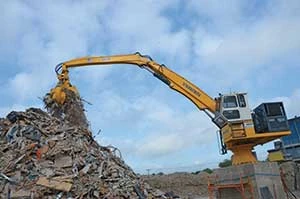
Once municipal solid waste (MSW) and construction and demolition debris (CDD) show up at a materials recovery facility (MRF) or transfer station, there is a need for further handling of the resultant material stockpiles. That need is met by material handling machines, known as grapples, that pick up and lift the waste materials, and by conveyor belts that carry the waste through the facility. Because of their inherent high production capacities, this equipment is usually found at larger facilities with high waste throughput rates (less productive facilities can make do with smaller pieces of equipment like front-end loaders). What are the capabilities of this equipment? What does this equipment do? How do they work together and as part of the whole waste management process? How are they used to deal with construction and demolition (C&D) waste? What are the differences and appropriate applications for mobile versus fixed equipment? But first, we should examine what kind of material this equipment manages.
Characteristics of MSW and CDD
MSW is a very heterogeneous material, consisting of components varying greatly in size, shape, color, density, moisture content, combustibility, biological degradation, and ferromagnetism.
CDD is the other primary wastestream handled by MRFs. CDD is the waste or leftover material resulting from the construction or demolition of buildings, utilities, and structures.
CDD includes wood, glass, plaster, metals, wire, conduits, I-beams, rebar, asphalt, bricks, blocks, and concrete. CDD is recovered and recycled by source separation or commingled recycling.
The Big Picture—Grapples, Conveyors, and Waste Processing Systems
Before we look at grapple and conveyor operations, it is best to look at the environment they will be working in. Waste separation in a MRF is a multi-stage process, with a different type of waste being removed at each stage by a uniquely designed piece of equipment. First, the metals are removed. Ferrous metals are removed by fixed magnets or electromagnets either configured as part of the conveyor belt or set over the belt to pull out ferrous metals as they pass below on the conveyor belt. Nonferrous metals are extracted with eddy current separators. These are rapidly spinning magnets that induce an electric current within the metal object, which in turn generates its own magnetic field in opposition to the applied magnetic field. Since the electric fields repel each other, the nonferrous metal objects literally jump from the moving belt into an adjacent storage receptacle.
Organics (food waste, yard waste, green waste, fall leaves, etc.) can be removed via hydro-pulping. A simple and direct method, it utilizes high-velocity water jets to smash and pulp the organic waste into a slurry which is carried away by a water stream to an anaerobic digester to produce biogas for fuel. Other organics (office paper, newsprint, old corrugated cardboard, magazines, etc.) are removed mechanically. Cardboard and boxes are removed with disc screeners. These are bed floors equipped with rotating discs of various sizes and shapes (depending on the material being processed) whose movement creates a wave-like motion that carries large and light objects to the top for easy removal. The smaller, lighter paper is removed with air clarifiers. These are structures resembling chimneystacks equipped with blowers that pull small, light waste objects such as paper and newsprint up out of the main wastestream. A refinement of this approach is air blades, sheets of high-pressure airflow arranged in parallel. The differing airspeeds of each “blade” allow for further separation of different grades of paper, magazine stock, and newsprint.
Some waste is separated by color. Multi-colored waste objects (plastics and glass of all types) can be removed by color separators utilizing LSP technology. LSP meters read the wavelength of the light reflecting off of the glass or plastic object. The reading then instructs a series of high-pressure air blows to push the object at the right time into the appropriate storage bin. As a further refinement, LSP meters using infrared can determine the density of the plastic and sort it out by type.
Grapples are there at the beginning and there at the end. Once the waste is dumped onto the tipping floor, large quantities of waste can be grabbed by grapples and directly deposited on the starting end of the belt operation or into a hopper that feeds the conveyor belt. Grapples equipped with their own magnets can remove steel and other ferrous metals initially without the need of a subsequent magnetic separator. This operation is far more efficient for large waste quantities and high throughput rates than the more traditional front-end loader. At the end of the operation when waste has been separated into its various components and stored in a receptacle, grapples can be used to offload this mini-stockpile either by reaching into the storage hopper directly or by lifting and moving the hoppers themselves when they are full.
Conveyors are everywhere in between. They are installed as a veritable highway of moving heavy-duty industrial grade belts connecting the processing equipment. These belts are loaded with waste and then carry the waste to and through each removal station. At the start of the process, hooks and blades slice open and remove trash bags, spilling their contents onto the belt. The adjusted speed of the belt ensures a more or less even distribution of the waste as the belt moves to the first removal station. Branching belts can take waste to several different locations for processing in parallel, or remain in single file for processing in series.
Grapple Types, Operations, and Applications
A grapple (often referred to as a “clamshell”) is a mechanical tool with two to eight jaws (or tines) arranged in a pattern around a central arm joint connection or suspended from a cable. It is used to pick up objects or clumps of material. The entire assembly can be mounted on a tractor tread vehicle, wheeled vehicle, excavator, or backhoe. This configuration allows for mobility across the work area. The arm used to maneuver the grapple can be extended, retracted, swung side-to-side, elevated, or lowered as needed to grab material and maneuver through the workspace. Grapples can also be mounted at fixed locations with the control arm set securely into a foundation and often controlled remotely. Lastly, a grapple can be suspended from the framework of a facility’s roof structure. Running along tracks, the grapple can be positioned and lowered as needed to retrieve and deposit materials.
There are several different types of grapples for different operational situations and work environments. In addition to the clamshell bucket used for soil or sand, there are those grapples designed for waste recycling and demolition debris management. Solid waste grapples are designed to handle the heterogeneous and varying materials that make up municipal solid waste, from loose trash to large white goods. Demolition and sorting grapples are heavy-duty units used for recycling of non-concrete CDD materials (the concrete is usually managed by the specialized equipment used to reduce the size of concrete chunks). Designed to handle bulky loads, they are capable of exerting great force on the grabbed material.
Lastly, there is a category of grapples referred to as “orange peel grapples” with the tines resembling the sliced peel of an orange (with four, five, or six tines). This design and the powerful hydraulic cylinders powering them allow an operator to penetrate deep into waste piles and securely grab the maximum amount of material possible. These two attributes result in very high production rates. Orange peel grapples can also come equipped with electromagnets. This allows the grapple to effectively manage scrap ferrous metals.
Conveyor Types, Operations, and Applications
A conveyor belt is such a common thing, from grocery checkouts to heavy industry, that we tend to forget that there is a wide variety of such belts. These include various types of configurations (chained edge, troughed rollers and trough slide beds, flat sliders, and slide beds), materials (rubber, PVC, polyurethane, neoprene, nylon, nitrile, polyester, and leather), and applications (manufacturing, debris waste management, food production, shipping and packaging, aggregate and building materials, etc.). Conveyor belts come in various sizes, widths, lengths, and shapes. In general, the harsher the working conditions, the more rugged and durable the belt has to be.
One such rugged application is the handling of bulk quantities of waste. Chain belt/edge conveyors are designed to carry high volumes of materials, such as incoming flows of solid waste. The waste contains large quantities of sharp objects, so any conveyor belt used in this application has to be cut- and abrasion-resistant. In addition to carrying waste, these belts are used in conjunction with MRF workstations and separation equipment for waste sorting and removal. These tend to carry lighter loads, up to a ton per hour.
The next step up in durability is steel belt conveyors. These come in two configurations: piano hinge and overlapping steel aprons. Less used in MRFs where they would interfere with magnetic separation of ferrous metals, these are more suitable to CDD processing operations. Steel belt conveyors can carry large weight loads (with 20 to 50 tons per hour throughput rates). They can manage bulk loads of brickwork and crush concrete and steel rebar. In between steel belt and chain belt with a capacity of 1 to 15 tons per hours are slider beds conveyor belts. This intermediate range allows for greater operational flexibility with slow to fast operations.
MRFs usually make use of all three types depending on which part of the wastestream is being handled. They utilize inclined installations to allow the easy transfer of materials from one elevation to another. Segregated waste can be easily moved by conveyor belt to different parts of the recycling process, or into larger hoppers for storage and stockpiling. Controlling the speed of the belt controls the speed of the overall recycling process, even allowing for reversal of direction if needed. They act as bridges, connecting loading and offloading points with the various removal and collection nodes in the MRF recycling process.
Major Suppliers
Builtrite Manufacturing provides a wide range of grapples for multiple applications. At the small end is the Builtrite Model 40-SE Stationary Electric Material Handler, designed primarily for loading smaller balers (nonferrous, paper, cardboard, etc.) or in pulp or other types of wood mills, for unclogging conveyors. The material handler boom is a compact 18.5 feet in length, allowing for operation in tight, confined spaces. The mid-range Builtrite Model 40-SE Material Handler is designed to be reconfigured to meet different application needs. Its customizable platform includes both a remote operator’s station with its own remote power unit or a directly operated sit-down operator’s platform. The heavy-duty Builtrite Model 1010-SE is designed for a variety of applications (loading conveyors, balers, shredders, nonferrous scrap handling, lower volume scrap applications, log handling, foundry use, etc.). Its seven different boom configurations can reach as far as 25.5 feet and it also comes with either a remote operator’s station or a direct sit-down operator controls.
Continental Biomass Industries manufactures a complete line of equipment designed specifically for the recycling and reduction of MSW, including portable and stationary shredders and grinders, screening and sorting equipment, and conveyor belts. Their 16-feet-by-60-inch-wide feed conveyor is constructed of durable Hardox AR450 plate and is designed with a fluted (funneling) high trough. This design configuration aids with the continuous feed of CDD and green waste into their Hog chipper champers. The conveyor belt has an extra-large flow through capacity which simplifies the feeding of large volume material surges or large dimensioned and bulky individual objects (trees, logs, telephone poles, stumps, or railroad ties). The entire feed system is radio-controlled and load-regulated. Similarly, their discharge conveyor is also 60 inches wide and features a 220, 2-ply cleated belt, providing system performance at maximum efficiency.
Emerald Equipment Systems provides tracked stockpiling conveyors for operations at mobile crushing and screening plants. These mobile conveyors allow for flexible operations that minimize the need for wheel loaders to move materials and manage stockpiles. Their Telestack units operate at rates of 100 to 1,500 tons per hour and can handle materials as large as 12 inches while reducing dust and emissions. With discharge heights as high as 40 feet, they can manage stockpiles as large as 3,210 cubic yards or 4,330 tons. Their Masaba telescopic conveyors can be used in multiple applications such as quarry, organic, and port loading.
Genesis Attachments has developed its Jaw Armor protective system available for severe-duty contractor grapples. This is a weld-on modular system constructed of abrasion-resistant, proprietary GenGuard steel that maintains structural integrity and virtually eliminates the need for buildup and hard-surfacing of the protected wear areas. Jaw Armor kits are available for new and existing Genesis contractor grapples. In addition to this development, Genesis has added two sizes to its GSG Scrap Grapple line, for a total of six models in this product line. These orange-peel type scrap grapples are available in 2.0 cubic yard and 2.5 cubic yard sizes in addition to the original 0.75 cubic yard to 1.5 cubic yard models. The grapples come with protective hardened steel bearings with dust seals at all pivot points to keep out contaminants, a heavy-duty cylinder guarding system that protects the cylinders and internal components, reverse-mounted cylinders that protect rods from damage, and large-bore hydraulic cylinders to maximize clamping force.
Doosan Infracore North America manufactures wheel loaders for use at solid waste facilities and scrap recycling centers. When solid waste facilities use a wheel loader and a grapple attachment, the operator loading a conveyor may feather the material, so it doesn’t just get dumped in. The wheel loader operator opens the grapple tines to allow some material to fall out, then opens them a little further so more material can fall out. This process allows the wheel loader operator to efficiently meter the material flow into the hopper. Typically, in the scrap and recycling industry, companies choose a grapple with an open-bottom design that won’t hold dirt and debris and allow it to fall through the grapple tines. At solid waste transfer stations, a wheel loader may be paired with a bucket with a smooth edge to scrape up and get everything cleaned from the surface. The grapple helps operators retain the material while the bucket collects it. A thumb wheel on the wheel loader joystick controls the opening and closing of the grapple tines. Doosan wheel loaders are designed with a thumb wheel that has proportional control, which means the operator can vary the hydraulic oil flow to the cylinder.
Adolfo Sandoval is the vice president of operations for SCOR Industries, a Southern California construction and demolition recycling company that uses wheel loaders and grapples to manage waste. “We try to recover as much of the waste as we can,” says Sandoval. “As a result of the comprehensive services we offer, our company works on some of the largest, highest-profile building projects in Southern California. Our customers like the unique way we manage job site waste and the recycling rates we can achieve.” At its facility, once the rolloff containers are dumped, a pair of Doosan wheel loaders with buckets and grapples efficiently handle the waste material, including loading wood into grinders for making nursery products and putting metal into shredders.
Revolution Recovery is a construction and demolition recycling firm based in Philadelphia, PA, with three locations. The company’s mission is to keep recyclable materials out of sanitary landfills. They take in materials from construction sites, both new and renovation, as well as demolition and manufacturing sites. On average, the company takes in about 450 tons of material a day at its Philadelphia and New Castle, DE, locations. In order to keep their operation running smoothly, the company relies on wheel loaders with grapples. New Castle Plant Manager Nick Grovola says his location uses wheel loaders with grapples to meter the material for the appropriate flow on conveyors, as well as pushing material and loading the fine screens, wood chips, and crushed concrete. Grovola estimates that the company can recycle up to 75% of the material delivered to its facilities, helping reduce the amount of waste that is sent to sanitary landfills.
Excel Manufacturing provides rubber belt and steel belt conveyors for both aboveground and in-ground applications. Their conveyor systems are engineered to work in tandem with their balers for seamless conveyor to baler integration. The engineered system approach is designed to ensure that the conveyor and baler systems are pre-wired with all contactors, electronics, and conduits. The whole package approach eliminates hidden additional costs normally associated with including hinged and removable pit plates. To properly integrate with their baler machines, the conveyor belts come with high side walls for material containment. Ease of maintenance is provided by a self-cleaning under-belt system, axial flow wing pulleys, and full flashing protection belt, and cleaning is minimized with standard installation kits including painted pit plates, anchor bolts, and miscellaneous hardware.
Sierra International Machinery is a source of a diversified product line of material handlers. Their 29-ton T510 is equipped with a 33.5-foot boom and is designed for use at the scrap yard, MRF, or CDD facilities. Operator comfort is provided by a 17-foot-high cab with heating and cooling, ergonomic controls, and soundproof design. The 22-ton T409 is available in either electric or diesel and features a two-piece boom with a 32-foot reach with the grapple on a rotator. It comes with a front heavy-duty blade, two rear stabilizers, and puncture-proof solid rubber tires and is powered by a 145 hp Cummins four-cylinder turbo diesel engine. Their 17-ton T308 material handler is equipped with a two-piece boom with a 27-foot reach with a grapple on the rotator.
Latest from Waste Today
- Nexus W2V breaks ground on Indiana bioenergy complex
- CP Group announces new senior vice president
- Michigan governor proposes raising tipping fees to curb out-of-state waste
- Circular Services breaks ground on north Texas MRF
- Alberta, Canada, looks to encourage growth of biodigester, biogas industries
- SoCalGas signs RNG procurement contract
- Heritage Environmental Services rebrands
- Interstate Waste Services acquires Pinto Service