
A question that often arises at the beginning of a material recovery facility (MRF) retool or transfer station project is “What are the key factors to kicking off a project in the correct manner to maximize the productivity of your team and the entire project over the coming weeks and months?”
Many factors contribute to a successful project from the request for proposal (RFP) process through the construction team involvement, ensuring communication is continual throughout the project.
The RFP
I’ll quickly touch on the RFP process without getting into the work that takes place prior to the issuance of the RFP but only what takes place after the RFP is distributed.
The RFP can be distributed in a variety of ways: 1) to design/builders, 2) to equipment suppliers or 3) sometimes a hybrid is used where an RFP for the building modifications is issued separately from the equipment RFP.
This article discusses a project where the RFP went directly to the equipment supplier, which was then responsible for finding a design/build contractor or general contractor and design team to assist in developing the pricing and other information required in the RFP. In such a case, the equipment supplier would generate the formal response to the RFP and would answer any questions that arise from the owner.
There isn’t a right or wrong way to issue an RFP for a project; it really depends on individual needs.
Once the RFP is issued and the selection process is completed, the contract is signed and the work on the proposed project begins.
In this example, the equipment supplier is holding the master contract with the owner and a subcontract with the design/builder. With this scenario, all communication with the owner (whether it is a private or public project) needs to flow through the equipment supplier as the entity that holds the master contract. This is key to the process, as the equipment supplier ultimately is responsible for staying within the project scope and budget as well as for ensuring the design remains consistent with the RFP response. If this happens, the risks on the construction side are lessened.
In this RFP scenario, the design/builder or general contractor is being asked to provide a budget for the project during the RFP process. This is important to note because it is early in the overall process. The design/builder or general contractor is going to be asked to hold to this budget until the project is completed.

This direction needs to be provided during the RFP process because many external factors that affect the construction budget need to be built into the budget early on. These include permit fees, material cost escalations, labor cost escalations, etc. From the time an RFP is launched and responded to to when a contract is in place likely will be around a year or more.
Inherent risks must be factored into budgets to cover a calendar year. It is also important that the contractor supply a complete scope of work and list of inclusions/exclusions as part of the budget for the equipment supplier to include in its response. This will help the owner to better understand the scope of work included in the proposal.
The kick-off
Now that the RFP is complete and the supplier, design team and contractor are under contract, it is time to bring the entire team together. I would recommend a kick-off meeting at the project site with all involved stakeholders attending the walk-through. The goal of this meeting to is close any gaps on the scope and to discuss the steps moving forward.
Everyone needs to understand visually what is included in the project, how it will impact operations and what shut down may be required. It also allows everyone the opportunity to put a face to the names for all parties involved, including the contractor, equipment supplier and owner. This is very important when building a relationship among all parties and assists with communication going forward. It also helps to assemble and distribute a project organization chart identifying all persons involved and their role in the project.
As with all meetings, the items discussed at the site visit should be documented and issued to the team after the meeting is concluded. This is important for all meetings that take place throughout the project. Documentation shouldn’t be limited to meeting minutes; any scope or schedule changes need to be clearly identified, and a budget update/change order needs to be developed immediately to allow the owner a chance to review it and ask for changes, decline it or accept it. All additional items that need to be tracked should be added to a project “tickler” list for the project manager to stay on top of. This list would then be discussed on the regular project calls.
The Design process
Once the kick-off meeting is completed and the results are documented, it’s time to begin the design process and to hold regular meetings to discuss issues, talk about options, recap progress and bring up new items. These meetings are critical to creating an atmosphere of open communication, which leads to consistent progress. It’s important that all stakeholders participate regularly in this process.
While the facility/site design is progressing, the equipment supplier also is working on continuing the design/layout. Communication between the equipment supplier and the design team is critical. The earlier the equipment supplier can get its final designs to the design team, the better off the project is.
Supplying this information as early as possible will lead to higher quality drawings and provide more time for the contractor to identify potential issues. A lot of equipment coordination needs to be factored into the architectural, structural, mechanical and electrical drawings for the building.
The fewer changes the equipment supplier issues late in the design process, the higher the likelihood the project will be successful in limiting design and construction issues and encountering budget changes or overages.
The next step to ensure the success of the project is regular reviews of the drawings while developing the permit drawings. This is from an equipment perspective and a building/site perspective. You will need to set your own review periods based on the project’s level of difficultly and the teams’ input. Reviews at the 50 percent and 90 percent points, at minimum, are recommended. Three review points would be optimal and are used for more difficult projects.
The construction team should be involved in all design reviews, as well as any discussions that affect the project phasing, scheduling, site activities or means and methods for the project. This allows the team to have complete buy-in to the final designs and drawings and should help to limit design deficiencies when the drawings are completed.
One important factor during this phase is to set the expectation with the design team early on regarding what you would like to see included in the review sets. If it isn’t clearly defined, you are subject to the opinion of each design team member, and that never turns out well.
At these same review points, you should receive a set of the equipment drawings to check for contradictory design issues and to help define/ensure pit locations, drains and power drops, among other things, are in coordination or moving in the right direction. The reviews should be conducted by the equipment supplier, owner, design team and construction team. This way all perspectives get to weigh in on the direction of the drawings and point out any potential issues in the plans.
After issuing the drawings, a web or in-person meeting should be held to do a page turn of the drawings and to review all comments from the various teams. Changes can then be incorporated into the next drawing review set.
Let’s recap where we are to date: The RFP has been issued, contracts are in place, a kick-off meeting has been held and team members introduced, regular weekly or biweekly calls/meetings are being held and drawing review sets are being issued to ensure project coordination.
The construction team
So far we have placed the primary focus on the design team, equipment supplier and owner. Now we have to make sure we get the construction team involved to help plan the site activities, shutdown time, phasing (if required) and drawing review for constructibility and identification of any items that may help to reduce material costs, reduce overall construction time or have an impact on the owner.
The construction team provides a completely different perspective on any project. While it hasn’t been mentioned earlier, I would highly suggest this team be invited to and attend the kick-off meeting on-site so it can see the building and the site to begin visualizing the changes being made.
The construction team’s input is then factored into any proposed changes and the final designs/ layouts for the facility.
The construction team should be involved in all design reviews, as well as any discussions that affect the project phasing, scheduling, site activities or means and methods for the project. This allows the team to have complete buy-in to the final designs and drawings and should help to limit design deficiencies when the drawings are completed.
Ongoing Communication
Maximizing communication and having the entire team involved from the outset are the best ways to have a project work through the various steps in a smooth, precise manner. Everyone involved should ask as many questions as possible for complete clarity; questions lead to more questions, which help to weed out potential gaps in the scope or errors within the design.
It also is advantageous to have a team that has experience in these type of projects so it can incorporate lessons from past projects and provide feedback on design ideas and concepts.
MRF projects typically are complex and require a lot of planning and coordination. It is important that you take the proper amount of time to include the right team members, work through the contract details and get through the design process. These are not things that can be rushed, unless you want to encounter a myriad of problems throughout the course of the project.
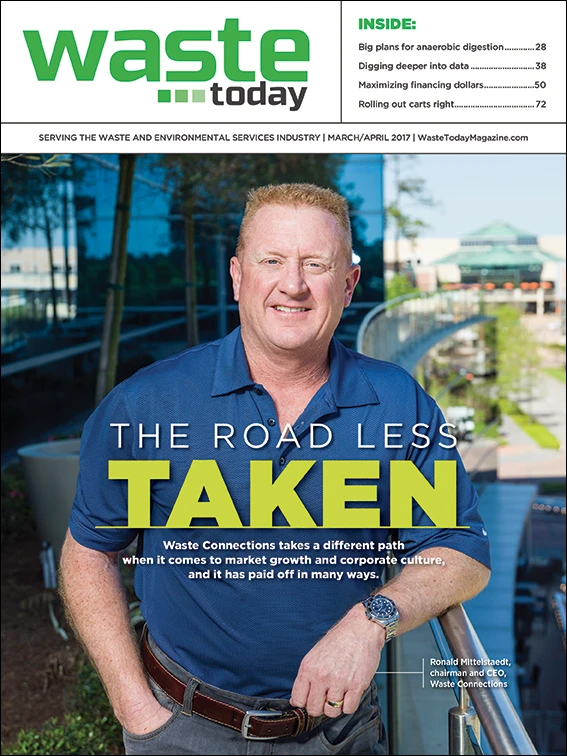
Explore the March 2017 Issue
Check out more from this issue and find your next story to read.
Latest from Waste Today
- USDA grant helps Wyoming county lower composting costs
- Hoffman Sanitation Services acquires Wildhorse Waste Services
- US Tire Manufacturers Association supports legislation boosting tire retreading
- Vanguard AD installation goes online in Wisconsin
- Struggling with excess wood debris?
- More of what the world needs, less of what it doesn’t
- Gaeta Recycling: Driving efficiency and sustainability with SENNEBOGEN material handlers
- Enhance mobility using Sebright Products Portable Compactor Solutions