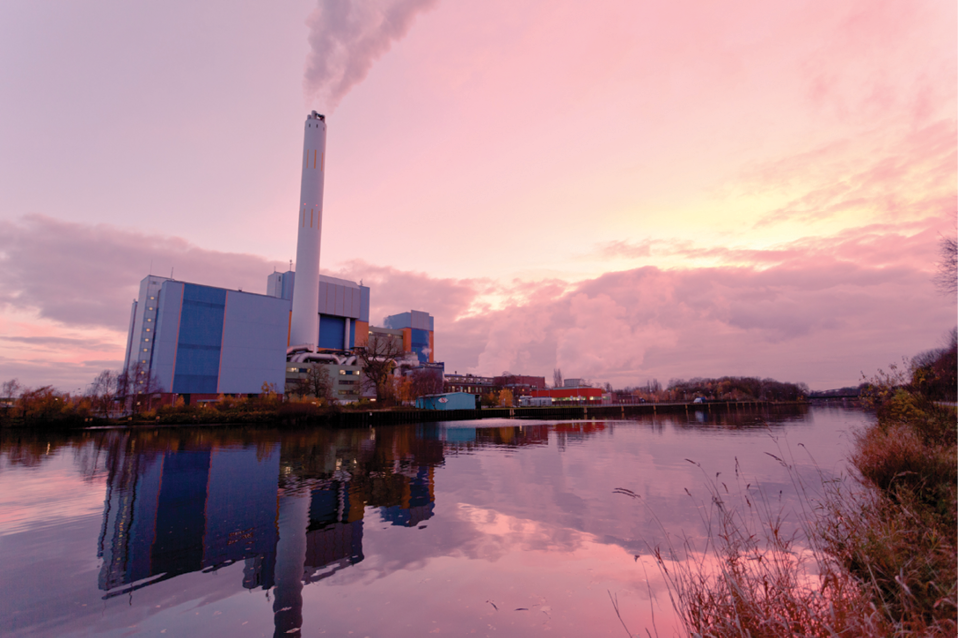
Waste-to-energy (WTE) facilities are a cog in local material disposal systems in the United States. Particularly in areas where landfilling is expensive or politically undesirable, a WTE facility often is a viable endpoint for material that cannot be recycled. In 2018, nearly 12 percent of the municipal solid waste (MSW) produced in the U.S. was sent to WTE facilities, according to the U.S. Energy Information Administration.
As with operating landfills, material recovery facilities (MRFs) and transfer stations, running an efficient WTE facility requires in-depth knowledge.
Neal Bolton, president of Victor, Montana-based Blue Ridge Services Inc., says understanding the flow of material throughout the day is key to running a WTE facility well.
“Generally, what we’ll see in terms of waste flow is a lot of commercial and residential trash in the morning,” he says. “It’s the same on some residential routes. The garbage man starts pretty early in the morning, usually. That type of wet residential [and] commercial trash is more likely to come in during the late morning.”
Often, dryer construction and demolition (C&D) material arrives in the late afternoon or evening as workers end their days.
“The waste-to-energy facilities may be able to take advantage of that to target the types of waste that they prefer to have in there,” Bolton says. “If there’s more trash in a region than the waste-to-energy facility can handle, they may not take everything. If they’re only taking some of it, they will tend to pick and choose what they want to take.”
If they can choose the materials they accept, facilities are at an advantage because they can customize the mix of materials in a way that creates the most efficient recipe for the plant.
“A lot of the wet trash—there’s a lot of BTUs in there,” he says. “It’s just that you use some of those BTUs drying it enough to make it burn. It’s just like building a campfire. You can use wet wood; it just takes a lot of dry wood to get the wet wood going.”
Facility operators must intimately understand the material flow and what mix works best for the plant, and Bolton says they learn to intuitively mix material to achieve optimal results.
Making space
Bolton says WTE plants can process a specific amount of material per hour—whether it’s 30, 40 or 50 tons—but trucks delivering material don’t set their schedules so conveniently.
Incoming material “comes in surges,” he says. “There has to be some storage capacity just to be able to manage the inbound waste and still run it through the system at an optimum rate.”
Bolton says space is needed not only for stockpiling but also for mixing materials.
“You can’t run dry C&D through [the system] at one point and then run a bunch of wet food waste through at another time because it’s not going to be consistent,” he says. “Having enough storage capacity and then the ability to still manage some kind of recipe is important.”

Maintaining flexibility
Another challenge for WTE plant operators is the evolving nature of the waste and recycling business.
If the WTE facility is designed based on a waste characterization, including the amount of paper, cardboard, plastic, glass, organics, metal and other content that ends up at the plant, what happens when the material stream changes?
“Rules change, and so does a lot of recycling,” Bolton says. “A lot of states have mandated recycling, targeting paper and cardboard and organics and brush. And now there’s a big push to target food waste, which is most of your wet trash.”
Some states treat WTE processing as a form of recycling because adding other forms of diversion reduces plants’ ability to produce power, he adds.
“The more recycling programs that are enacted, the less trash there’s going to be, and that’s a concern,” he says. “So, if you’re building a system based on a certain feedstock, what factors can change [volumes of] that feedstock?”
C&D waste, which he says is high in BTUs, falls off during recessions because construction often slows.
WTE plant operators must consider the factors influencing the waste stream when establishing contracts with haulers, municipalities and energy companies.
“It’s a crystal ball thing where you’re putting a lot of money on the table to build a facility like this and [taking] a lot of years to get it designed and permitted and ready to go,” Bolton says. “You want to control those variables to the extent that you can.”
Get curated news on YOUR industry.
Enter your email to receive our newsletters.

Explore the November December 2023 Issue
Check out more from this issue and find your next story to read.
Latest from Waste Today
- McKinsey identifies engineering polymers as a recycling opportunity
- Lindner establishes Brazil subsidiary
- Tennessee thermal dryer facility delayed
- CAA submits amended plan in Colorado
- Tetra Pak finances installation of AI-powered optical sorting technology
- Cullet volume, quality mars flat glass recycling: McKinsey
- Philadelphia waste collectors, city employees, go on strike
- Wall Recycling rebrands to Liberty Waste Solutions