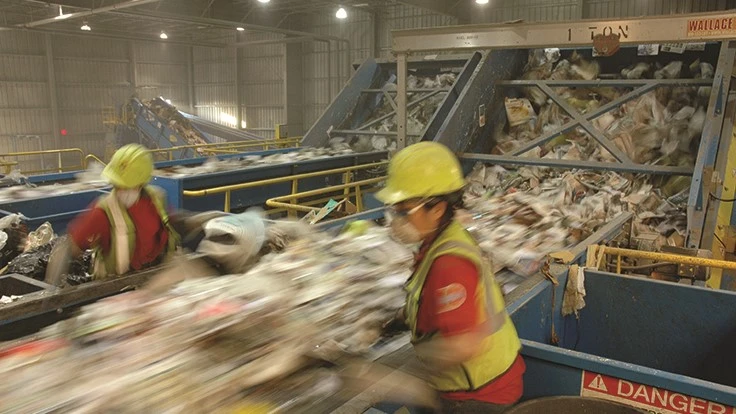
Photo from Recycling Today archives
While refuse and recyclable material collection continues to hold the ranking as the sixth deadliest occupation in the U.S., the overall industry has made strides in recent years to create a safer working environment for personnel.
These efforts can be seen through the implementation of new technologies, proactive safety measures, as well as better planning and facility design—especially at material recovery facilities (MRFs). Given the many hazards that can be found within a MRF, whether it be on the tipping floor or at the sorting line, these types of facilities can serve as a prime example of how to address and mitigate safety issues.
Keeping comfort in mind
For Bob Gardner, senior vice president at Long Beach, California-based SCS Engineers, applying general measures to maintain a comfortable space for personnel is the first place to start.
“I spent a week during the commissioning of a facility in Maine and had a lot of time to reflect and look at what was going on around me,” he says. “I [created] a list of seven things that I observed [regarding safety], and the first one was noise protection.
“There were a number of people who were in that facility that didn’t have [noise protection], and I can see how over time that can have an impact on your hearing—especially when you have a big MRF with a lot of motors going, machines moving, things clanking all over the place; it’s a noisy place.”
The second area of concern for Gardner was dust control, which can pose hazards such as lung and eye irritation, choking issues and reduced visibility. When processing solid waste through trommels, screens and conveyors, Gardner says dust generation is inevitable, thus necessitating the use of masks or respirators.
“There are so many places within the MRF where dust could be generated,” he says. “When you go to the tip floor, when it goes into the hopper when you’re loading it., when it goes to the trommel or through all the screens, so there is a real [risk there].”
A safety hazard that has garnered significant attention in the media has been the issue of medical needles on sorting lines.
“This is a real issue. I sat there and looked at the fines line [at the Maine MRF] … and the amount of medical stuff that was on that fines conveyor was phenomenal,” Gardner explains. He adds that MRF personnel have expressed growing concerns surrounding needle pricks, leading many facilities to begin experimenting with different gloves to better prevent medical needles from piercing skin but also allow for enough dexterity for workers to properly do their job.
Be aware of common hazards
In terms of facility planning and design, Gardner says slip hazards should remain top of mind when considering personnel safety. Stairs going up to platforms or liquids on the floor from “drippage” are often slip hazards, so proper stair and hand railing designs can help prevent dangerous falls. Facilities should also keep sorbents on hand to deal with liquids on floor areas.
“Slip hazards are more of a design issue than anything else,” he says. “It’s important to make sure you get nice nonslip surfaces and railings and so forth, which are generally required by OSHA (Occupational Safety and Health Administration).”
In addition to proper design, being aware of equipment hazards at a MRF also should be “common sense,” according to Gardner. Given the many rotating parts found at a MRF, he says equipment should be respected and personnel should have awareness of daily operations and their hazards.
“I always joke when I’m doing yard work that anything that isn’t eye level, you don’t see. So, being aware of the equipment hazards, trip hazards and the like is really important,” he says. “It’s more of a self-awareness kind of thing.”
This kind of awareness also comes into play during the startup and shutdown of equipment, which often includes specific processes and procedures. For the workers involved, Gardner says proper training can help keep everyone on the same page.
“In a MRF, lots of things can get wrapped around the axels of the various screens ... that are turning, so you don’t want somebody [working] in a machine when you ultimately turn it back on,” he says.
Latest from Waste Today
- Thinking about selling your waste business?
- Industry civil suit heading to trial in 2025
- SSI equips Japanese company for diverse operations
- Waste Pro cites contract success in 2024
- NWRA commentary: Comprehensive immigration reform could be legacy defining moment for the second Trump administration
- EPA takes steps to require MSW incinerators to report toxic chemical emissions
- Food waste composting system coming to Canadian province next year
- Updated: CAA submits final draft program plan in Oregon