
Friedman Recycling has been in the industrial, commercial and institutional (IC&I) recycling business since its beginnings, says Morris Friedman, who owns the Phoenix-based recycling firm with his brother David Friedman.
Their father, Abe Friedman, started out in the recycling business by sorting metals by hand in the late 1940s and early 1950s in Ohio. When Morris and David started helping their dad with the business, they adopted this same hand-sorting method.
“We grew up sorting material from the ground,” Morris says, adding, “When you’re [hand sorting], you have clients sort as much as possible.”
When Abe developed asthma in 1974, his doctor suggested he move from Ohio, where seasons and weather are constantly changing, to a destination where the air is clean, dry and constant—perhaps a desert state such as Arizona.
“He packed us up, drove [us] across the country, and [we] showed up in Arizona,” Morris recalls. “He wanted to get back into recycling, but my mom didn’t want him to go back to scrap metal because of his health.”
Morris says his father had just started to handle small amounts of newspaper and cardboard before the move, “so he decided to focus on that.”
Humble beginnings
In the early ’80s, Abe received a call from Honeywell, a client at the time, asking if Friedman Recycling could shred documents. Rather than say no, Morris says, Abe bought a shredder and added document destruction to Friedman Recycling’s list of capabilities.

When Morris and David became involved in the company, paper and cardboard were the focus because the lack of mechanical sorting technology made sorting through commingled loads too difficult. But as technology advanced in the late ’90s and early 2000s, Friedman Recycling broadened its scope, adding processing of commingled residential material and of mixed office paper loads and mixed container loads from the company’s IC&I clients.
“Our business is set to be a one-stop vendor for our clients,” Morris says. “We don’t run or own transfer stations and landfills, but we do haul to third-party landfills and transfer stations.”
Friedman has locations in Phoenix; Tucson, Arizona; El Paso, Texas; and Albuquerque and Los Cruces, New Mexico. The Los Cruces location deals with the company’s curbside recycling stream, where materials are transferred to its El Paso material recovery facility (MRF).
The Tucson and Phoenix MRFs are strictly for the company’s IC&I materials, while the El Paso and Albuquerque MRFs were built in response to requests for proposals for residential MRFs. These two MRFs also can process commercially generated material if necessary.
“We also handle plastics and scrap metal, but we don’t process the metals,” Morris says. “We’re thinking of taking it to the next level and shredding plastics, but the market hasn’t been great.”
Going through the motions
Eugene, Oregon-based Bulk Handling Systems (BHS) supplied the system for Friedman Recycling’s residential MRFs.

Van Dyk Recycling Solutions, Stamford, Connecticut, provided systems from Bollegraaf, Appingedam, The Netherlands, for the Phoenix and Tuscon facilities to process commercial materials.
“Unlike a residential system where we’re about to secure a contract with a municipality that guarantees materials, commercial [material] is added over time,” David says. “Our systems are supplemented, redesigned and upgraded over time—there are newer components with older ones.”
The Phoenix system has three different entry points for materials at various stages of processing.
The system includes OCC (old corrugated containers), fines and fiber screens, as well as optical units that are used to separate plastics and fiber. Magnets pull out ferrous metals, while eddy current separators remove nonferrous metals.
“Unlike a residential stream, the material is very diverse and much more complex and difficult to handle efficiently,” David says.
Both manual and mechanical sorters separate materials to get the streams “as clean as we can,” Morris says. This includes removing wood, large pieces of plastic and any other items that may damage equipment or clog screens.
The incoming fiber is sorted according to the Institute of Scrap Recycling Industries (ISRI) Paper Stock Industries (PSI) Chapter specifications before being baled and transported to consumers of these materials.

The team at Friedman Recycling also spends time on quality control, which includes training employees on the manual sorting line and breaking open finished bales to check their contents, ensuring a clean, up-to-spec batch.
“Our end goal is to provide a great raw material to paper mills we’re supplying,” Morris says. “And our goal in the industry is to divert the material from landfill.”
With the largest amount of commercial material—350 to 400 tons per day—being processed at its Phoenix plant, Friedman Recycling supplies its sorted fiber to paper mills that are located throughout the U.S. and globally.
Morris says Friedman Recycling sells paper to domestic mills and mills in China and Mexico. “We spend a lot of time traveling to make sure we’re meeting their needs,” he adds.
Small differences
While the sorting and processing systems are not much different between the residential and commercial lines at Friedman Recycling’s MRFs, the difference in volumes between the two service areas are beginning to show, with IC&I streams declining per customer, the brothers say.
“Unlike a residential system where we’re about to secure a contract with a municipality that guarantees materials, commercial [material] is added over time. Our systems are supplemented, redesigned and upgraded over time—there are newer components with older ones.” – David Friedman, Friedman Recycling
“On the residential side, we are in 15 to 20 year contracts, and we know it will be difficult to lose our clients,” Morris says. “With commercial, it’s a little more difficult [to keep volumes up].”
The volumes are “off,” for Friedman Recycling’s IC&I sector, he says. The reasons behind the reduction in volume vary by client and can include conscious efforts among generators to reduce waste and recycling generation; competition for material from other service providers, such as larger, integrated waste and recycling companies, in the areas the company serves; and municipalities that enter into contracts to handle all of the materials generated in the area.
Other factors also can be at play, David says. “Some large manufacturers have outsourced and moved out of the area, so we’re just dealing with distribution. Others are creating streams with lighter and lighter materials,” he says. “Our clients are also just getting a lot smarter about the manufacturing of their waste and generating less.”
Commingling of materials and a lack of regulation prioritizing recycling in the states Friedman Recycling operates in are holding the company back, Morris says. He adds that Friedman Recycling always is looking toward the future and keeping its finger on generation trends affecting the industry.
“We’re keeping an eye on trends, seeing if competitors are trying something new,” he says. “We stay up to date with PSI specifications and are changing as the waste stream changes.”
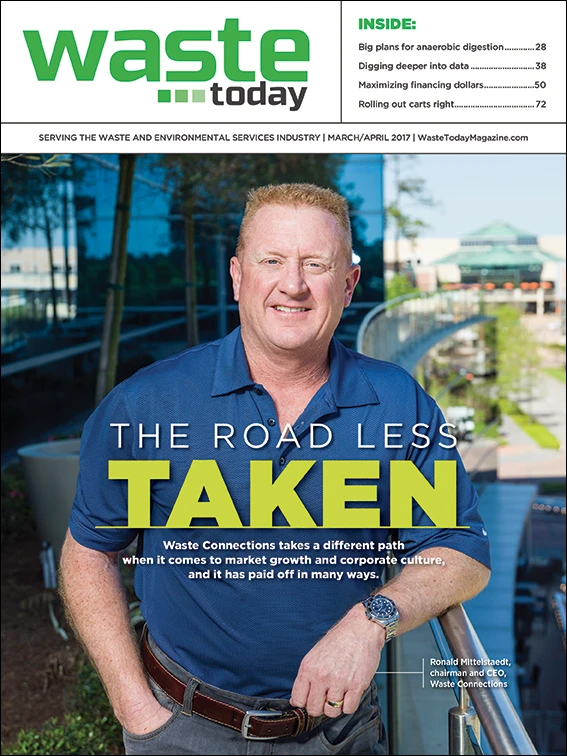
Explore the March 2017 Issue
Check out more from this issue and find your next story to read.
Latest from Waste Today
- Hoffman Sanitation Services acquires Wildhorse Waste Services
- US Tire Manufacturers Association supports legislation boosting tire retreading
- Vanguard AD installation goes online in Wisconsin
- Struggling with excess wood debris?
- More of what the world needs, less of what it doesn’t
- Gaeta Recycling: Driving efficiency and sustainability with SENNEBOGEN material handlers
- Enhance mobility using Sebright Products Portable Compactor Solutions
- Drive operational efficiency with Sebright Products Oil Filter Recycler