
Photo by Neal Bolton
The EPA’s Subtitle D rule, and your state’s regulations require landfill operators to cover waste every day. Here’s the federal version of the daily cover rule.
§258.21 Cover material requirements.
- Except as provided in paragraph (b) of this section, the owners or operators of all MSWLF units must cover disposed solid waste with six inches of earthen material at the end of each operating day, or at more frequent intervals if necessary, to control disease vectors, fires, odors, blowing litter, and scavenging….
These rules go on to explain options for alternative cover material and waivers that may be granted during extreme weather conditions. However, at a minimum, these rules require that the trash be covered every day with at least 6 inches of soil.
A close examination of these rules shows that they establish both a prescriptive standard and a performance standard.
Like a doctor’s prescription, the rules first state what you must do. That is: cover the trash with at least 6 inches of soil. Then the rules go on to explain why you must cover every day to control disease vectors, fires, odors, blowing litter and scavenging.
You must follow the prescribed rules to achieve a specific performance.
Based on those rules, most of the managers and equipment operators are prepared to testify that they are placing 6 inches of soil, even though most of them have never measured the depth, tracked inbound loads, or calculated volume of soil placed.
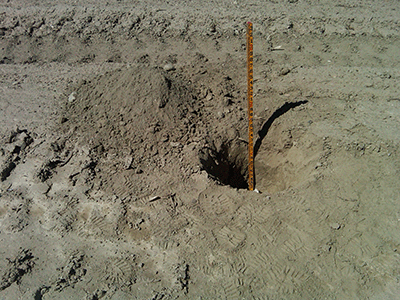
Measuring depth of daily cover soil at about 1.5 feet.
On the other hand, I’ve often dug holes when training landfill operators, but not to confirm 6 inches of cover soil. Rather we’ve dug the holes to show the reality of how much airspace is wasted through the overuse of cover soil.
Calculating how much soil your team is placing for daily cover is a quick and straight-forward process.
Over the years, I’ve provided training for hundreds of landfill regulators, usually for state agencies that want their team to better understand landfill operations. These are folks whose job is to regulate and inspect landfills. Interestingly, when we get to the topic of cover soil, I always ask how they confirm a landfill’s compliance with the 6-inch daily cover rules. In almost every instance, they utilize what I refer to as the skunk test. If it looks like a skunk and it smells like a skunk, it’s a skunk.
For the inspectors, if it looks like it’s covered, and if it meets the criteria for preventing litter, odors, vectors, etc., then it’s covered. In all that time, I’ve only met a handful of inspectors who had ever physically dug a hole to measure the depth of cover soil. Like I said, it’s the skunk test.
On the other hand, I’ve often dug holes when training landfill operators, but not to confirm 6 inches of cover soil. Rather we’ve dug the holes to show the reality of how much airspace is wasted through the overuse of cover soil.
Calculating how much soil your team is placing for daily cover is a quick and straight-forward process.
While there is some nuance to the analysis the equation is simple as recording the number of loads brought in by your truck or scraper, multiplying it by the rated payload (in cubic yards), and then dividing by 27 to convert from cubic yards to cubic feet. For example,
32 loads x 18 cy/per load x 27 cf/per cy = 15,552 cf
Where;
cy = cubic yards
cf = cubic feet
Then, divide the cubic feet of soil, by the surface area of trash it covered. Like this:
15,552 cf/110 ft wide x 120 ft long = 1.178 ft
Finally, multiply that depth by 12 to get the answer in inches.
1.178 ft x 12 in/per ft = 14 in
You can find the rated payload of the hauling unit online or by looking in the Operation and Maintenance Manual. A handheld laser range finder provides a quick way of estimating the dimensions of the waste being covered.
Most managers and operators are surprised when they run these numbers, finding that the concept of covering trash with 6 inches is a regulatory standard, but an operational impossibility.
After working at more than 500 landfills, I have yet to find a single one that can cover trash (to the point where it looks covered) with only 6 inches of soil. The average, at the many landfills where I’ve measured daily cover soil, is 16 inches. That’s right, based on hundreds of operational evaluations, the average landfill uses approximately 16 inches of soil to cover trash, while thinking that it’s only 6 inches.
The best operation I’ve seen averaged just 11 inches of cover soil. The worst was an amazing 42 inches! By the way, the latter was a contract operator. Their site looked great with no exposed litter, but they went broke within a couple years – and wasted lots of airspace in the process.
Why the discrepancy between the rules and reality? Because our industry has spent so much time talking about 6 inches of daily cover soil as the target – and so little time actually calculating soil depth – we’ve simply assumed it’s really happening. But don’t take my word for it. Do your own test.
Count loads, convert to cubic yards, then to cubic feet. Divide that answer by the length and width of the area you’re covering …and viola! You’ll know the average depth of cover soil used at your landfill. You may be surprised to learn just how much soil you’re placing for daily cover. And you’ll likely be shocked when you convert that quantity of soil into the volume of airspace that daily cover soil is consuming every day at your landfill.
Going back to the equation, 32 loads x 18 cubic yards per load is 576 cubic yards of soil that you brought in as cover soil. You pay for the labor, equipment, and fuel to excavate, haul, and place that soil. But that’s chump change compared to the value of airspace it consumed. Using a conservative estimate of $15 per cubic yard for the value of airspace, the soil in our example just burned $8,640 in landfill airspace!
For many managers, that is a hidden cost - something they don’t think about. They won’t think about it until it’s time to construct the next lined module, but by then it’s too late.
Yes, daily cover soil represents, far and away, the single biggest waste of airspace at most landfills. Said another way; landfills that use cover soil as their primary means of covering trash may be looking good. They may be feeling good. But they probably have no idea what’s going on in terms of wasting airspace.
This is why so many landfills now use one or more forms of alternative daily cover (ADC) to cover trash in lieu of using soil every day. That’s something we’ll discuss in the next article, but for now, we’ll examine ways to minimize soil usage on those days when you must use soil.
Nearly every landfill, even those that are dedicated to ADC, must periodically use soil when working on an outside slope, when moving from one area to another, or simply as a periodic fire break. Most states require landfill operators to cover everything with soil at some regular frequency.
So, when you must use soil, what can be done to minimize the amount used?
Well, that’s a simple question that comes with a somewhat more complicated answer.
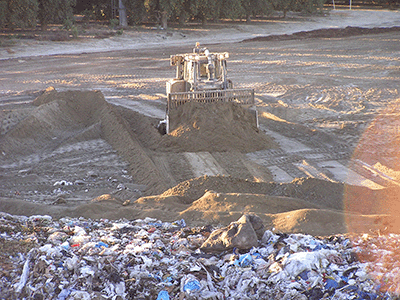
Dozer placing daily cover soil on rough trash surface.
Consider first the condition of the waste surface on which you’ll be placing soil. A smooth, uniform, and well-graded surface will naturally require less soil than a rough, uneven, and poorly graded surface.
Trash that’s delivered in packer trucks, like side-loaders, rear-loaders, or front-loaders is more homogeneous than rough trash like C&D. Consequently, it will produce a smoother surface.
Some landfill operators will track-walk the trash surface before placing cover soil to help “knit” the surface together, reduce voids, and provide a nice uniform surface to cover.
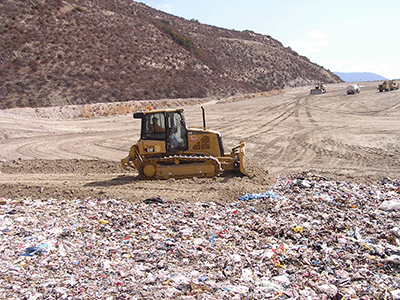
Dozer placing daily cover soil on smooth trash surface.
These two photos show contrast between placing cover soil on a rough surface, vs a very smooth surface.
This comes down to the type of trash you’re using to finish the active cell, and how you’re placing it.
When it comes to placing daily cover soil, your operational choices matter.
If you’re primarily using soil as daily cover, it’s important that you understand precisely how much soil you are placing. Effective managers know that stating the problem is the step toward solving it.
But once you determine how much soil you’re using for daily cover, you’ll want to do something about it. Along that line, here are some tips for reducing the amount of soil used for cover.
Tip #1 – Use homogeneous trash, like what comes in packer trucks, to finish off the waste cell. This material allows you to create a smooth, uniform surface with fewer voids that rough, C&D-type trash.
Tip #2 – Roll the surface with the compactor to create a stable, solid surface. Cross rolling at 90 degrees is an effective way to firm up the surface.
Tip #3 – Use a small dozer to track-walk the surface of the waste prior to placing cover soil. In most cases, this produces the smoothest waste surface with the fewest voids.
Tip #4 – Establish a budget for daily cover soil. Do this by working through the equation backward. Start by measuring the trash area to be covered (length x width). Then calculate how much soil would be required based on a given depth. I like to set a challenging goal of maybe 10 inches of soil. Your landfill will almost certainly require more than that, but most landfill workers will do surprisingly well when a goal is clearly stated. You’ll find it helps workers visualize the goal if it is expressed in loads of soil.
Here’s an example of how to establish a cover soil budget.
Measure the area to be covered. Again, a laser rangefinder makes this easy.
115 ft wide x 120 ft long = 13,200 sf
Then convert to cubic feet based on the target depth of cover soil, which in this example is 10 inches.
13,200 sf x 10 in x 1 ft/12 in = 11,000 cf
Then convert that volume of soil from cubic feet to cubic yards, using the factor that 1 cubic yard equals 27 cubic feet.
11,000 cf x 1 cy/27 cf = 407 cy
Finally, divide the volume of soil required for cover by the payload of your truck or scraper. In this case we’ve assumed an 18cy payload.
407 cy x 1 load/18 cy = 23 loads
Based on this process, covering a 110ft by 120ft area with 10 inches of soil will require 23 loads of soil.
If you’re into excel, you can create a simple budget model that will streamline this calculation. Even better, send me an email and I’ll send you a link to download the model I use. Mine is set up as a basic lookup table.
In the next article, we’ll discuss alternative daily cover (ADC).
Part 4 - Alternative Daily Cover
ADC Secrets from the Best Managers in the Business
Part 5 - Tracking Your Landfill’s AUF
Bringing It All Together to Save Airspace and Money
Neal Bolton is President of Blue Ridge Services Montana, Inc. He has been improving solid waste operations for more than 47 years. You can contact Neal at neal@blueridgeservices.com
Latest from Waste Today
- Meadow tabs aluminum as key to boosting beauty sector recycling
- LFG-to-energy: Maximizing returns with multitiered methane monitoring
- FCC completes acquisition of Florida WTE facility
- Casella to acquire Mountain State Waste
- Landfill Insights | Airspace Part 5: Tracking your landfill AUF
- Missouri city expands recycling capabilities with funding from The Recycling Partnership
- Recycle BC portrays its end markets
- Crystal Clean launches compact PFAS remediation solution