
Photo courtesy of Neal Bolton
Machines don’t wear out all at once, they fail one component at a time. An engine here, a transmission there, with a final drive or differential tossed in for good measure.
Sure, a machine fire or catastrophic roll-over can be the
death of a machine, but typically they reach the end of their life in a
progressive and somewhat predictable path.
Knowing this, the best managers are strategic when it comes
to tracking machine components. They know things will fail, but they choose to
track and manage that process.
This begins with establishing expected component life based
on the history of similar machines and your experience. For example, you
might estimate that a bulldozer engine will go 10,000 hours before it needs to
be replaced or rebuilt.
Further, you can adjust your expectations by closely
monitoring its condition. Is it making noise, consuming more oil or emitting more
exhaust smoke? Is your oil-sampling program showing specific “wear
indicators?” That typical 10,000-hour estimate is never exact, so adjusting
your expectations is very important, especially as the machine ages.
Based on annual usage (i.e. hours per year), you could
calendarize those expected component failure points to create a specific cash
flow projection for every machine.
Think about it: What if you could project the life of
individual components, do that for every machine, and then combine that
information into a machine component rebuild schedule? You’d have a very
accurate, adjustable and real-time budgeting tool for major machine repair
costs.
This would be much better than the current process used by
most managers that bases next year’s machine repair budget on how much was
spent the previous year. That’s a process that makes managers look like a hero
for one year, and an idiot the next. No thank you.
So when it comes to managing your machines, managers should
think in terms of components. They should, but not all of them do.
Even worse, some organizations have a policy that assumes if
a major component fails, like an engine or transmission, it’s time to buy a new
machine. The local equipment dealers may favor this approach, but the
organization will leave lots of money on the table. It is standard industry
practice to repair components as they fail, while managing overall machine
performance and cost to manage the “four R’s.” That is, should I run it, repair
it, rebuild it or replace it? Every manager makes those decisions every day.
They just use varying levels of knowledge when doing so.
We’ll look at a way of managing the “four R’s” that
integrates knowledge and wisdom into the process.
Tracking component life for an individual machine, like a bulldozer, begins by listing those components. They include engine, transmission, final drives, undercarriage, pins and bushings and any other rebuildable components. This list will vary from one machine type to another but, in every case, you’ll be focusing on the major components that make up that machine.
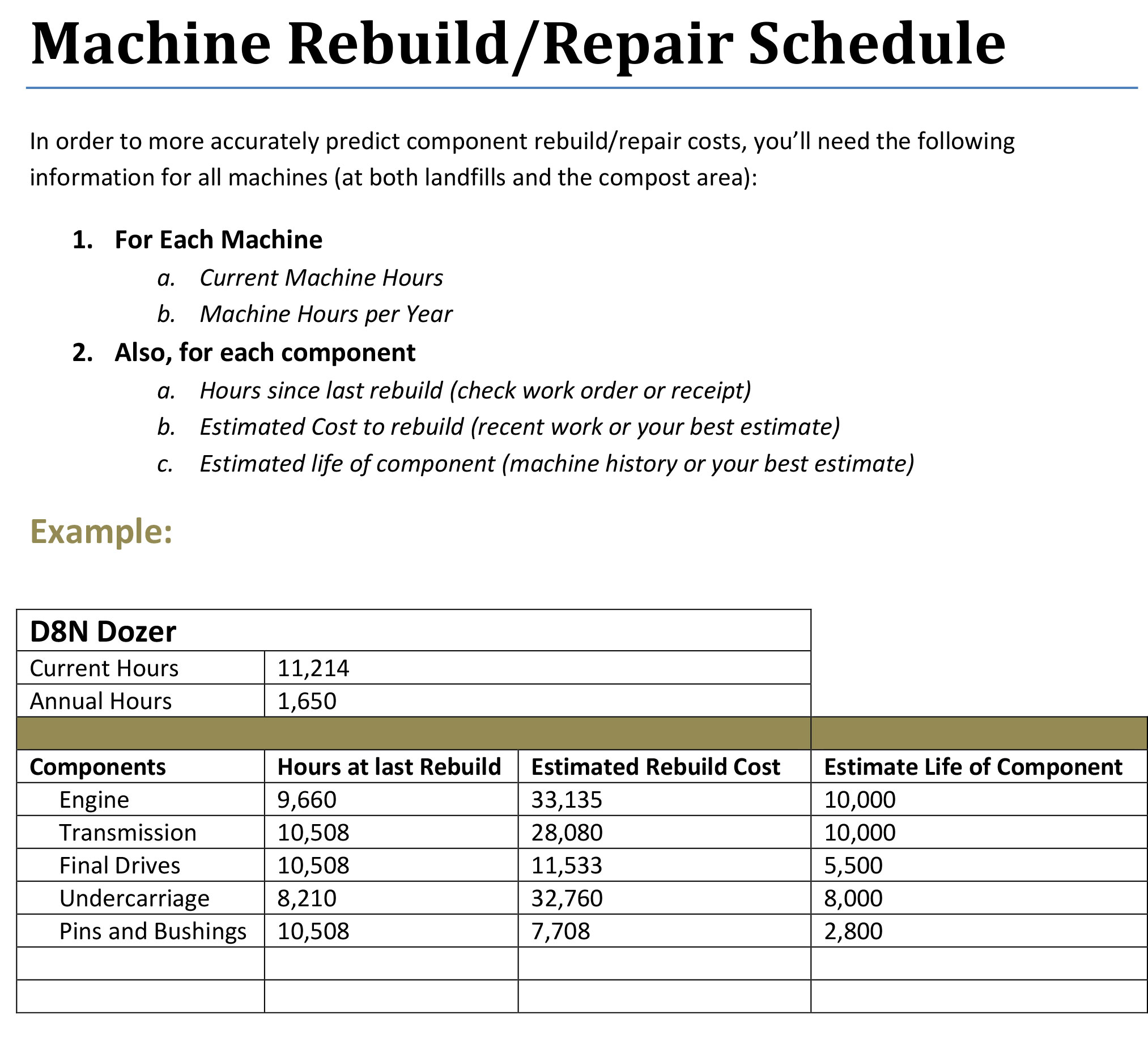
Next, assign an estimated life of each component. In this
part of the process, it’s good to use historic data and your experience. Be
sure to talk with your mechanic and the field service rep from your local
dealer. There is wisdom in many counselors and your goal is to accurately
estimate the life of every component.
Inventory is the next step. This is where you create a
status report for every component for every machine. Determine when the most
recent rebuild or replacement of every component was done. For example, you
might estimate that a bulldozer engine will last 10,000 hours. But if the
engine on your bulldozer was replaced at 9,660 hours, then that engine would be
expected to fail approximately 10,000 hours later, somewhere around the
19,660-hour mark.
Under this system, the clock for individual components starts over when a component is rebuilt. In some cases, it may make sense to downgrade the life estimate for rebuilt components. Due to various factors, a rebuild component may not last as long as the original component that was part of a new machine. Again, these factors should be based on machine history and your experience.
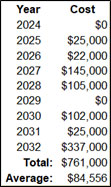
For many years, I’ve used a simple Excel spreadsheet model
that estimates the recurring failure point for every component on a given
machine—for instance, a bulldozer.
It then rolls that information into an annual estimate of
that machine’s annual repair costs. Here’s a look at that annual cost estimate
(table and chart). This estimate includes major components: engine,
transmission, final drives, undercarriage and a subcomponent of undercarriage—pins
and bushings.
The average annual component cost for this machine is
$84,500 per year but, as you can see, there is wide variation. Some years we
skate through without anticipating any component issue, and other years show
multiple rebuilds or replacements. It looks random, but in fact it is based on
annual hours and estimated component life.
Based on previous articles, you know that when it comes to
overall machine life, there is a point at which it’s best to replace an aging
machine. The trick, of course, is to replace it before it becomes a financial
sink hole.
Along that line, consider what our bulldozer model shows for
the year 2032. Based on our assumptions of annual hours and component life and
replacement cost, 2032 is a very expensive year. Consequently, selling that
machine in 2031 makes sense.
Of course, as you get closer to that time, you may adjust
your decision based on actual conditions. That’s why you should periodically
adjust this model as you rebuild certain components, monitor oil sampling
results, track annual machine hours and observe other vital signs of that
machine.
Finally, you can bring all this together by combining
similar information for all machines in your fleet. At that point, you’ll have
a robust cost model that can predict major repair costs for all machines. By
getting a solid handle on machine component costs, you’ll be a hero every year
because instead of guessing, you’ll be managing those costs.
Neal Bolton has nearly 47 years of experience in the heavy construction and solid waste industry. He can be reached at neal@blueridgeservices.com.
Latest from Waste Today
- US Senate backs reduced cuts to EPA
- ELV Select Equipment, Reworld aid NYPD in secure firearm disposal
- Waste Connections announces Q2 results
- Returnity and Cosmoprof to address reusable bag waste
- SWANA releases report on aging WTE facilities
- New economic assessment reveals cost benefits of California’s SB 54
- Premier Truck Sales & Rental opens new facility
- TeknTrash Robotics, Sharp Group partner on humanoid robot pilot