
Since the advent of recycling programs in the 1970s, material recovery facilities (MRFs) and the equipment in them have continually evolved. The recycling industry has adapted to meet the growing demand for higher recovery and purity rates primarily by adopting new technology in MRFs.
Optical sorters and artificial intelligence (AI) have been prime topics of discussion among industry stakeholders, largely because of their high return on investment (ROI) and their ability to decrease contamination.
Industry professionals from several large waste management firms explored the central role optical sorters play in their recycling facilities at an Oct. 18 session titled “Opticals: The Sorting Workhorse” during the MRF Operations Forum, hosted by the Recycling Today Media Group in Chicago.
“We started first using optical sorters probably around 30 years ago in our business, but they have changed dramatically from a one-off in some high-volume MRFs to now, [when] you can’t build any facility really today without thinking of multiple optical sorters,” said Jeffrey Nella, regional recycling director for GFL Environmental Inc., based in Canada, and moderator of the session at the MRF Operations Forum.
Nella added that some packaging materials cannot be sorted efficiently by people because the human eye cannot identify those materials quickly enough. He said opticals can help to replace human labor to sort tough-to-identify materials.
“Sorting technologies have exploded [to] where they’re no longer just color cameras or NIR [near infrared], they span the gamut of what they’re able to see and do,” Nella added.

Evolving from screens to opticals
As the use of opticals has become more widespread and processing volumes on systems that adopted them have increased, the way MRFs are built and laid out has changed, as well.
“[MRFs] aren’t very linear anymore,” said Thomas Ferretti, operations manager for Brooklyn, New York-based Sims Municipal Recycling. “It’s not a 60-foot belt with 50 people on it.”
With these new designs came changes to cameras, needle valves and pneumatic valves, including the speed with which those valves can shoot, Ferretti added.
As optical sorters have made their way into more MRFs, Ferretti said these facilities have increased their tonnages while often maintaining purity rates ranging from 94 percent to 97 percent.
“The ROI is pretty good,” he said. “[They are] very low maintenance, so [they are a] low cost per ton to run. … And they’re very smart, which gives you the ability to keep them on your line and get through your depreciated span of payments and keep them going.”
”Sorting technologies have exploded [to] where they’re no longer just color cameras or NIR [near infrared], they span the gamut of what they’re able to see and do.”
— Jeff Nella, regional recycling director, GFL Environmental Inc.
While screens once served as the primary method of separation, opticals have quickly become a low-maintenance, cost-efficient alternative as material streams evolve.
“I think the configuration designs now are changing on screening. There’s less fiber, more cardboard and less newspaper and junk mail [that] we’re seeing, so you don’t need as much screening,” said Jim Marcinko, vice president of recycling operations for Houston-based WM. “Once you … have the paper out of the way, then you can layer in the optics and do a lot of your hard work—it’s definitely everything working together.”
Ferretti agreed, noting that purity levels achieved by using opticals and screens are very similar. Given optical sorters’ high capacity and longevity—often lasting up to 15 years before needing to be replaced—he said screens could “start to take a bit of a backseat” to opticals.
The need for purer, cleaner recycled commodities has driven demand for more advanced technology at MRFs, including optical sorters.
Between labor shortages and what many in the industry describe as the “Amazon effect,” or the growing volume of cardboard boxes in the residential recycling stream, optical sorters have helped MRF operators to adjust.
“Boxes are starting to act like small bottles, which makes it very hard for a screen to handle,” Ferretti said. “It rolls back like a PET [polyethylene terephthalate] bottle; it doesn’t carry up. Where, with the opticals, the volume may spread on your accelerator belts, you’ll get to have a lot better purity on an ejection than you would [if] you [tried] to get it over a star screen.”

Complementary technology
As optical sorters and AI continue to create a stir in the recycling industry, the advent of robotic sorting has left some perplexed about how it differs from optical sorting and how the methods can work together in a MRF. Panelists said there are clear distinctions in how each piece of equipment operates.
“They’re … performing two different tasks,” Marcinko explained. “An optical sorter is sorting, and a robot is really [quality controlling]. You have certain items where the optical sorters struggle, like [distinguishing] clamshells from PET —thermoforms—where a robot would be very helpful in removing them,” he said because the robots often are paired with AI and use a different camera. “They both have their place; they’re complementary.”
For Ronald Grinold, area manager of plant operations for Phoenix-based Republic Services, the choice between the two technologies depends on the preferred extraction method.
“If you’re trying to pull your contaminants or your plastics out of your fiber, you’re looking at 500-800 picks per minute; you can’t do that with a robotic arm. That’s where the optical comes in and gets that workhorse role,” he said.
With the advancement of opticals and AI comes valuable data on a MRF’s material streams and its operations, presenting new opportunities for MRF operators to increase their efficiency.
There’s a lot of information there, and we as an industry have been relatively primitive in using it.”
— Jim Marcinko, VP of recycling operations, WM
“There’s a lot of information there, and we as an industry have been relatively primitive in using it,” Marcinko said. “So, we can start moving into that, making adjustments, or we can look at our belt and say, ‘OK, something’s wrong, you need to go address this. There’s too much PET here.’ It gives us more information to use and run our business better.”
Ferretti added that some MRFs are taking advantage of this data.
He said, “You can get an alert … on a laptop or a tablet or [on] the touch screen on the optical itself where it could tell you that it’s seeing too much [material], which indirectly tells you there is a problem upstream.”
Eventually, he said the hope is that the robots will “talk” to each other during the recycling process.
“You can get very in-depth reports from your robotic providers right down to the point where [you learn] what it’s capturing, what it’s missing, what it tried to capture and missed, the value of what it captured over the course of a month … there’s a lot of information, but you can set parameters on what it’s expected to look at by volumes,” Ferretti said.
“[The opticals] can alert you now, but I’m sure pretty soon that [they’re] going to talk to another machine.”
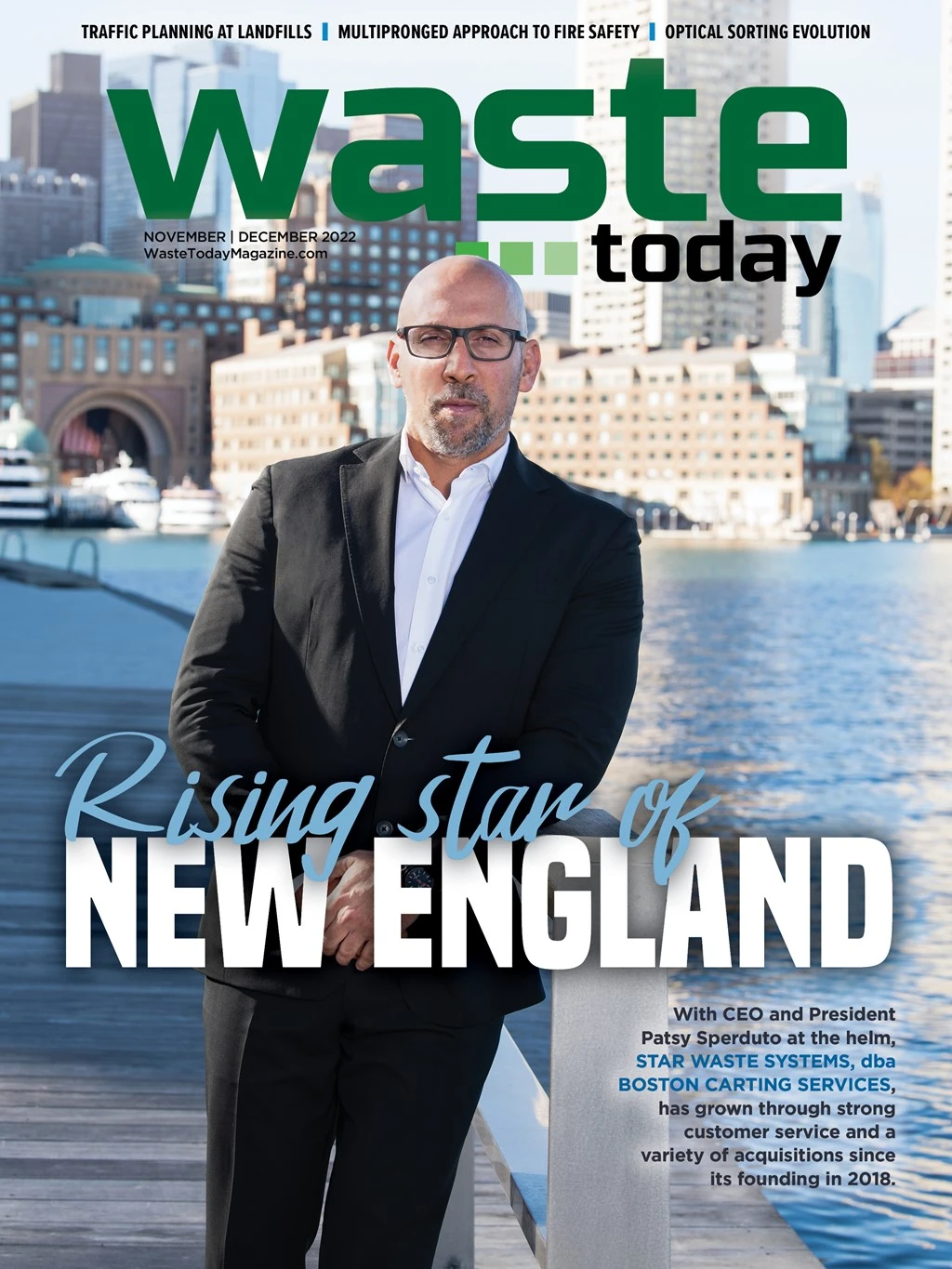
Explore the November December 2022 Issue
Check out more from this issue and find your next story to read.
Latest from Waste Today
- Startup proposes medical waste facility in Alabama
- Mount Vernon, Ohio, city council tightens waste hauling regulations
- Retail associations sign MOU to form producer responsibility organization for textiles in California
- Republic Services partners with EDL to provide RNG for San Antonio buses
- WM opens 12 recycling facilities in 2024
- Plastics recyclers report difficult conditions
- BTS Bioenergy opens Maryland Organics Recovery Center
- Meadow tabs aluminum as key to boosting beauty sector recycling