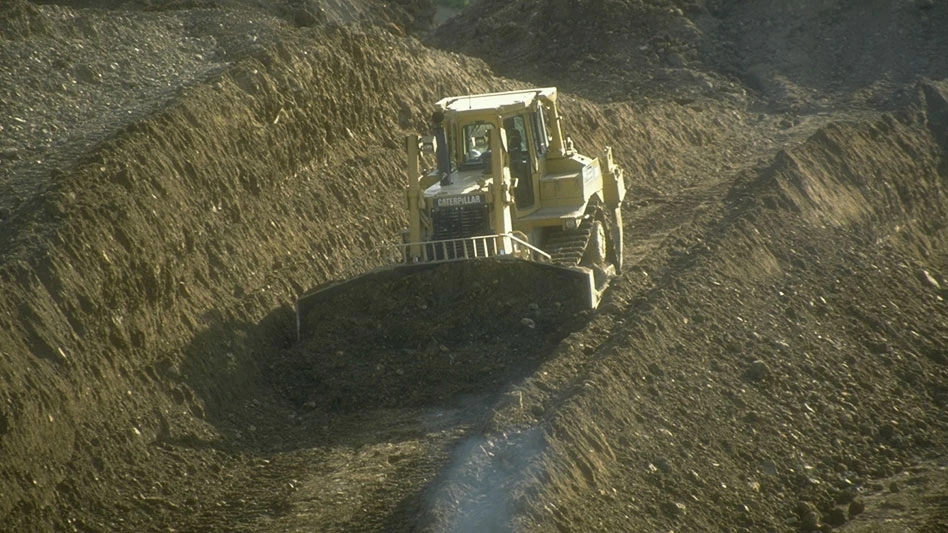
Photo by Neal Bolton
In some recent articles, we’ve discussed the fact that machines—trucks and tractors—will age and wear out based not on years but on hours of use. Thus, it follows that we could extend the useful life of those machines by reducing the hours they work.
This concept appears simple, except when viewed through the lens of tradition. How could we reduce the hours of use and still complete the work for which we purchased those machines in the first place? Most managers have established a normal way of doing things and they accept the idea that their machines will wear out along the same timeline that previous ones did.
Let’s step back, though, far enough to get some perspective. I’m writing this article while flying back home from a project. Not counting time at the airport, I’ll make the 1,500-mile trip in less than 4 hours. That’s my current “normal.” But in years past, I’ve also driven this same route, and those 4 hours of flying translate into a solid 3-day road trip—a different “normal.” Same goal of getting from here to there, but two very different ways of doing it. Further, we could say that one method is much more efficient than the other.
In other words, “There is more than one way to skin a cat.”
No, I’m not referring to Tabbies, Calicos or any other type of feline. In my world, “Cats” refers to bulldozers, a shortened version of “Caterpillar.” And folks who operate those machines are “catskinners.”
Let’s examine two contrasting ways a catskinner might work.
Imagine a bulldozer working at a quarry, where every day, every push is set up to be a full production push. Utilizing downhill and slot-dozing techniques, it’s relatively easy to get into a pattern of high productivity. There are no traffic jams, no waiting, no gathering a bit of soil here, a bit there. The dozer is moving material along a well-defined pattern, push, after push, after push. It is pure production.
Compare that to a bulldozer at a landfill, where every push could be different. There are production pushes and cleanup pushes. There is waiting, gathering, staging, grading and back-blading. In these somewhat random conditions, it’s easy to forget about making every push a production push. Instead, the goal can become one of keeping busy or, even worse, just looking busy.
This doesn’t only happen at landfills, but throughout the waste industry.
We could easily apply that same concept to how a transfer station processes trash. The goal for most transfer stations—simply stated—is to move trash from where it’s dumped on the tipping floor into a transfer truck. It is to move that trash from here to there. That task may be done with an excavator, grapple or, most commonly, with a wheel loader.
If we look at that process from the standpoint of pure production, using a wheel loader to top-load 20 tons of trash into a transfer trailer would take about 12 minutes. I’m also assuming that within those 12 minutes, the loader is gathering additional waste while the loaded truck exits, and an empty one takes its place. Overall, top-loading a truck is a 12-minute cycle, as shown by this graphic.
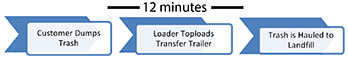
© Neal Bolton
But at many transfer stations, the loader must wait for the next empty truck because the driver is on break, stuck in traffic or chatting with the scale attendant. So, the operator ends up pushing trash into a temporary stockpile.
That temporary stockpile grows throughout the day, until it’s in the way, slowing production and ultimately forcing the wheel loader to change from pure production to juggling. That is: juggling waste from one end of the stockpile to the middle, from the middle to the other end …and finally into a transfer trailer. In the process, that ideal 12-minute per load cycle time takes half an hour (See Chart Below).

But it doesn’t stop there. This scenario goes on to require additional equipment, weekend work for the transfer trucks and lots of overtime for the drivers and operators. It is a snowball effect: The worse it gets…the worse it gets, until normal operations feel out of control.
The same evolution can occur with inefficient collections, at landfills where pushing, compacting and covering operations are inefficient, or at MRFs that are not focused on diverting the right commodities. In this industry there are many examples of operations forgetting what productivity looks like. Their operations may feel normal, but they aren’t good—and they aren’t efficient.
So, how can we stop the madness and establish a new, more efficient “normal” for our operations? We do it by fixing the operational chain, one link at a time. We’ll run through an example so you can see it in action. Let’s go back to the wheel loader at the transfer station. First, here are the factors that define this transfer station.
- The facility is open Monday-Friday, but the entire crew works Saturday to catch up
- Inbound trash: 480 tons per day
- Transfer truck payload: 20 tons
- Ideal cycle time for loading trucks (pure production): 12 minutes
- Average cycle time for loading trucks: 30 minutes
- Loader’s current workload: 10 hours per day (60 hours per week Monday-Saturday)
- Exported waste: 20 loads (400 tons) per day Monday-Friday, plus 400 (stockpiled) tons on Saturday
- Stockpiled waste at end of day on Friday: 400 tons
- Full staff of drivers and operators are required on Saturday to clear the floor
Now let’s conduct what is often referred to as a Comprehensive Operational Review, or CORE. Every CORE begins by defining the individual steps that are part of the process we’re evaluating—in this case, top-loading a transfer trailer.
On Monday morning, the first couple loads go off without a hitch. There are transfer trucks in position to be loaded, the floor is clean, route trucks are rolling in and the wheel loader gets the first 2 loads out in 24 minutes…that’s 12 minutes per load. This is what we saw in the first flow chart.
Then it happens. The third transfer truck is delayed getting to the loadout area, so the loader has no choice but to start stockpiling incoming waste on the floor. Later, an empty transfer truck arrives but it’s too late. The wheel loader begins loading—slowly because the stockpile is now in the way. But this entire process takes 30 minutes.
What’s more, instead of clearing the tipping area by taking every push to the transfer trailer, the wheel loader must stop loading, move to the other side of the stockpile and push more waste into the stockpile…to make room for the next route truck. The juggling process has begun.
More transfer truck delays lead to more juggling, and soon the stockpile has grown into a major obstacle—in the middle of the floor. The wheel loader’s cycle times become slower and more erratic. Those ideal 12-minute loadout cycles have been replaced with a stressful “normal” that averages 30-minutes per load.
At this point, we’ve lost control of the operation. To recover, we must figure out the root cause of the problem. Why wasn’t the next transfer truck/trailer in place for loading? Do we have enough trailers? Enough drivers? Appropriate scheduling? Identifying and then solving that problem will take some analysis. It may require a pit boss to ensure the next truck is in place as needed so the loader doesn’t have to wait…ever.
One of the challenges we face in making these types of improvements is complacency. If the staff has normalized those delays and become used to struggling during the week and then catching up on Saturday, they may not feel the urgency to change. They may also have become accustomed to an extra day of overtime each week. As managers, we must find a way to reset our “normal.”
We may find other factors contributing to the loss of efficiency because it’s seldom just one thing. The loader operator may be taking a morning break during a busy time. There may be no backup operator to keep things moving. Delays with transfer trucks/trailers may be due to maintenance issues, staffing issues, fueling delays, traffic delays or hold-ups at the landfill.
Sometimes fixing those underlying problems can take time. But look at what’s on the table if we do it.
- The loader could go from working 60 hours per week to 24 hours per week
- The loader’s functional life could be extended by a factor of 250 percent
- The daily cost of the wheel loader could be reduced by 60 percent
- Saturday work could be eliminated
- Overtime for all workers could be reduced
- The risk of fire from stockpiled waste could be eliminated
- Tipping floor crowding would be reduced, thereby improving safety for workers and customers
Yes, I know that the loader must adjust to inbound tonnage. Some hours are busy, others are slow. But in this simple example, the key is to have an empty trailer pulling into position immediately after a loaded trailer pulls out. There must always be a transfer truck in place, so that when waste is on the floor, the wheel loader has a trailer to load. That way, the loader can be parked during slow times, and only work when conditions allow it to make those productive 12-minute loads.
Please note that all operations have their unique characteristics and the numbers I used here, while typical, do not reflect conditions at every transfer station. Every facility has unique conditions requiring unique analysis.
Redefining “normal” starts by identifying the ideal production rate for a specific worker, machine or process. It’s followed by eliminating those roadblocks to achieve that peak production. Finally, it requires diligence to hold the operation to those new standards until it becomes “normal.”
As previously noted, it’s good to know how to calculate machine costs. It’s better to understand the key drivers to those costs, like machine work hours and machine life. But ultimately, the goal is to make operational changes that will maximize machine efficiency and minimize those costs. And when we can also improve safety, it becomes a win-win…win. That’s the core of process improvement. That’s the goal of every manager.
Neal Bolton is President of Blue Ridge Services Montana, Inc. He has been improving solid waste operations for more than 46 years. You can contact Neal at neal@blueridgeservices.com
Latest from Waste Today
- Startup proposes medical waste facility in Alabama
- Mount Vernon, Ohio, city council tightens waste hauling regulations
- Retail associations sign MOU to form producer responsibility organization for textiles in California
- Republic Services partners with EDL to provide RNG for San Antonio buses
- WM opens 12 recycling facilities in 2024
- Plastics recyclers report difficult conditions
- BTS Bioenergy opens Maryland Organics Recovery Center
- Meadow tabs aluminum as key to boosting beauty sector recycling