
Material recovery facility (MRF) operators have been discussing the changing composition of the recycling stream for many years. The fiber portion of the stream has evolved to comprise fewer old newspapers (ONP) and more cardboard boxes, or, as they are referred to in the industry, old corrugated containers (OCC). Also, the prevalence of plastic containers, particularly water bottles, has increased.
However, as manufacturers have reduced the weight of water bottles made from polyethylene terephthalate (PET), they can behave more like two-dimensional paper when they travel across screens meant to separate 3D material from 2D material, resulting in contamination in paper bales and less revenue.
Optical sorters can offer the flexibility MRF operators need to deal with the changing recycling stream going forward, according to panelists at the 2016 MRF & Recycling Plant Operations Forum, which the Recycling Today Media Group hosted in Chicago last October.
Nat Egosi, president and CEO of RRT Design & Construction, Melville, New York, moderated the “Sorting Super Session,” which featured panelists Nick Davis, senior cost estimator, CP Group, San Diego; David Marcouiller, executive vice president of sales engineering, Machinex Industries Inc., Plessisville, Quebec; Ted Pierpont, director of sales, Bulk Handling Systems, Eugene, Oregon; and Pieter Eenkema van Dijk, president, Van Dyk Recycling Solutions, Stamford, Connecticut.
From separation to sizing
While the panelists said optical sorters would play an increasingly important role in MRFs of the future, they agreed that screens remained necessary for now.
Van Dijk said MRFs that are handling residential material are still seeing a 50/50 composition of paper and containers arriving at their facilities, which makes screening necessary for achieving separation of 2D and 3D materials. However, he continued, “I personally believe the future is a no-screen future where the separation is done with opticals.”
While van Dijk added that sizing screens would continue to play a role in MRFs, the angled screens that separate 2D material from 3D material would be replaced by other technology, namely optical sorters. Part of his reasoning is that the OCC found in the residential stream is growing in size and in volume as online shopping grows in popularity. “With optical, you can separate the cardboard from the other paper and get the added revenue, which you cannot do with a 2D screen,” van Dijk said.

“Before you could actually [determine the] size [of] a system by counting the number of ONP screens there were,” said Marcouiller. He adds that because of the changing material stream, operators may not be able to do that anymore.
While he added that screens are “not fully obsolete now,” he agreed that the trend would be away from separation screens toward sizing screens.
Expanding sorting tasks
As the amount of OCC and other forms of packaging in the residential recycling stream increases, the panelists agreed that optical sorters could offer the best option for separating these items.
Pierpont said that because of the 3D nature of this packaging, it will end up on the container line. In the past, the volume of this material had been such that it was sufficient to have a single person removing OCC from the container line in a quality control sort. However, its increasing prevalence and the cost of labor could favor the use of optical sorters for this task at some MRFs.
When it comes to items like smaller juice boxes and pouches, van Dijk said, “These items are easily recognizable with optical.” However, he added that their volumes don’t always justify their separation. Van Dijk said his company’s approach to recovering these types of packages has been to use an optical sorter with two tracks. “You let the material go on one track, and you shoot out cartons. And, then, on the second track, you shoot out whatever [else],” he said, offering polypropylene (PP) as an example.
“So, you can invest in only one optical sorter but do two products,” van Dijk continued, adding that the volume of cartons doesn’t justify an optical sorter dedicated solely to that task.
When it comes to the configuration of future MRFs, van Dijk said he believed the smaller ones would include an OCC presort, a fines screen and an optical sorter to remove small OCC. MRFs that process commercial material may want to include a second optical sorter to recover office paper.
The addition of a third optical sorter would enable the MRF to process single-stream residential recyclables, van Dijk said. “But the small cardboard becomes more and more important, and you have to use opticals for that, in my opinion,” he added.
Egosi asked the panelists what the breaking point was to justify installing an optical sorter in a residential MRF to create sorted office paper (SOP), to which van Dijk said it makes more sense in MRFs handling commercial material.
However, he added that MRF operators need to be aware of the various types of spectroscopy available in optical sorters to select the best option for the task at hand. “If you want to do paper from containers or PET, HDPE (high-density polyethylene) or PP,” van Dijk said, “you need to have near-infrared (NIR) technology. If you want to [sort] SOP from other paper or cardboard from other paper, you need near-vis (visible) technology.”
Optical sorters can incorporate both types of spectroscopy, but they will be 20 percent more expensive on average, van Dijk said, adding, “It might be worth spending the money upfront for the tonnage of the future.”
Davis said, “It’s worth the extra capital upfront to get all the wavelengths you need.” He said doing this gives a MRF operator flexibility to respond to the changing recycling stream.
Positioning for success
When it comes to the optimal configuration of equipment in a MRF, Davis said, “I think there are a lot of different ways to design a MRF. I think there are some hard and fast rules that you have to follow, such as the magnet must be in front of the eddy current, as we all know.”
He said designers must be more flexible in their approaches to container lines.
“There is always going to be a cost-benefit decision to what we are doing,” Davis continued. “Taking out PET first really cuts down your volume to your next sorter, which allows you to downsize it slightly. Taking out the HDPE first, it’s a much easier target, and you’re going to get a much better, cleaner PET stream at the end.”
Van Dijk said PET and HDPE are present in the same percentages in single-stream residential material by weight, but the HDPE is heavier, meaning more PET material is present overall. He suggested removing the PET first because there is a small chance HDPE accidentally will be removed with it because of its heavier weight. “If you do PE first, there is a bigger chance that you can send PET with it,” he added.
Ensuring performance
Ongoing preventive maintenance is essential to the proper function of optical sorters. Pierpont said ensuring the strength of the light source should be a MRF operator’s first concern, and that means cleaning the sorter’s glass and replacing its bulbs.“Checking the nozzles is important,” he added.
Davis agreed, saying the valves on the ejection array should be examined for damage to their O rings. “Usually, when we see a problem in the valves, either they get stuck open or closed or they are leaking. You can trace that back to the compressor system,” he said.

If the valve seems to be stuck in the open or closed position, Davis said, it could mean dust is getting in from the compressor. If they are leaky, he continued, oil or water from the compressor might be to blame.
“Valves are expensive, so it is good to maintain the compressor to keep your optical sorter performing,” Davis said.
However, 50 percent of the time, the problem can be upstream of the optical sorter, Pierpont advised, suggesting that it could be seeing too much paper from the polishing screen or contamination because of disc wear.
Future flexibility
While the evolution of the recycling stream is inevitable and beyond the control of MRF operators and systems providers, optical sorters could represent the sorting equipment with the most flexibility to respond to the changes to come, according to the panelists.
“I must say the traditional single-stream system with screens is not very flexible,” van Dijk said. “And that’s why I don’t want to repeat myself too much, but I think the future will be an OCC screen and then three opticals. You have less labor, you have more flexibility for the stream of tomorrow.”
Davis said, “More optical sorters and fewer people is really the answer.”
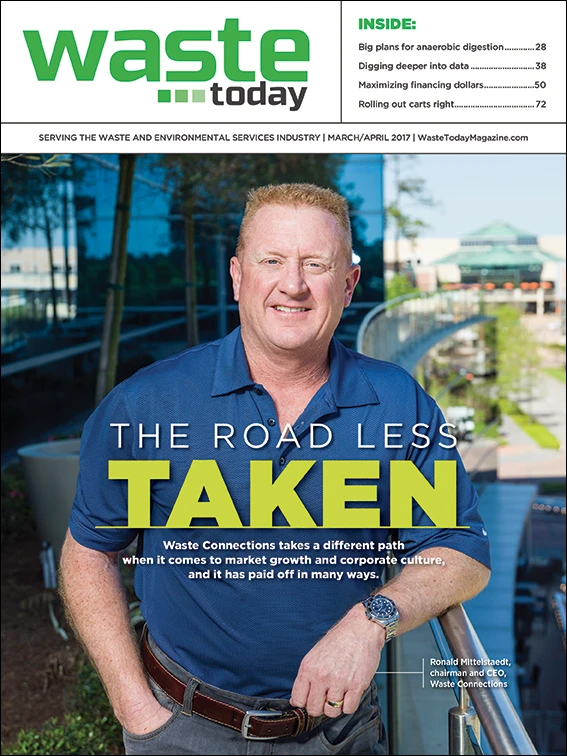
Explore the March 2017 Issue
Check out more from this issue and find your next story to read.
Latest from Waste Today
- Ecore program recycles outdoor track material at Louisiana school
- Heidelberg name now used at former GRR facilities
- USDA grant helps Wyoming county lower composting costs
- Hoffman Sanitation Services acquires Wildhorse Waste Services
- US Tire Manufacturers Association supports legislation boosting tire retreading
- Vanguard AD installation goes online in Wisconsin
- Struggling with excess wood debris?
- More of what the world needs, less of what it doesn’t