
Photo by Neal Bolton
A landfill’s airspace utilization rate is very dependent on its operational processes. In that regard, most folks automatically turn their thoughts to compaction. Certainly, compaction is important, but the process doesn’t start there. Indeed not.
Those landfills that achieve excellent waste compaction start that process far upstream. Long before they put the teeth to the trash, that trash has been categorized, segregated and strategically placed within the active working face.
One might argue that good compaction begins with development of community education programs to manage waste flow, and that it continues with well-structured waste disposal agreements with local towns and private haulers. There’s no question that good diversion programs contribute to the preservation of landfill airspace and those pre-planning efforts are important. However, in the context of this article, we’ll look at what happens at the landfill when a load of waste shows up at the scale.
Looking ahead
In the same way that a successful flight begins long before takeoff, the onsite process of managing your landfill’s airspace begins with planning and response, one load of trash at a time. Ideally, the scale attendant will be communicating with the spotter or equipment operators, letting them know when specific types of loads arrive. It’s a big help for the spotter, dozer operator and compactor operator to have pre-notice of any out-of-the-ordinary loads that are headed their way.
Sure, trash is trash. But that dead horse, the load of sludge or the dump truck filled with rough C&D will require some special handling, and the sooner the landfill operators know it’s coming, the better.
However, even with the best possible early warning system, when a load is dumped at the tipping pad, the dozer operator—or whatever other machine operator pushes that load to the active face—must make a quick decision. Hopefully it’s not a wide-eyed snap decision, because even without notification from the scale attendant, there are some preliminary indicators based on truck type. Still, we really don’t know what’s in that load—until it’s dumped.
And once it hits the ground, the operator must decide where to push that load.
- If it’s bulky, it may go into the toe of the slope or a corner, where it can be out of the way of normal cell construction activities.
- If it’s wet, you may push it across a dry portion of the cell where that moisture can be shared with dry fibrous material like paper or cardboard.
- If it contains lots of fines, say from a MRF or the bottom dregs off the transfer station floor, it should be mixed with material that has lots of voids. This creates a denser and more homogeneous mix.
- If it’s a nice, uniform packer-truck load, it may simply be integrated into the active face.
There are many other, “If this, then that” analyses, but these are some of the more common ones.
The point is, cooking up a good compaction rate starts with putting the right ingredients in the right spot—at the right time.
Yes, I understand that some landfills have the benefit of receiving a nice, dependable flow of homogeneous waste from one or more transfer stations. That may help dampen some of the wide variability that most landfills see. But there are still judgment calls. Don’t become stuck on the idea that a transfer station is a factory that ships out a super-consistent waste type. Sure, transfer stations may do some mixing and even some pre-compaction, but what they send is dependent on what they receive, something that can vary day by day and load by load. Transfer stations operate on a strict concept of garbage in, garbage out.
OK, we get it; the waste stream varies—that’s bad. But we can work with what we get to maximize our compaction results—that’s good.
The conversion from bad to good is what happens between the tipping pad and the active face, and success depends on how the spotter and dozer operators manage that inbound material.
Along that line, I’ll set forth some guidelines for getting trash from the tipping pad to the face. These are generalized based on what I’ll call a “typical” landfill, where a dozer pushes trash from the tipping pad to the active face. Of course, there are many ways to run a landfill, but after working at hundreds of sites, these guidelines can, with minor adjustments, be applied to most.
Allow room to stage
The landfill industry loves tradition. Back in the days when most landfills used soil as the only means of cover, it was beneficial to keep the active face as small as possible—to minimize the quantity of soil required for covering and reduce the corresponding consumption of airspace. But this isn’t your grandfather’s landfill. We’ve been using various types of ADC for many years, and the main reason for maintaining a postage stamp-sized face is no longer valid. Yet many landfills are still limiting their workspace for no apparent reason.
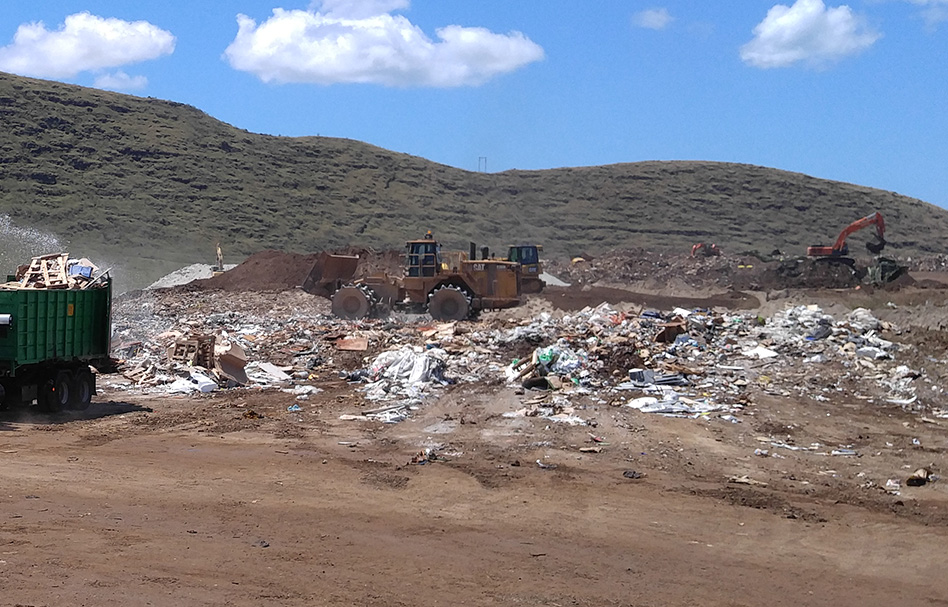
Today, the benefits of a larger face usually outweigh the drawbacks. This is something we’ll discuss in a future article. Suffice to say, you should consider widening that active face, which means you can also widen the tipping pad to provide more room for staging loads.
For reasons associated with efficiency and safety, I have become a strong advocate of using a typewriter system at the tipping pad. Working in a repetitive right-to-left or left-to-right pattern, trucks move progressively across the tipping pad, followed—at a safe distance—by the dozer. This naturally maintains a safe buffer between customers and heavy equipment, while giving customers a predictable dumping pattern—something they can quickly learn and adopt.
As with anything else, there are many nuances to making a typewriter system work effectively. And, in the context of this article, one of those is the ability to segregate and preblend loads of waste.
Place loads strategically
Using a spotter (i.e., traffic director), signs, markers, radios and/or other forms of communication, certain types of loads can be placed in the most strategic location on the tipping pad. With the goal of making every dozer push a full production push, every tipping slot should be filled with trash.
Along that same line, multiple small loads of waste may be double or triple-stacked in the same slot based on the type of material. A load of rough C&D may be combined with a load of MRF fines in the same tipping pad slot. Similarly, it makes sense to combine a load of sludge with a load of cardboard or paper. Or a load of lumber that will create lots of voids may be combined with another type of material that can be broken down into fine particles that will fill those voids.
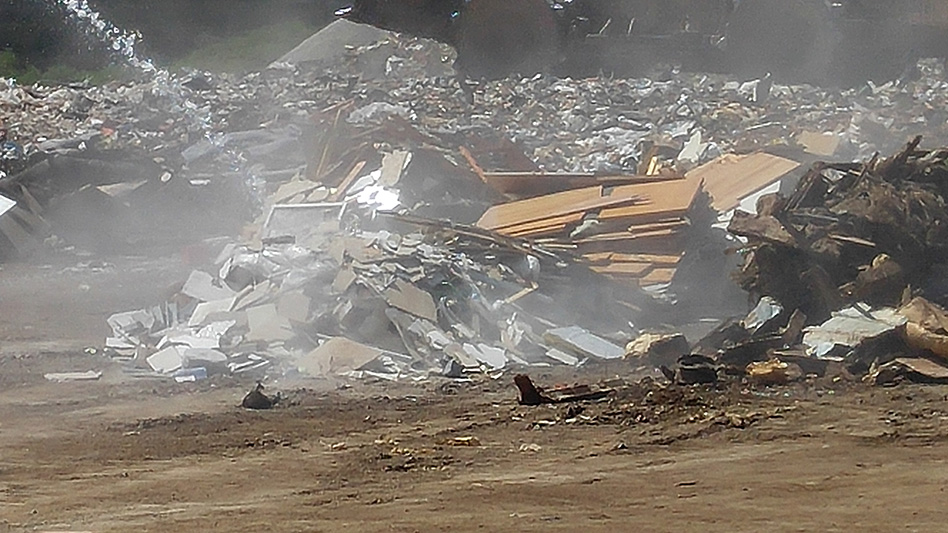
Also, a load of shingles or tile scraps that may be hard to push cleanly without dropping the blade and stripping lots of soil from the tipping pad might be more effectively cleaned if double-stacked with a sweeper load of brush or green waste.
The idea here is to pair different types of waste to create an ideal result. Fines can help fill the voids of a rough load and moisture can help soften fibers in paper and cardboard. In both cases, the dozer delivers to the active face a blended load of material that can be compacted efficiently and effectively.
Warehouse until you need it
When you establish enough working space at the tipping pad, you also allow flexibility for the dozer to be more strategic in terms of what is pushed to the face and when it’s pushed. This is a big shift in thinking. Operators who have become accustomed to working from a very constrained tipping pad have a mindset that every load creates an emergency. It must be pushed immediately because the next driver is in a hurry to get into that slot and dump. Yes, it feels like an emergency.
But with a widened tipping pad, while trucks may still need to wait for the appropriate slot to open, that pressure isn’t focused on the dozer operator making the next push.
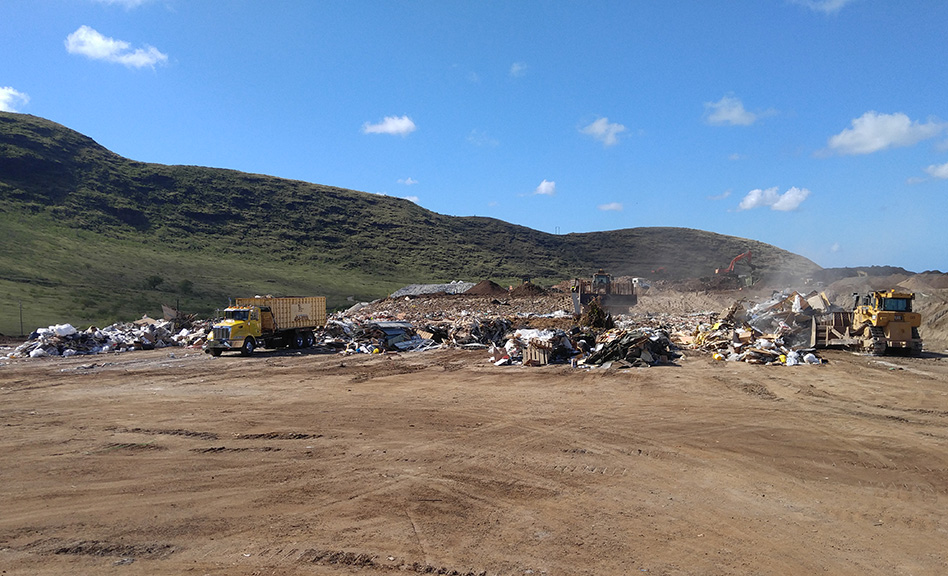
That means the dozer operator can be more strategic about when loads are pushed and how they are placed on the active face. For those who have operated heavy equipment, you’ll also realize that this will take pressure off the compactor operator, because rather than responding to the dozer making continual “emergency” pushes, those loads can now be delivered to the face when they’re needed and where they’re needed. This is the difference between emergency response and a strategic plan.
In an ideal scenario, the wide tipping pad is a staging area. We might even call it a warehouse. Individual loads of trash can be stored there until they are pushed to the face.
We can use that warehouse for blending different types of waste, and to create full production loads for the dozer. From a simple physics perspective, it takes less work to perform fewer full production pushes, rather than lots of non-productive pushes. You see this concept in play every time you board a plane where every seat is filled. Those airline execs know it’s better to make one full flight from Dallas to Portland rather than make two flights at 50 percent capacity.
This is pure physics.
Push full loads
Let’s step back and think big picture. The dozer pushes trash from the tipping pad to the active face. This is a repetitive task that may happen hundreds of times each day. Every push takes time and consumes fuel. Your dozer will eventually wear out while performing this repetitive process—one push at a time.
But how the dozer is operated plays a tremendous role in that process. If every load that’s dumped at the tipping pad represents an emergency, then the dozer will push that load, regardless of whether it’s a full production load … or just 3 bags of trash. Either way, it takes time, burns fuel and wears out the dozer.
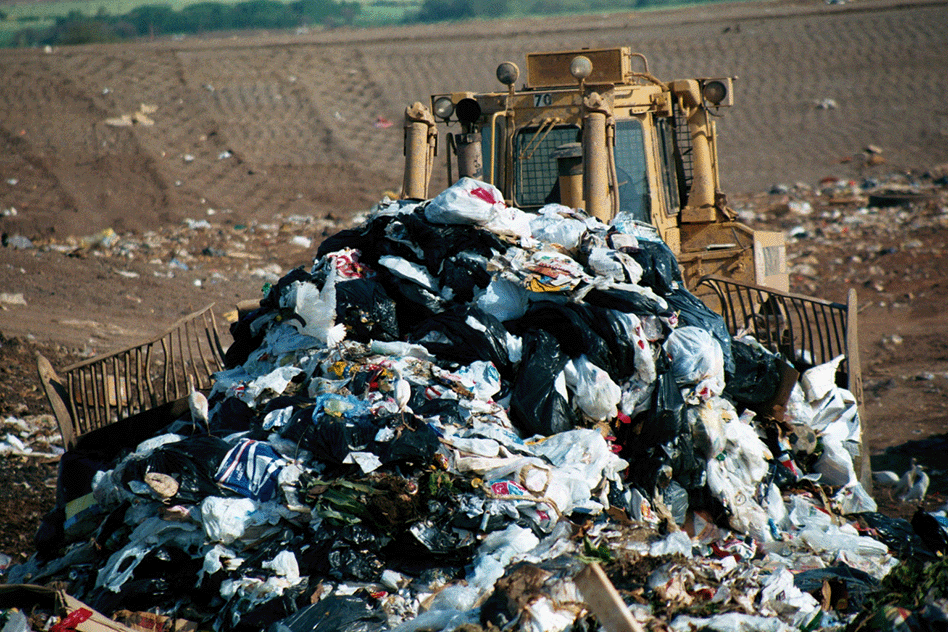
Here are some real numbers, statistics we’ve accumulated by filming thousands of dozer pushes.
- The average dozer push cycle from the tipping pad to the face and back takes approximately 1 minute.
- The average dozer makes multiple wimpy pushes to the face for every 1 (full blade) production push.
- The average dozer working at the tipping pad could reduce its hours, and corresponding costs, 50 percent to 70 percent by focusing strictly on making full production pushes.
Savvy dozer operators can make this shift by following the guidelines we’ve established here. But there is one more key step, and that’s related to cleanup.
At many landfills, the dozer operator will follow every push with two or more cleanup pushes. The idea here is that they are maintaining a clean—even polished—tipping pad. Sounds great, but unfortunately this is another of those old traditions that doesn’t make sense.
If we evaluated how much slot width a truck needs to back in and dump a load, we’d find that in most cases, the truck needs a clear slot that is 10-12 feet wide. Maybe a bit more depending on the dumping mechanism, how the tailgate swings, etc. The width needed for a truck to back in is created by the dozer making a single push. Landfill blade width can vary, but for a D6, D7 and D8, typical blade widths will average 13, 14 and 16 feet respectively. In most cases, a single dozer push creates a reasonable slot for the next truck. Sure, there are other factors, but generally a single dozer push is sufficient.
We can likely agree that every time a dozer pushes a load, a berm of trash is created on both sides of the push path. But we may not agree on the need to clean up that berm. Old-school thinking follows the line of creating a clean tipping pad, like a parking lot. My thinking is more along the line that those two berms will, after a few pushes right down the middle, create a slot for dozer. When it comes to dozer productivity, slot dozing will increase the efficiency of all subsequent pushes by up to 20 percent because it allows the blade to carry a larger load. Remember, dozer capacity usually isn’t limited by how many tons it can push, but by how much volume it can carry.
Again, this is all pure physics—with a direct impact on economics. Increased efficiency means reduced operating costs.
And once you’ve decided where a particular load needs to go, the next step is to get it there quickly, safely and efficiently.
Work with the compactor
All this analysis about pushing trash from the tipping pad to the active face is important. It can make the dozer operator’s job easier and save money. Wonderful.
But as we said at the beginning of this article, we are setting the stage to save airspace by maximizing the efficiency of the compactor.
Putting the right load in the right place at the right time is key when it comes to achieving good waste compaction. Some loads should be pushed intact and placed for the compactor operator to do the final spreading and mixing. In other cases, loads should be spread in thin layers to reduce the workload on the compactor. To decide what’s best for every load, the spotter, dozer operator and/or compactor operator must be working together. In all the steps leading up to effective waste compaction, there are no lone rangers and there are no superstars, there is a team.
Over the next four issues we’ll be drilling into these topics:
The Science of Landfill Compaction
Maximizing Productivity of your Landfill Compactor
Optimizing Cover Soil Usage
Using Cover Soil Wisely – Compliance without Overdoing it
Alternative Daily Cover
ADC Secrets of the Best Managers in the Business
Tracking Your Landfill’s AUF
Bringing It All Together to Save Airspace and Money
Neal Bolton is president of Blue Ridge Services Montana Inc. He has been improving solid waste operations for more than 47 years. You can contact Neal at neal@blueridgeservices.com.
Latest from Waste Today
- Waste Connections announces Q2 results
- Returnity and Cosmoprof to address reusable bag waste
- SWANA releases report on aging WTE facilities
- New economic assessment reveals cost benefits of California’s SB 54
- Premier Truck Sales & Rental opens new facility
- TeknTrash Robotics, Sharp Group partner on humanoid robot pilot
- Stadler equips mixed waste sorting plant in Sweden
- Mack electric collection truck delivered to New York