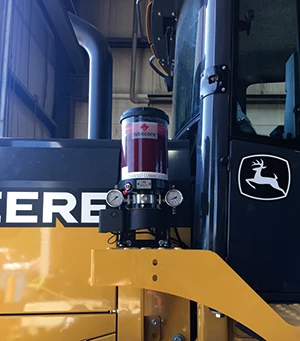
Because time is money and downtime is lost revenue, solid waste operations do well by operating to the maximum efficiency as is possible.
“Downtime, especially when it’s unexpected downtime, is a big problem,” says Rob Profilet, product application specialist for Shell Tellus.
It’s a tough environment out there for solid waste vehicles and landfill equipment.
Tim Russell, marketing manager for Shell Lubricants, points out that solid waste vehicles operate in a rugged environment that entails a lot of idling and hydraulics working to collect the trash from the street to deposit in the truck. “Think of how many times they’re cycled through every day,” he notes.
“Equipment is often neglected when it comes to consistent lubrication due to harsh operating conditions, unfriendly manual greasing situations, or even availability of greasing equipment,” says Jan Eisses, president of Lubecore.
“Dirt gets pulled past the cylinder wipers, seals, and packing on compaction cylinders and the contaminants naturally end up in the oil, the filter, the reservoir, and all components of the system,” says Curtis Dorwart, Mack refuse product manager. “That’s why it is important to have quality cylinders and to maintain the system to keep contaminants away from the chrome parts as much as possible.”
In addressing the relationship between the role of fluids in maintenance and the conditions to which collection trucks are subjected, Dorwart offers several factors for consideration.
“Oils lubricate, cool, absorb shock, and transmit motion in a hydraulic system,” he says. “They are key to having the system work as reliably and efficiently as possible. The wrong oil can damage components like hydraulic pumps if too high a viscosity oil is used in severely cold climates, as an example.
“High ambient temperatures and severe duty cycles that push oil to overheat can shorten oil life, especially mineral-based oils over synthetics. The dirtier the application, the more opportunity to ingest contaminants—even through the reservoir breather, which sometimes gets overlooked.”
Hydraulic systems are one of the most important factors in solid waste vehicles, Profilet points out.
“If the hydraulic system isn’t operating correctly, they’re not going to be able to be as efficient and productive,” he says. “It comes down to how much work could they do over time if the hydraulic system isn’t operating efficiently.”
Contamination is one of the major concerns regarding the ability of hydraulic systems to function effectively, says Profilet.
“If you have water contamination in a system, that’s not good for the system in that it can interfere with the lubrication and lead to situations of rust and corrosion down the road on critical components of the system,” he adds.
“Since water speeds up oxidation, that means the oil might deteriorate a little faster over time, so you may have to change the oil more often and across the wide fleet of trucks, that would add up to some costs over time across all of those vehicles.”
Profilet notes that in most hydraulic systems—be they mobile or stationary—today’s hydraulic oils are “carefully formulated and designed to protect equipment well and last a long time. Once you put them out in tough environments, there are a lot of challenges with heat or contamination. That’s when the challenge really comes in—can the oil still operate effectively under those types of conditions?
“Having the right lubricant, doing the right maintenance, taking care of the oil, trending the data, understanding the data, and using that to make decisions to help optimize your efficiency is all going to help your total cost of ownership, manage those costs, and make the company as profitable as you can.”
Through its Tellus brand, Shell offers a number of different hydraulic fluids, including mono-grade and multi-grade hydraulic oils. Multi-grade hydraulic oils have a higher viscosity index and are designed for use in a wider range of temperatures, “or you have a wider temperature operating window that you can use those in—sometimes in outdoor equipment—and so a higher viscosity index fluid is good,” says Profilet.
“We also classify our fluids based on being synthetic- versus mineral-based. Synthetic fluids offer some advantages in terms of their longevity because they have a better oxidation life,” he adds. “They’re a naturally higher viscosity index and cover a wider temperature operating range.”
Dorwart notes that the power steering system is the most important hydraulic system on a truck.
“They are well-engineered and offer very little trouble over the life cycle of the truck as long as the oil is of the proper viscosity and type and the filter and oil level are checked and maintained on a regular basis,” he adds.
Additionally, the compaction system has to work equally as well “or you won’t be generating any revenue with your truck, so the same goes for the body hydraulics,” he adds. “The body hydraulics are far more complicated and since there are more hoses and connections as well as complicated valving, there are more leak points and opportunities for hose chafing.”
Jim Salmon, a technical manager for the D-A Lubricant Company, says at a landfill and on solid waste trucks, each hydraulic system is equally concerning given the rugged environment in which they operate.
“All lubricant companies, including ours, offer a wide variety of viscosity ranges to compensate for environmental temperatures, ambient temperatures, and operating temperatures, and the different fluctuations depending on what area they work in and what kind of machine it is,” notes Salmon.
“Refuse trucks operate in some applications that are very demanding not only on the chassis and brakes but especially the transmission and the hydraulics where it works off and on, off and on,” he adds.
D-A Lubricant offers a line of products and viscosity grades designed to meet the needs of everything from stationary landfill gas engines to solid waste collection vehicles—and of particular note is the company’s CK-4 line of oils.
For hydraulic needs, D-A Lubricant offers a range of anti-wear hydraulic oils as well as a full line of greases that can work in severe, wet, and high-temperature conditions and a line of coolants.
Lubecore’s automated lubrication systems are implemented in many areas in solid waste management. Single-line, multi-line, and progressive systems are used to deliver fluid greases or solid grease to greasable components.
Lubecore’s automated lubrication systems are applied on on-road equipment such as truck chassis, transfer trailers, automated side-loading arms, front-end loaders, and rear loaders as well as off-road equipment like compactors, wheel loaders, and excavators on landfill sites.
Automated lubrication systems consistently deliver small amounts of grease on a regular schedule to greasable points on the equipment and are designed to reduce risk and labor costs and help with logistics and reduce wear, notes Eisses.
On MRF equipment such as conveyors, balers, and compactors, there are additional benefits of significant noise reduction and energy savings.
Maintenance plays a key role in keeping equipment running, reducing downtime, and keeping employees safe, notes Eisses.
“The functionality and longevity of a machine and its components are highly reliant on the operator in a manual greasing situation,” adds Eisses.
“A lubricant’s properties are dependent on several variables in any operational situation. Extreme heat, dirt, water, and time can separate ingredients such as soap from oil in a grease compound. This can be observed on most equipment that is greased by seeing wet patches of dirt surrounding grease Zerks.”
Oil analysis is the key to a successful maintenance program, says Salmon.
“The only way you can get a good look inside that engine is to go inside that compartment and grab the oil sample on a regular basis,” he says. “Vocational trucks work harder than an over-the-road truck would do on a daily basis, so maintenance schedules would be shorter. You could use the results from the oil analysis to decide whether or not you need to extend or shorten the maintenance schedule, depending on what the OEM recommends.”
In advising MSW operation managers what to look for in oil analysis, Profilet says that “like any hydraulic oil, regular maintenance and regular oil analysis is critical because you can trend the data over time. We always recommend to trend for some of the basic things like water content and viscosity—even the general appearance of the oil can tell you if something may be wrong with the oil.”
Oil that looks too dark or smells “funny” may indicate oxidation or degradation.
“Look for the acid number to see if the oil is becoming degraded,” says Profilet. “Also look for contamination. That can be done by looking at the elements that are in the oil. An ICP measurement detects all of the different types of elements and can give you a quick check of the additive content. It can also tell you if you have any foreign material such as dirt in the oil.”
Russell notes that most trucks in the solid waste application change oil based on hours, not miles.
“The maintenance intervals are set related not to hydraulics, but hydraulics along with engine and transmission and they set up all of their A/B schedules with to coincide,” he says.
“If one fluid has an issue, now you’ve basically impacted that whole schedule to some degree,” adds Profilet.
With the advent of data collection and analysis comes new maintenance methods.
“Oil analysis has been around for years and it’s a great tool to help potentially predict failure and prevent costly downtime as well as a tool to extend the useful drain life of your oil,” says Dorwart. “Analysis is quite sophisticated today and can detect the type of contaminants and likely origin well in advance of the technology of just a few years ago.”
Profilet says more MSW operators are becoming “much more tuned in” with respect to oil analysis.
“The nice thing about collecting data is optimizing the way you use the data,” he says. “With a large fleet of trucks, you could actually look at that data across the fleet or by location even and you could determine if there are specific trends that are going in one location versus another.
“If one location is having specific issues, they might be able to question another location perhaps served under another maintenance shop to find out what they are doing to prevent the issue from occurring? It can open up end-users’ eyes a little bit to look across their system versus focusing on a problem with an individual truck.”
For instance, a problem may exist at one location because of a weather-related issue.
“You can trend the data across the whole fleet and then segment it in a way that makes sense,” says Profilet.
“Cool, clean, and dry” are the operative words in fluid maintenance, notes Profilet.
“If you can keep any lubricant cool, clean, and dry through its application life, that’s going to help the equipment, help the oil life, and help maximum productivity,” he adds.
Latest from Waste Today
- Enviri posts Q4 and full year 2024 loss
- Miami-Dade still grappling with MSW options
- Oregon approves EPR Program Plan
- J.F. Lehman & Co. acquires Atomic Transport LLC
- Mazza Recycling adds to transfer station operations
- Michigan awards $5.6M in recycling, waste reduction grants
- Republic acquires Shamrock Environmental
- Russelectric spotlights paralleling systems for water, wastewater treatment facilities