
Photo by Neal Bolton
The most effective folks in the business manage landfill airspace as though it was their most valuable asset. Actually, it is.
An increasing number of landfill managers share this opinion and, coincidentally, so does the U.S. Securities and Exchange Commission (SEC). According to the SEC, landfill airspace is considered an asset. More specifically, airspace can be reported on a company’s balance sheet as a depleting asset.
The rate of depletion shows up on your annual airspace report. If yours is like many other landfills, an engineer compared your before and after topographic maps and calculated how much airspace you consumed last year. That is good information but it is, at best, historical knowledge. If you want to make a difference moving forward, you’ll need more detailed information. Nobody drives down the road while only looking out the rear window.
Airspace is depleted as it is consumed, but if you want to manage airspace, you’ll need to think in a bit more detail. How, for example, is the airspace being depleted? Here are some ways.
Do the math
The inbound waste stream consumes airspace. When a customer brings in a load of trash, you effectively take some airspace off the shelf and sell it to them. It’s just like a box store, only your boxes are measured in 3-foot x 3-foot x 3-foot cubes, called cubic yards. Typically, the rate of airspace consumption is measured in pounds (or tons) per cubic yard (PCY), something referred to as an airspace utilization factor, or AUF. A typical landfill might achieve an AUF of 1,400 PCY (or 0.7 tons per cubic yard).
Many managers look at their AUF simply as a mathematical calculation—which it is. Your AUF can be calculated by dividing the mass (M) of waste placed by the volume (V) consumed. Like 2 + 2 = 4, your AUF is always M ÷ V = AUF.
But the way inbound trash is converted to landfill airspace is dependent on several factors. Those factors can be controlled, for better or for worse, by your operating techniques, and therein lies the opportunity to improve your operation.
Over the years, I’ve worked at more than 500 landfills, and I’ve seen the AUF range from 800 PCY to well over 2,000 PCY. Some of that variation is a result of different waste streams but most of it comes down to the choices that individual operators make regarding the simple processes of pushing, compacting and covering.
Making the right choices can be learned through simple training and by giving operators the tools they need to perform at their optimum level. Today we’ll present an overview of these AUF variables. Consider this a preview, because over the next few articles, we’ll be presenting a Master’s look into the grammatically incorrect terms most landfill folks refer to as push, pack and cover.
Push
Maximizing your landfill’s AUF starts at the tipping pad, where spotters and dozer operators identify different types of trash and push it to the correct location on the active face.
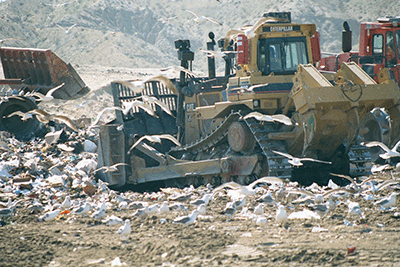
Bulky items go into a hole, along an outside edge or pushed up against the toe, where they can be tucked in and covered with loose trash. Construction and demolition (C&D) debris and other rough trash that has many voids may be blended with fine materials. Loads that contain lots of paper, cardboard or other cellulose fibers are mixed with wet packer truck loads—or even with sludge. The finer, packer truck material is used to finish off the cell, producing a smooth, uniform surface that is easy to cover with soil or alternative daily cover (ADC).
Like a puzzle, different types of waste are assembled on the active face. This is science and art. When done correctly, this sets the stage for the compactor to do its thing—pack.
Pack
Waste compaction is how landfills keep score. Other things, such as regulatory compliance, fiscal responsibility and environmental protection are all very important, but when landfill managers get together and compare notes, it always comes down to the compaction rate. Yep, in other settings we might look at: How smart are your kids? How fast is your car? ... Or, How much can you bench press? But for us landfill folks? It’s always, “What is your AUF?”
In that regard, the make, model and size of your compactor(s) is important. So, too, are the specifics of wheels and teeth. But the biggest factor is the compaction techniques of your operators.
There is a reason landfills spend a million dollars a pop for a landfill compactor. Obviously, it is to enable the operator to achieve the highest possible density and conserve your biggest asset: airspace. For now, consider this question.
If you spent a million bucks on an accounting software program with the intent of managing several million dollars per year, would you want your accountant to be highly trained, certified and experienced, or would you just toss the keys to somebody who had worked as a cashier at the scale house? We know the answer.
So, how much training have you provided to the person who operates your $1 million landfill compactor while managing airspace that’s worth many million dollars per year? Are they highly trained, certified and experienced … or did you just toss them the keys?
In a future article, we’ll lift the lid and look inside the complex process of waste compaction.
Cover
Today, most landfills use one or more forms of alternative daily cover—ADC. But most also use a significant quantity of cover soil.
In our experience, excessive use of cover soil is the single biggest factor that wastes landfill airspace, and it is the biggest hidden cost.
I’ve asked hundreds of landfill operators—and hundreds of landfill managers—“How much cover soil are you placing on that trash?” Almost without exception, their response is, “6 inches.” But when I ask if they’ve ever measured it? Or have they ever calculated the volume of soil used versus the surface area to be covered? The answer is, “no.”
Sponsored Content
MORE THAN A TRUCK.
Hino trucks power through the toughest challenges with proven durability, performance, and exceptional comfort. With Hino Edge connectivity, an exclusive standard 5-year Allison Transmission warranty, and 24/7 HinoWatch roadside assistance, our support goes beyond the sale. With The Ultimate Ownership Experience, Hino always delivers MORE THAN A TRUCK.
Sponsored Content
MORE THAN A TRUCK.
Hino trucks power through the toughest challenges with proven durability, performance, and exceptional comfort. With Hino Edge connectivity, an exclusive standard 5-year Allison Transmission warranty, and 24/7 HinoWatch roadside assistance, our support goes beyond the sale. With The Ultimate Ownership Experience, Hino always delivers MORE THAN A TRUCK.
Sponsored Content
MORE THAN A TRUCK.
Hino trucks power through the toughest challenges with proven durability, performance, and exceptional comfort. With Hino Edge connectivity, an exclusive standard 5-year Allison Transmission warranty, and 24/7 HinoWatch roadside assistance, our support goes beyond the sale. With The Ultimate Ownership Experience, Hino always delivers MORE THAN A TRUCK.
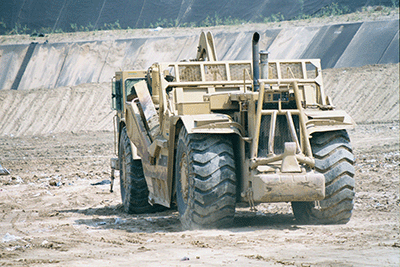
How, then, do so many people in our industry assume they are placing 6 inches of soil? Because that’s what the regulations require. Yep, federal and state regulations require that landfills cover all exposed waste at the end of every operating day, with at least 6 inches of soil. Have you ever been on a diet without counting calories? Or have you ever been on a budget without tracking expenses? If so, then you can probably relate to the futility of managing cover soil without monitoring its use.
Well, we have measured it—hundreds of times. And we’ve found that the average depth of soil used as daily cover is 16 inches … not 6. Cover soil consumes a lot more airspace than most managers and operators think.
Looking at it another way, we can use a conservative estimate that every cubic yard of soil brought into the landfill costs $15 per cubic yard, considering the value of airspace and the cost to excavate, transport and place it. Thus, it follows that every scraper or truck load of soil—even if it’s used for daily cover—costs $300 to $400.
Think of it; for every load of soil you bring into your landfill, you take $300 to $400 worth of airspace off the shelf! So, how many loads of soil do you haul into the landfill every day?
These are big questions. And the answers represent big costs.
If this discussion has you wondering how you can better manage airspace at your landfill by improving your AUF, stay tuned. We’ll be covering these vital topics over the next several months.
Over the next 5 issues we’ll be drilling into the following topics:
From the tipping pad to the active face:Techniques for efficient and effective pushing
The science of landfill compaction
Maximizing productivity of your landfill compactor
Optimizing cover soil usage
Using cover soil wisely – compliance without overdoing it
Alternative daily cover
ADC secrets of the best managers in the business
Tracking your landfill’s AUF
Bringing it all together to save airspace and money
Neal Bolton is president of Blue Ridge Services Montana Inc. He has been improving solid waste operations for more than 47 years. You can contact him at neal@blueridgeservices.com
Get curated news on YOUR industry.
Enter your email to receive our newsletters.Latest from Waste Today
- US Senate backs reduced cuts to EPA
- Waste Connections announces Q2 results
- Returnity and Cosmoprof to address reusable bag waste
- SWANA releases report on aging WTE facilities
- New economic assessment reveals cost benefits of California’s SB 54
- Premier Truck Sales & Rental opens new facility
- TeknTrash Robotics, Sharp Group partner on humanoid robot pilot
- Stadler equips mixed waste sorting plant in Sweden