
In the effort to improve overall recycling or diversion percentages within jurisdictions or municipalities, the dense tonnages associated with construction and demolition (C&D) debris have always been a prime target for recovery.
The common C&D processing equipment of a screen or two and some manual sorters is now expanding to include more sophisticated air separation equipment and even infrared (IR) optical units to better separate materials for more recovery or potential new markets. While the technology is improving to process these C&D materials, most within the industry stress the importance of markets and outlets for the commodities that are targeted for recovery.
SOPHISTICATED RECOVERY
One of the most sophisticated C&D plants that has been constructed recently is the Zanker Recycling demolition processing facility in San Jose, California. The system shared the Solid Waste Association of North America’s (SWANA) Gold Award for recycling systems in 2016. The system is rated for 60 tons per hour (tph) but consistently operates at 75 tph. The facility serves an approximate population of 6 million people in an area with strict recovery regulations regarding all waste.

This system uses three types of screens, four different air classifiers and three separate magnets to achieve a material recovery rate of more than 70 percent. The infeed stream consists mostly of demolition materials from the removal of local houses and businesses. The facility recovers clean fill, metals, concrete and brick and wood, as well as uses the fines it recovers as alternative daily cover (ADC). The recovery numbers for each of these products from the first year of operation are displayed in the chart on page 34.
While ADC is certainly the largest material recovered, the system was specifically designed to recover clean wood and clean concrete and brick. To achieve this, the stream is screened several times to get an optimal size ratio for the air classifiers, called air drum separators. The different size streams go to two separate air drum separators that are inline, with the first targeting a clean stream of concrete and brick and the second targeting clean wood. Ferrous items are recovered via magnets, and nonferrous metals are recovered by hand. The wood and the concrete streams have sorters as quality control (QC) to remove unwanted items from the streams, such as painted or treated wood.
OPTICS AND SCREENS
Some facilities also are using IR optical technologies—similar to those used in curbside recycling plants to recover plastics—to recover wood. However, the results have been mixed as they were not selective enough to get a clean wood stream. Recent upgrades to these units are providing more accurate recovery.
Bill Bauman of Bauman Enterprises in Cleveland has a recently installed optical unit to eject wood in his C&D plant and has been happy with the results. His system also uses multiple screens to send the right size of material to the optical unit. The functionality of the air classification units and the optical units are dependent on the sizes of material that are fed to them, with an optimal size ratio (the size of smallest item to the largest item in the stream) that is generally close to 1:4 for air systems and 1:8 for optical units. This may vary depending on the equipment and the type of material, but is a good general rule to understand.

Most screening for C&D is done using traditional finger screens, trommels and disc screens. A relatively new type of disc screen, called the Anti-Wrap Screen (AWS) from Van Dyk Recycling Solutions, headquartered in Stamford, Connecticut, uses large drums with low profile flower-type discs with 6 inches of space between the drums. These are less prone to wrapping materials, such as plastic wrapping and tarps. The screen uses alterations in speeds to change the size of the materials screened out of the stream from approximately 2 inches to 6 inches, depending on rotation speed and material type. In addition to the limited wrapping, the speed variability allows the screen to be used on a wide variety of materials.
The AWS screen was first implemented in the U.S. for municipal solid waste systems, but these screens also have been used in C&D applications with reportedly good success.
At the Zanker facility, much of the wood is used as fuel, though the cleanest recovered wood will be further processed into mulch. The outlets for different types of wood products recovered from C&D seem to be locally dependent. Dem-Con Cos., Shakopee, Minnesota, focuses mostly on wood recovery and tries to source its incoming streams accordingly, including pallets and other such items.
Dem-Con has a limited market for mulch, but has a more robust market for animal bedding and fuel for biomass boilers, and has tailored its processing capabilities to match these markets. For instance, animal bedding requires very clean, metal-free wood chips without splinters, while its customer requires the biomass fuel to have a limited size range between ¼ inch to 1 inch.

Dem-Con has constructed a much different processing system than the one at Zanker by focusing on wood chip production, including several grinders and pneumatic conveyance to process and move the chips to a covered flatbed outfeed system.
ROBOTICS AND VINYL
One of the most interesting innovations for C&D is the use of robotics systems as sorters. ZenRobotics, Helsinki, Finland, has implemented robotic C&D sort systems in several locations and looks to be part of the future of recycling recovery.
While the current robotic arms are generally slower than human sorters, they can be more accurate and do not need as many breaks. A system in Japan that uses robotic sorters operates 24 hours per day, which helps to make up for the slower throughput required by the current generation of robots.
Robotic sorters also are capable offhandling larger and heavier objects than can be considered safe for many human sorters to handle.
The technology to recover materials from C&D streams is certainly becoming more sophisticated, enabling better recovery and less labor. The markets for these recovered materials are an important driver for the level of automation that a facility may require, and it is difficult to have one without the other.
It appears that many C&D recovery facility operators throughout the country are adept at finding and providing for current and potential commodity markets within their regions. This high-level marketing is very necessary in the C&D recovery business.

With the ever-evolving marketplace and the advent of increasing recycling goals and mandates, constant attention to developing new markets (and to protecting current ones) is paramount. One such developing market may be vinyl siding.
Regional buyers of clean vinyl siding are in many parts of the country, though specific requirements for the quality and even the packaging of the siding need to be taken into consideration.
According to Kevin Reily, president and senior sales manager of Reily Recovery, Haw River, North Carolina, siding baled with horizontal balers tends to be packed too tightly for recovery at the siding processors. Vertical balers are recommended for preparing vinyl siding. The cleanliness of the siding also is important, and while there may not be many siding cleaning systems in the C&D recovery realm yet, if there is a need there will be a solution. The innovative equipment manufacturers have continued to see to that edict.
For C&D facility owners, operators or marketers, as new markets emerge (and some may disappear) there likely is a technological solution to help better separate and segregate materials in a manner that allows them to sell these commodities that would otherwise be wasted in a landfill. This evolving marketplace is why, by necessity, C&D systems owners and marketers are some of the most creative companies in the solid waste industry.
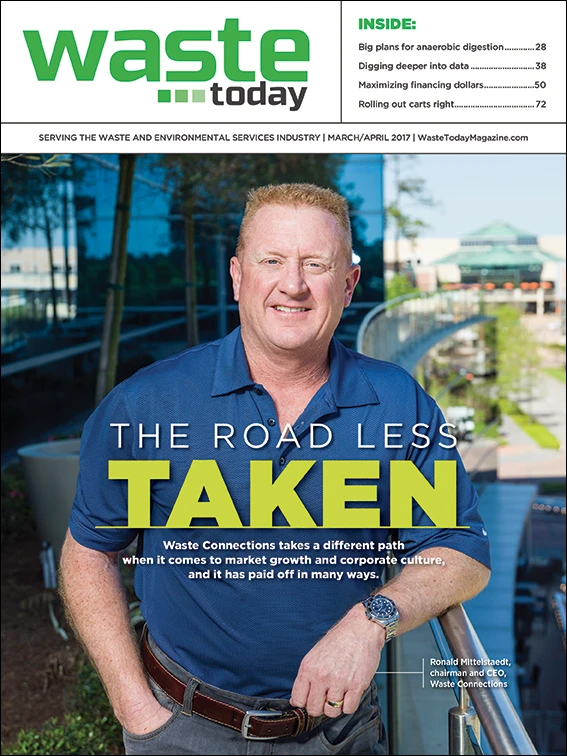
Explore the March 2017 Issue
Check out more from this issue and find your next story to read.
Latest from Waste Today
- S2 Manufacturing launching Aljon Equipment Finance at ReMA 2025
- AMCS completes 2 acquisitions
- Machinex launches Gateway service and maintenance online platform
- WastAway wins US patent for hydrolyzer infeed
- VTE appoints new leadership
- NWRA announces national awareness campaign about battery hazards
- McNeilus showcases advanced refuse and recycling vehicles at WasteExpo 2025
- Results of New Hampshire waste study reveal missed opportunities for diversion