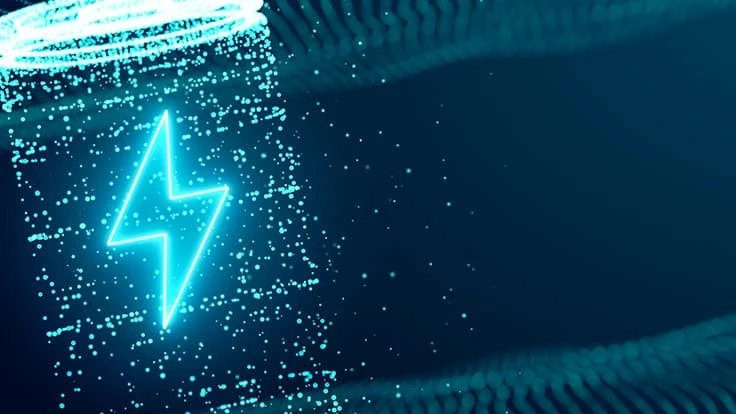
As a result of new advancements in technology and growing demand for electric vehicles, battery power across the world is expected to increase from 184-gigawatt hours (GWh) in 2018 to more than 2,600 GWh by 2030, according to market and consumer researcher Statista.
For recyclers, that means that about 86,000 metric tons of nickel, 35,000 metric tons of cobalt and 125,000 metric tons of lithium carbonate equivalent from used batteries will be recovered for reuse by 2030, according to Statista. While a greater influx of batteries into material recovery facilities (MRFs) across the nation presents an opportunity for these facilities to capitalize on the recyclable material, this also means an increased risk of fire hazards.
As many facility operators have seen firsthand over the years, lithium-ion batteries are perhaps the single biggest threat to MRF operators because of the fires and explosions they can cause if not properly handled.
“Lithium-ion batteries pose a serious threat to both the equipment and people that work in these facilities,” says Michael Timpane, the vice president of Ann Arbor, Michigan-based Resource Recycling Systems (RRS). Timpane has spent three years researching this issue with organizations like the United States Environmental Protection Agency and the Institute of Scrap Recycling Industries.
Due to the risks these batteries pose to operators, experts like Timpane have been searching for new ways to proactively address these issues as demand for batteries increases.
A GROWING CONCERN
While it has not been conclusively studied, experts like Timpane report instances of fires caused by lithium-ion batteries are increasing. According to a survey done by Timpane in conjunction with the EPA, 50 percent of MRF operators believe that fires are increasing at MRFs and 64 percent of operators believe it’s because of the spike in lithium-ion batteries.
A study done by RRS showed that a MRF operated by South Bay Waste Management in Northern California had 5.48 lithium-ion batteries come down the belt every hour, which equates to about 1,000 over five weeks.
Lithium batteries have a chemistry different from other batteries because they have higher energy densities and voltages, can contain a charge in a dead product and their electrolytes are flammable if they come in contact with air, according to the EPA.

This means that any puncture of a battery could cause damage to the safety separator between the cathode and anode, which generates heat and can cause a fire or explosion. Additionally, sorting these batteries is difficult because they are sometimes hard to identify and remove from electronics, says Jordan Riveria and Neal Sushack of the Pipeline and Hazardous Materials Safety Administration (PHMSA), a branch of the Department of Transportation.
“Anything that uses a battery could be considered dangerous,” Timpane says. “Even something as small as a greeting card because they release a thermal reaction if they’re not handled properly.”
A fire or explosion as a result of failing to properly sort or store a lithium-ion battery could lead to catastrophic damage. For example, a fire at one of South Bay Waste Management’s MRFs that was believed to be started by a battery cost the company about $8.5 million in damage. This type of widespread damage is, unfortunately, all too common for recycling organizations.
ADDRESSING THE HAZARD

While the dangers of fires caused by lithium-ion batteries are growing in severity, Timpane says several things can be done to proactively stop a fire from happening. This includes improved signage, deployment of technology, and improved training and education.
“Before electronics even make it to the waste stream, they could have clear labels on them warning consumers not to put it in recycling containers,” Timpane says. “I know original equipment manufacturers could improve the labeling of these devices and be more consistent. This could prevent a substantial amount of these batteries from making it into waste streams.”
While some manufacturers have begun labeling what devices can and cannot be recycled, most still do not. This means MRF operators need to increase training and education for their workers so they are aware of what to look for when analyzing incoming materials. Timpane says things like repeatable toolbox training sessions that focus on identification, fire response and hauling should all be covered frequently in sessions. Also, he suggests training drivers to lookout for batteries when on collection routes to prevent batteries from making it to the MRF.
Timpane says that operators should also put their workers through battery count training. This is when the operator places scrap either on the floor or a belt that’s been stopped so that the workers can sift through to find all the batteries in the mix. The goal is to increase a worker’s awareness about what kind of material could have a lithium-ion battery in it.
“Practice makes perfect,” Timpane says. “You can do it on the floor or on a belt, but if you get your employees involved, chances are they will pay attention.”
Other things that an operator can do to improve the safety of a facility include routine checkups of the facility’s security system at night as well as making sure the sprinkler system has been inspected by the local fire department, Timpane adds.
Technology is also playing a larger role in preventing fires at MRFs. Timpane says companies can invest in artificial intelligence that can alert employees when a lithium-ion battery has been detected. He also notes that there are various webinars and podcasts that can be used as training tools for workers.
“The EPA holds frequent webinars about this,” Timpane says. “I believe artificial intelligence is going to play an important role in MRF technology and safety.”
OUTSIDE HELP

While there are plenty of preventive measures a MRF operator can take to increase site safety, the most important thing in preventing fires is educating the community, says Brandon Wright, the communications director of the National Waste and Recycling Association.
“Everyone wants to recycle,” Wright says. “People want to do the right thing, even if they’re not sure if the object can be recycled or not. So, they throw it in the bin anyway and hope that someone else down the line will sort it out.”
Educating the community on what can and can’t be recycled often eliminates fire hazards before it is possible for an issue to arise. This can be done through improved pamphlets, posters and some boots-on-the-ground initiatives. Some communities, like Akron, Ohio, have launched programs to examine residents’ recycling carts, and if there is contamination like plastic bags or lithium-ion batteries, a note is left informing the resident why the container cannot be collected.
However, while experts agree that cart contamination assessments and tagging programs are some of the most effective ways of preventing fires at MRFs, it takes a constant effort. This is because residents frequently come and go from the community, which means how an area recycles constantly changes.
“I really do believe that community engagement helps prevent hazardous items like lithium-ion batteries from entering the waste stream,” Timpane says. “Improving the education of the community can increase its acceptance of better recycling methods. However, you can never let your foot off the gas pedal. If you do, that could lead to an increase in hazards found down the line.”
This article originally appeared in the Sept. issue of Waste Today. The author is a digital editor for the Recycling Today Media Group and can be reached at akamczyc@gie.net.
Latest from Waste Today
- New Hampshire House committee advances amended landfill moratorium bill
- Viably teams with Turmec on materials processing systems
- Untha shredder prepares SRF in the UK
- Anaergia to upgrade anaerobic digestion facility at UC Davis
- Dynamic Renewables, BC Organics, National Organics combine to form Sagepoint Energy
- Wastequip appoints CFO
- SWACO grants target landfill diversion
- Doppstadt says new trommel offers optimized flexibility