
In the world of compressing and compacting—be it cars, or aluminum cans the market dedicated to reducing the size of trash has become faster, more sophisticated. Moreover, it has also become much safer as Sean Usoff, director of sales and marketing of International Baler Corporation of Jacksonville Florida explains.
Safety by design
“There are two aspects always at the forefront of our decisions. Safety first is critical in this business,” he says.
“Unfortunately, while we all do our best—which is all you can do really—people always seem to find a way to hurt themselves. So, we see safety as a first and foremost concern.”
In the baling business since 1946, the company manufactures vertical and horizontal baling equipment that is distributed worldwide. The various machine sizes are either fully automatic and deliver tied-off bales, or semi-automatic with a manual tie-off operation. Serving multiple markets in recycling, distribution, scrap, municipalities, textile, and specialty markets, their balers make short work of mountains of trash every day.
“From cardboard to cans and plastics to paperboard with everything in between, our machines can push out 20-30 tons per hour in our larger units. But large or small, every machine is designed with safety and accident prevention in mind,” Usoff says.
“As a manufacturer, we have to follow ANSI [American National Standards Institute] standards and in fact, we are a member of their board and advise them on aspects of safety. We have to keep up with UL requirements [a safety science company, formerly Underwriters Laboratories] and OSHA requirements on baler operations. Anything that might be on a piece of equipment needs to fall under the safety purview.”
He adds the second consideration is ongoing and proactive evaluation of their equipment.
“We are always thinking ‘how can we make changes, improve our technology; how are customers using our equipment and running the machines. How do we stay ahead of the game to prevent accidents and keep people from harm's way?’”
One of the improvements he cites is making maintenance safer. The company has added touch screens that allows operators to see the maintenance intervals of the machines and making it easier to see what needs to be done.
“Both lack of maintenance and lack of training, issues we are very concerned about, can be bolstered by the screen. They have thorough diagnostics and there are notifications when to replace filters, alerts when a switch is not functioning right. There’s a lot of direct intervention you can have now. We actually have the entire operation manual of our balers accessible to those operators right there.”
Usoff says that the machines need to be smarter because the labor force may not be getting the training they need, and this leads to accidents. Even 15 years ago he said machines had manually operated controls, which makes it easier to have potentially unsafe situations.
“The machine of today is actually more intuitive about its working operations than the operators, and, actually the more automation you have the more safety issues you need to cover. The more the machine does things on its own is where you run into higher risk.”
On their large, 2-ram machine they installed a series of safety locks that are cast steel locks in a series.
“If you have to get in the hopper door you can't override the machine without this system. When you turn the lock with one of them, it shuts the machine down. Then you go to the hopper door, put that key in, and then there's a key to the control panel. It's a four key sequential system and when used in this daisy chain fashion closes all the guards, and you literally cannot have any running operation when these are in use. If nothing is running, no one can get hurt. It opens and closes in a sequence that requires human intervention at each step.”
With machines moving a lot of critical high-volume materials, Usoff says operators and managers don't want to shut the machines off if there is a hopper jam or a problem, citing lost productivity.
He describes one scenario a customer offered that illustrates the effect of a downtime shut-off.
“If you are a small company and you add 20 seconds for safety for each bale, that becomes 1.5 hours of production time per day they've lost. It doesn't sound like much, but it adds up to 500 hours over a year of lost production time. If you are a small company, you can't afford to eat that loss.
“As an OEM [Original Equipment Manufacturer] we are very sensitive and aware of the financial concerns of customers and yet we always have to worry about protecting liability. You have to make them as safe as they can be, you just can't not do it,” he says.
“The human reaction is to try to correct it or fix it while it's running. We try to make that impossible. While money is volume and getting the maximum amount out in an eight-hour day is understandable … the risk and liability is huge.”
Another safety feature is the safety interlock, Usoff says.
“You have two kinds of electronics and two halves of a switch on the hopper door. A key to open the door and a receiving switch to the hopper. So if you need to get into the hopper, the key goes into the switch and the circuit is closed. Years ago it used to be a magnetic switch, but those could be jammed and bypassed. Today we actually rivet the switches to the housing to limit any override possibilities.”
The other component, training, is essential as well, but it has its challenges, he explains.
“We don't require our techs be on site for the start-up, but we recommend that the installation be performed by us or an authorized dealer. This helps them get familiar with the machine and they learn proper operations.”
But Usoff adds the operators who work these machines are a high-turnover labor force. They might stay only one year, often much less, which means that people who learned the proper operations take that with them, and it may not be passed down to the next workers.
“Most bigger companies understand safety and prioritize safety. What we see more of the lack of attention to this is in the small industries. Anything that slows them down is lost money. And the bigger the machine the more safety you have to worry about. On both the manual and auto-tie machines there are moving gears and all these need to be safety guarded and air locked to avert harm.”
The machines also have warning labels on pinch panels, and notations for electrical panels. They do offer the manual in several languages but, as the standards are always changing, “The manuals are constantly evolving and being reissued since we have to keep up with standards both in North America and in other countries, as well.
“Safety is a round-the-clock concern. It's never ending, and accidents can happen in a blink of the eye. We take pride in the efficiency of all our balers, but we work every day towards preventing disasters from happening, and we never stop thinking about how to do it.”
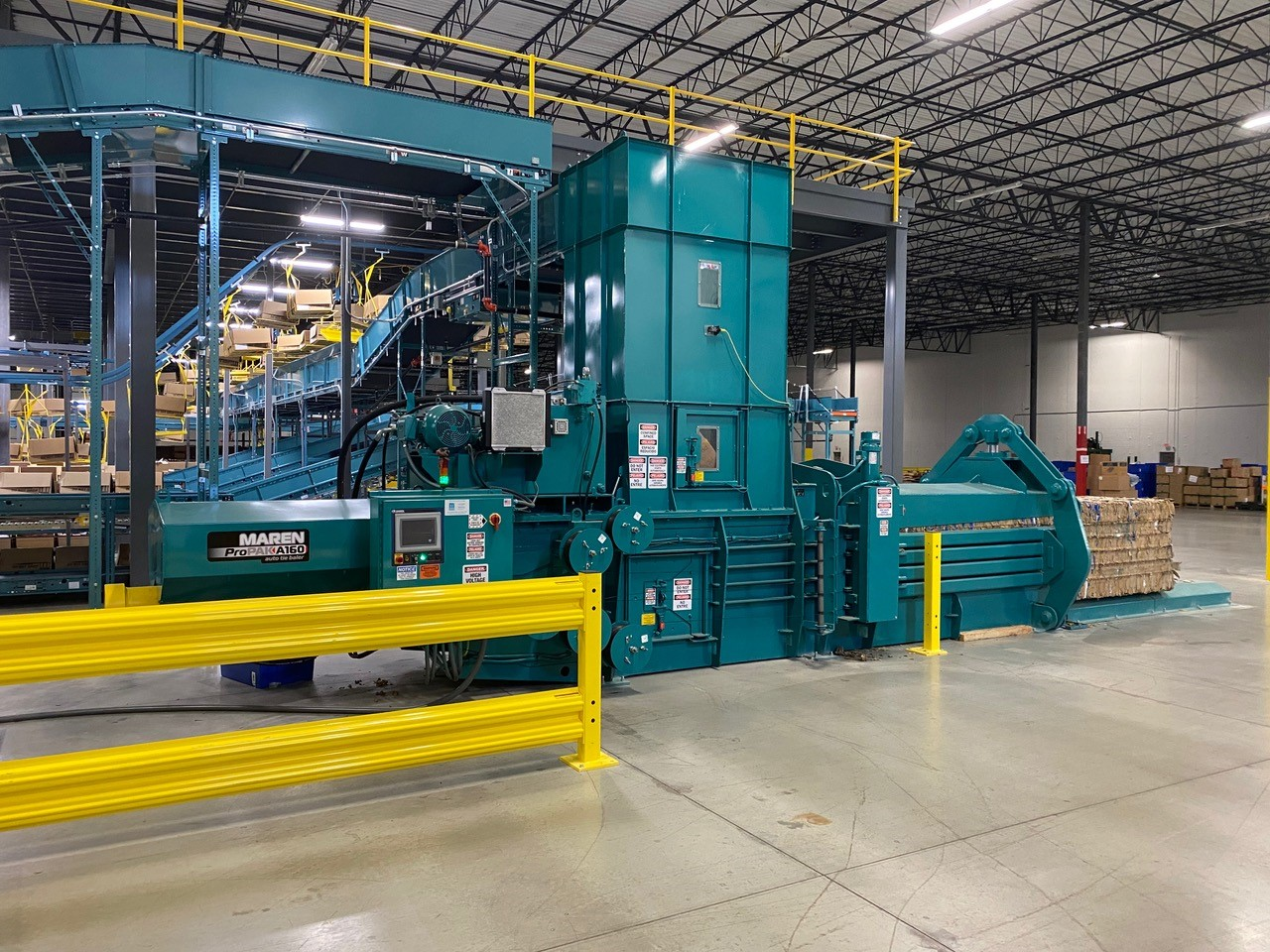
Purpose built for a critical task
With more people staying at home from COVID restrictions, the waste arena has experienced some dramatic shifts in operations in the last few years. Alex Papp, BOMAG Manager of Landfill Products says recycling has responded by changing the way it has been sorted, and he adds, “According to municipality statistics, landfill disposal is way up.
“What this means is if you have 50,000 more tons of trash coming to you each year, you are more rapidly consuming your air space. If your site was designed for 10 million tons and your intake has increased exponentially, the life expectancy is cut in half. So, getting the most air out of the space you have by compacting as effectively as possible becomes essential.”
Papp says the key to this is adding pressure, as “the more pressure you have to compact the trash, the better you remove the voids that would consume valuable air space.”
Pressure as in terms of weight. Think of those cast iron gadgets that take the crinkle out of frying bacon, but a whole lot bigger. The task is made ever more crucial in the face of what Papp says can be a ten-year turnaround time to building a new landfill.
“Getting the most out of what you have right now is essential. For example, if you have a million yards of air space and you bring in 10,000 yards a year, if you can condense that to 8000 tons then you can bring in more and stay open longer.”
He says their machines are unlike any other on the market and their seven different sizes of compactors are built specifically for compacting. Landfill operators can choose, based on weight of the machinery, the right machine that is most suited to their specific landfill needs.
“At 30' long, these are big pieces of equipment pushing trash. The 60,000 lb. machine is the smaller unit and the largest has 125,000 lbs. of compacting capacity. The tips on the wheels that do the work are 9.8 inches long, and we have a 10,000-hour warranty on those wheels; there is no changing of tips as on other machines.”
But with their massive size and weight comes safety concerns that on a landfill, is a precarious landscape on the best of days.
“Having a good sight line and understanding your position outside, from the inside, is done with our clear in-cab screen display units. These tell you the percent of slope you are on from both front to back, and side to side. With our true, four-wheel drive wheels and articulating oscillating joint, you are always stable on the ground, in all types of slope conditions. There are four independent drive pumps that drive the wheels, and four drive motors and two tandem pumps keep it running all the time.”
Other features Papp describes are the new open-air steps with heavy steel tread for good grip, especially if there is ice or rain. There are no slip trips or falls with this new design, he affirms.
“Our platforms are also obstacle free, we install mirrors with plane and spherical sections to increase field of vision and there are rails and grab bars all round, and a higher cab door with a split window so you can leave it open if you need to.”
While comfort may not always be equated with safety, Papp emphasizes that, “Good instrument and ergonomic seating design is crucial, it should be adjustable and allow operators who might be sitting in there 8-10 hours a day, to concentrate on the job outside—not on how uncomfortable, cold, or distracted they are.
“Having clear views all [a]round is part of that as well. Our engine air intake is in a central position that does not obstruct vision, and our seats are electrically controlled and heated—these all contribute to comfort, ease of operation, and therefore safer, more attentive operators.”
Other options that customers may want are different types of blades, or “Customers might want a winter package that has a pre-heating element, radio-controlled climate control, and if you are working on asbestos, we have a closed and ventilated cab option for those landfills. Plus, we have a rear camera system which is standard, but you can add an obstacle detection system for rear area monitoring.”
This BOMAG compacting line, he reports, are machines of exceptional quality and the only purpose built machine for the market.
“That's the only thing they do, and they will do it well for you, every day of the year, in all kinds of conditions and weather.”

Diligent innovation lessens danger
“The biggest source of accidents in this business is people not following standard safety procedures, and, often even intentionally defeating the very safety features that were installed to protect them,” says Todd Wondrow, President of Maren Engineering. The South Holland, Illinois-based business has been making balers for more than 60 years and, “If it needs to be baled, we likely have a machine to do the job,” he says.
“That's all we do is make recycling balers and supporting equipment for managing any waste situation; we have customers in literally every industrial segment you can think of.”
But in terms of safety, Wondrow says, “We've been doing this since 1962 and we constantly configure new strategies to reduce the risk to people who are running the machines.
“Customers can choose just the right baler for their needs from our many different models, including full eject manual tie balers making only 1-3 tons per hour, to open end auto-tie and two ram balers with ram forces up to 50,000 lbs and process rates in excess of 50 tons per hour.
“The open end can produce bales from 42" high, up to 78" long with a bale weight ranging from 1000 lbs to about 3,000lbs.”
While all machines are equipped with multi-language safety and warning decals; nonetheless, “What makes these horizontal balers so useful is also what can make them dangerous.
“Horizontal balers run in a semi, or fully automatic mode and use photo-eyes to initiate the processing of materials. The baler hopper is loaded with a conveyor, an air system, or even manually from a fork lift, or a bucket and skid steer. Once the material is in the hopper the ram goes forward to shear off excess material that doesn’t fit in the bale chamber and then compress the remaining material.” But problems happen when people try to intervene in the operation.
Wondrow reports that a lot of the fatalities and bad accidents occur with horizontal balers when people are trying to extricate or clear a jam in the hopper, and who then fall in. And, as he cautions, “The photo-eye doesn't distinguish a human from the cardboard, carpet, plastics, or whatever else.”
This is where Wondrow says training—and vigilance with the training program among operators and managers—will make the difference in your company safety record and the ability of your employees to return home safe every day.
“When the installation crew commissions the machine, they provide training to the facility managers and operators, and they often stay over two or three shifts to cover all the workers. These machines can be running on a full-time, non-stop basis, so we want everyone to get the message.”
But he says after they leave that position, if the facility manager doesn't appoint a training person, there’s a potential to have “no one designated to pick up that responsibility to train new people.
“This can be a high-turnover-rate job, so without a designated trainer, new people will not have the benefit of really hearing how to have respect for these powerful machines. You shouldn’t be thinking of how to get around the safety measures because they are designed to keep you safe.”
Wondrow says there are already plenty of rules and regulations but that the baling arena could benefit from facility management taking a more aggressive stance on training and reinforcement.
“Our approach is that you can do all kinds of things with regulations but if we as manufacturers take steps to remove the danger in our design, that can have a more permanent impact on overall safety.
“For example, there are things you wouldn't equate to safety that we have implemented on our machines. One feature is our automatic hopper bridge detection. Let's say you are dumping in cardboard boxes and the hopper is too small, and the box bridges, preventing it from falling in, the machine will try to clear it on its own. This can prevent your operators having to poke around in the hopper to clear it.”
While this is an efficiency feature in the minds of the customer who see the machine as being able to self-correct a problem, “We at Maren see it as a safety measure that keeps hands out of the hopper.”
There is also sheer jam detection and prevention, Wondrow adds.
“The baler can detect a sheer jam and can often clear it on its own. Yes, it is efficiency, but it is also safety. And then there is the eject jam correction feature as well.”
Each particular baler runs at a certain speed, whether it's one or 20 tons per hour, and “for every few hours, if there is a half hour of down time to clear jams or problems, then it makes the baler not efficient, so the controls that both reduce jams and also keep people safe are doing double duty in efficiency for the customer.”
Another big factor in efficiency is maintenance. Wondrow says their machines are designed with a minimum level of required maintenance, and that many problems have self-correcting features.
“One notable feature is the self-clearing aspect in the rear of the machine on open-end auto-tie balers. The product is automatically expelled without the need for a machine shutdown, and this keeps the operator safe.”
The benefit to this design is that customers don't need a full-time watcher, although he says some models do require an operator, as in the case of the manual-tie machine.
Although some balers are equipped with an open-top hopper, Wondrow says you can't really get near any dangerous parts of the machine. “This is because of the combination of height and distance making the hazards pretty much inaccessible from a person standing on the ground.
“This is referred to as “guarding by distance,” and we purposefully build them that way adhering to the ANSI Z245 recycling equipment safety standards that mandate those measurements.
“Despite all of the systems designed to prevent the operator from having to enter the danger zone, ultimately, sometime it will be required. When that happens, the facility is required to have a LOTO (lock out, tag out) program in place. This is required by OSHA and is independent of us as a baler manufacturer.”
He explains that LOTO requires that the source of power is turned off and each person who is entering the danger zone place their own personal lock on the power source. Each person has the only key that opens their lock, “so we all have to take our lock off to ensure we are clear, and one person is not in control to independently override the system. OSHA is very clear on this and there is no margin for error here.
“You might think after all of that, there must be enough safety built in, but we further equip our balers. We have safety devices that use dual redundant monitoring circuits through interlock latches and devices at any danger locations. Any of which, when tripped, will shut down the baler. The important note is that these are not alternatives to LOTO, but additional safeties, and operators must receive training and feedback to reinforce this.”
Wondrow says his staff is accustomed to watching the operations and looking for potential red flags where an opportunity for mishap in the operation is just waiting to happen.
“We try to prevent it rather than relying on the facility manager to police it.
%2
Latest from Waste Today
- SWANA releases report on aging WTE facilities
- New economic assessment reveals cost benefits of California’s SB 54
- Premier Truck Sales & Rental opens new facility
- TeknTrash Robotics, Sharp Group partner on humanoid robot pilot
- Stadler equips mixed waste sorting plant in Sweden
- Mack electric collection truck delivered to New York
- How waste management fleets can navigate a volatile labor market
- Sagepoint Energy acquires Peoples LFG