
In the old days there was just plain old "plastic," but in today's world that nomenclature has expanded to embrace at least eight different kinds and types of plastic! While originally touted as the packaging answer to replace heavy materials like glass and metal, we are unfortunately so overburdened with this convenience that we're overwhelmed.
Recycling and reuse seem like the solutions but it's far from perfect, even after decades of refinements. So many types, so many distinctions; sorting, identifying and processing—it's just short of a waste stream nightmare. Yet it is accuracy in making those distinctions that are key to both an efficient recycling program and more responsible environmental stewardship.
“Here was an opportunity for getting municipal organics out of the landfill, so we created several diversion streams.
The good news is, novel ingenuity and sophisticated technology are decoding the challenging enigma of “What Is It?”

Staying ahead of the changing times
At the beginning of WW2, nobody was thinking too much about recycling. But when the Fresno, California Orange Avenue Landfill opened in 1941 it was destined to evolve as a leader in the recycling industry of the future. Rich Caglia, President, Corporate Development of Caglia Environmental, and third-generation owner, explains.
“My grandfather started the landfill back then and by the 1960's he started his own recycling operation. This was in stride with the Keep America Beautiful campaigns that began in the 50's and promoted a public message to put trash in receptacles to help curb littering.
“On Saturdays, he had free admission to the landfill and residents could bring in trash and demolition materials and just drop them off. This was cutting edge public service back then. And we were just a few years ahead of the first Earth Day and the launch of the EPA that really was the springboard for what we now call the Environmental Movement,” Caglia says.

“One of our goals was to take edible food and get it to people. By working with a local organization and Fresno Metro Ministries, Food to Share, and other partners, we bring food to people who need it. Then, we take other food to cattle and other viable processing operations. It doesn't sit and rot in the landfill, we find a use for it all. It's efficient recycling and a good public service for our community.”
He also adds that connecting with the local fire department for tours is another public relations effort to consider.
“One thing I would recommend to other site owners is to invite your local fire fighter teams to become familiar with your facility. In the event of a fire or accident they will already be familiar with your location, its layout, and any specific incident command protocol so that things would be managed as you would like them to be.”
The organization had big plans in the works to increase efficiency in collecting polypropylene (PP), when the pandemic short circuited many activities.
Caglia's Division Manager, Cedar Avenue Recycling and Transfer Station (CARTS), Mike Ledieff describes their next round of change.
“We had a 20-year old facility and it was time to look at new technology to increase both safety and our efficiency. By introducing an auger to bifurcate the single stream of material you can more easily see what's on the belt for sorting. But I became educated on polypropylene (PP), and up to now, due to its being nearly indistinguishable appearance of other packaging such as HDPE, the PP materials could not be effectively separated.”
This was an important challenge. Ledieff says the unique properties of PP are prompting an uptick in being adopted as a food industry packaging. But, while one yogurt cup looks like the next on the conveyor, they may be in fact two entirely different plastics with different chemical compositions and attributes. And, when it comes to processing for feedstock, HDPE (#2) and PP (#5) are not compatible.
“So, with our goal to really separate and process efficiently, and increase our revenue by providing processors with recovered and pure PP, we turned to robotics,” Ledieff says.
“We then connected with the grant program at The Recycling Partnership to assist us with this investment. That partnership made the difference and really took us to the level and beyond of our expectations.”

You can't teach humans this trick
“In early 2020 Caglia learned about our grant program for MRFs and polypropylene equipment grants” explains Brittany LaValley, Lead of not-for-profit The Recycling Partnership’s (TRP) Polypropylene Recycling Coalition.
Founded in 2014, she says the funder-based organization is dedicated to the concept of circularity by converting member dollars into supporting grants.
“We turn those revenue funds around into grants that support our mission, which is to mobilize people and data to advance solutions for the residential recycling system.”
LaValley explains how their applications process works.
“For the Polypropylene Recycling Coalition, we have an application process that was previously on a three-month review cycle. But now, we process applications on a rolling basis. When a MRF sends in their application, we follow up to learn more about the facility and its needs. Is it polypropylene sortation equipment upgrades that are needed, or are there other intervention opportunities, be it for other materials or things like contamination?
“We review the applications internally, leveraging the technical expertise of our staff who outline a recommendation on the opportunity. In this case for Caglia, we saw an opportunity for the Polypropylene Recycling Coalition to provide an equipment grant.”
“Once a grant has been approved, we ask grantees to let their feeder communities know they’re accepting PP. This way, residents know what to put into their bins and the MRFs get the benefit of capturing more of the material.”
In Caglia's case, she adds, they were keen to separate polypropylene given the amount of it in the stream and the fact that it’s a valuable material. The trend toward using PP in packaging is growing quickly, given its desirable attributes.
The challenge is that it cannot be separated manually because, as LaValley says, "you can't teach a human to hand pick PP given the variety of formats it comes in.”
So, enter technology of artificial intelligence and robotics to do the job.
Not too many years ago, the concept of artificial intelligence sparked fear that the gate to robots subduing humans was wide open. The futuristic and menacing robot named HAL, the brains of the space mission 2001 in Stanley Kubrick's eponymous film may have been partly to blame. In 1968, however, few viewers knew that HAL was an acronym for Heuristically programmed ALgorithmic computer—clearly not common parlance of the day.
Fifty years later, “algorithm” and “computer” are in our everyday dialogue. It is this intelligence that allows dramatic strides forward from improving medical diagnostics, predicting weather patterns, developing life-saving medicine, and forecasting effects of climate change are but a few of the many unsung heroes of algorithmic computations. Might make HAL think twice again, since he just locked the doors!
“Since Caglia was at the point of doing a complete overhaul of their MRF, it was the right time and place to install robotics. They were amazing partners to work with and our collaboration was showcased during an Open House in September.”
LaValley says that State and local policymakers, along with other stakeholders attended the Caglia Environmental open house and were able to experience firsthand how the equipment works. Moreover, it was a demonstration of successful public private partnerships to achieve optimal efficiency, financial goals and environmental targets.
“Everyone was amazed at this state-of-the-art technology and the streamlined techniques,” LaValley affirms.
She makes one further point. “It's important people know that as the granting source, TRP does not influence the equipment the grantees choose. We give the funds directly to the MRF and then they undertake the due diligence in choosing who and what they want. In this case, the choice of AMP by CARTS was a perfect marriage of technology, personnel and location aligned with the Caglia goals and outcomes.”
LaValley says that the average TRP equipment grant takes 3-4 months from submission of an application to approval, and averages from $200,000 - $400,000.
“There's a lot of amazing work and investment going into supporting the recycling system, but it is often overshadowed by a negative narrative that recycling isn’t working and never will.
“We certainly acknowledge that recycling isn’t a panacea and that there is a place for all three ‘Rs’: reduce, reuse and recycle. Reduction is something I know a lot of companies are working on in order to reduce their footprint and/or to meet goals they may have set. It’s something folks can act on today.
“Reuse, while a needed component of the effort to reduce our burden on the planet, is trickier in that it takes significant behavior change and there is little infrastructure in place to support it. Thus, it’s currently a bit idealistic to just say, ‘get rid of plastic, move to reuse’.
“Recycling infrastructure is already in place and is proven to work, it just needs some investment.”
Artificial intelligence ends the guesswork
“One of our biggest challenges with the growing use of PP is that it has not been a uniform product to identify. As an emerging packaging material, its adoption has really grown, particularly by food producing and delivering arenas. But in recycling, identifying your material properly is essential, and these (PP) are very difficult to distinguish in the lineup,” says Chris Wirth, President, Marketing, and Industry and Government Relations, AMP Robotics.
He relates how in just a few short years the Denver-based company has had record success combining the sophisticated advances in Artificial Intelligence (AI), with the latest designs in robotics, to advance the recycling and related reclamation industries.
“The company was pioneered under the premise that our solutions should be an accessible choice for markets that traditionally would not consider AI or robotics. In developing the AI, which is the brains behind the robotics, we saw an economic opportunity for the recovery and recycling industry to benefit both environmentally and economically.”
But this requires very intelligent robotics to not just pick up and sort items, which is what we typically think robots do: take over the work that a human might perform, and then do it with increased efficiency and speed. Wirth however, is quick to point out that robotics are not, as popularly viewed, “job killers.”
“This is exactly what we don't want people to think. What robotics can do for recycling, especially when equipped with AI, brings the service of modernizing materials recovery in lightning speed. Then, you can use your personnel for more meaningful work,” Wirth adds.
He says the shortage of labor has been crippling to the industry and he recounts that this was a significant factor in furthering Caglia to using robotics.
“They said that they would put out a call for 20 people for their MRF and maybe eight would show up and then half would leave after the first break. Sorting trash is not really a high-attraction opportunity. It’s dirty, and it has safety hazards,” Wirth says.
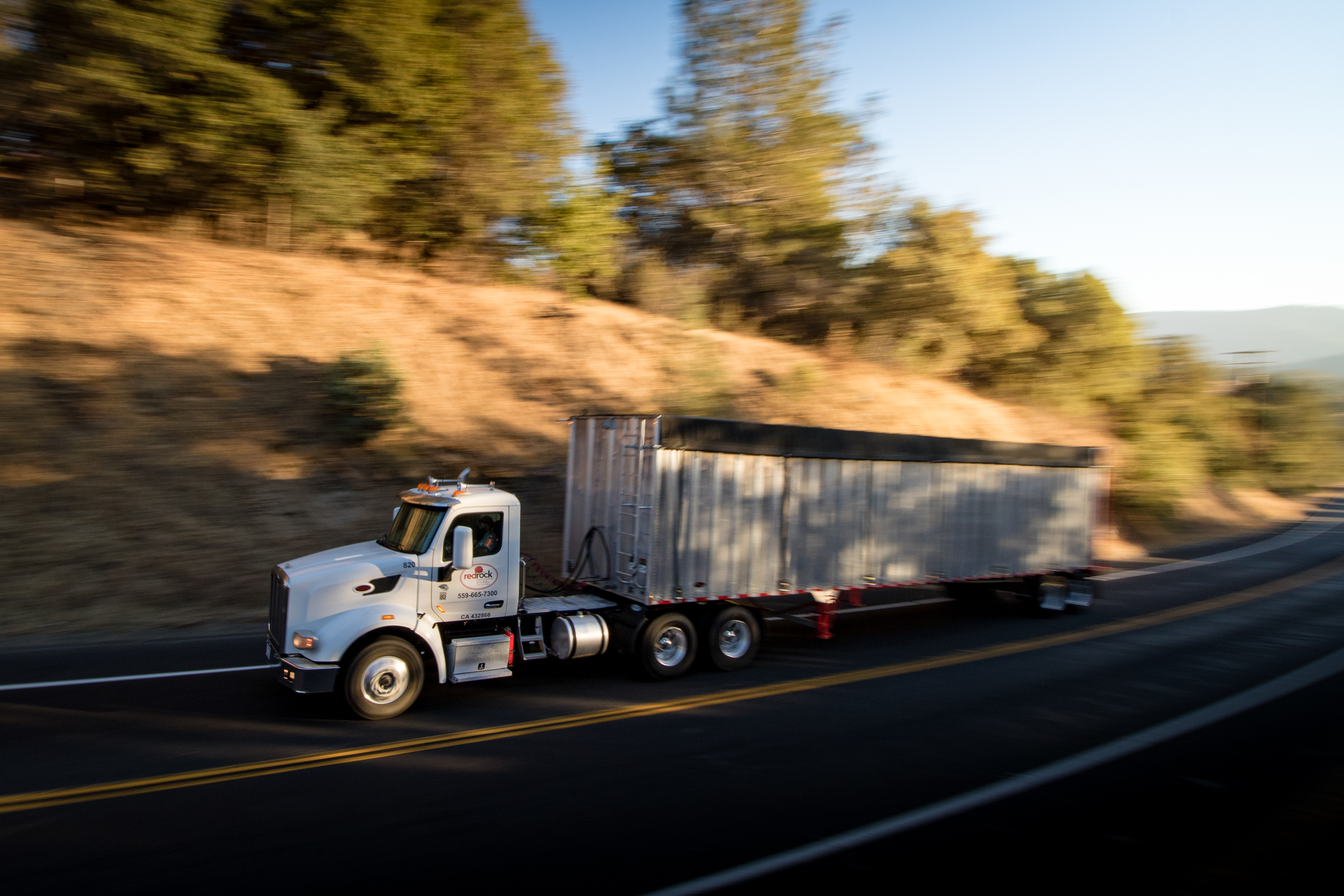
And without people, you can't economically recycle, particularly with the pressures of legislation such as California Senate Bill 343 at your heels, which Wirth adds was another motivating factor for Caglia.
In October, of 2021 California signed Senate Bill 343 into law. Known as Truth in Labeling for Recyclable Materials, the bill prohibits deceptive or misleading recyclability of products or packaging. The law defines how producers shall label their product and has a regulatory agenda for waste processors and recycling facilities to report how materials are collected, what they are, and the recycling process they must follow to be considered “recycled.”
Manufacturers have until January, 2024 to comply with the new mandates on labeling.
So, how exactly does robotics work to make the waste stream an effective processor? Wirth elaborates.
“First, understand that the robot must be fitted with the technology and software that allows its camera eye to pick up all the image-identifying data. Our camera relays the image and through a series of algorithms in the AI brain, it says, ‘okay, I know that it has this form factor, this type of polymer, this level of opacity, texture’ and so forth.
“This vision recognition is captured, calculated, and a decision as to whether the mechanical part should go into action is deployed. Of course, all this happens in milliseconds.”
If the recognition prompts the robot to act, then their machine acts like a miniature vacuum and sucks it up off the conveyor and spits it out with compressed air to a designated location.
Wirth explains further benefits, in that mapping millions of images of all the visual attributes is the power of AI. “First it is computation and visual, then after that it is continuous learning.
“What's really impressive is that our units are connected to a global neural network of AI. We have what’s called AMP clarity real-time recycling data characterization. What this does is once a unit learns this so- and- so- item that looks like this shape and has these attributes is PP, it can then share that knowledge with any AMP in any location.
“So, let's say Starbucks is starting to use PP in its beverage supply in California. After the machine in California learns, identifies, and processes PP, then that information can be shared and learned by a robot in Massachusetts where this trend may be very new to the market. When the PP begins to show up on the conveyor, then the recognition will already be in place.
“Being able to proliferate and get data across one unit to another is the way of the future.”
Moreover, as this type of technology advances, it offers MRFs a more economical and more viable recycling operation. If feedstock purity improves, and feeders are buying, then it is a win for everyone, especially for municipalities, whose recycling programs are still struggling post-covid, Wirth says.
“Incorporating AI, robotics, and connecting MRFs with buyers and offering them a continuous supply of desirable recycled product is guaranteed productivity for everyone.”
Wirth says that the large producers, such as soft drink and food-product producers are also a key link to this success as well.
“If they know that their shift in packaging, which puts billions of pieces of PP out there, will in fact be recaptured, then they know that down the line, a material value will eventually be returned to them in the form of new, good quality recycled feedstock for their products.”
Giving back keeps giving
Rich Caglia has nothing but praise for the partners and people that made their renovation virtually painless.
“The exceptional collaboration we had with Brittany and her team with TRP, Mike and his group from AMP, and everyone here at Caglia goes beyond what we had hoped for to make this happen. As we serve the processors and waste haulers of more than three or four surrounding counties of Fresno, we decided more than a year ago we wanted to be on the leading edge of all aspects of this business. And not only did we invest in equipment, hardware, and software to that end, [we] improved the site for our employees.
“If we expect people to stay in this industry, stay on as employees, we have to offer them more than a paycheck. So, we modernized our facilities, our bathrooms, our eating areas. We created other incentive programs to motivate and encourage retention and loyalty.
“The Caglia family has a long history here and a good reputation. We want to build on that legacy so it continues far into the future, and having and keeping good people is directly related to that success.”
Latest from Waste Today
- Yanmar CE launches full line of compact equipment
- EC Waste acquires fellow Puerto Rican hauling firm
- Goldman Sachs Alternatives to acquire Liquid Environmental Solutions
- Block Island Recycling Management Inc. aims to promote environmental stewardship
- Miami region officials seek WTE plant location
- Clean Harbors faces potential penalty for Ohio fatality
- New Hampshire governor signs leachate management bill
- MSS relocates to new facility in Nashville, Tennessee